So i've been trying to come up with a way to build a decent looking, well performing 5" quad frame.
The aspiration was to do it at home, with basic tools and inexpensive materials in the FT model - so others could maybe follow. I'd seen the UBMQ project here - which is fantastic, but I didn't want to get into 3d printing and really wanted a more H/X style-top mount battery situation - to get all "juicy" or whatever nonsense...
Inititally I started with the HMB 235 and then Versacopter's construction concepts to build on.
I came up with a design to cut from HDPE using a hole and hacksaw but the precision required was not feasible and the material too heavy and flexible to achieve decent performance. I really did try with this one - cut out two bottom plates spent ages filing / rasping but it was hooooorible.
I also tried a development of the versacopter - splicing it with David's mini tricopter frame and using his booms and motor mounts. I called it the boom quad. After a bit of modelling and thinking i quit this for a few reasons. All those tasty swedish carbon booms were getting expensive - the plate designs were looking time consuming to cut, ESC mounting was an issue and also the prop line was ending up adjacent to the top plate and I was worried about clearance / propstrikes to the big ol' go pro up front (this was pre-Session 5/Runcam 3 times...feels like a lifetime right!?).
At this point I took a step back - I looked deeper into the frames i really liked the look of, the ones the youtube guy's fly, the ones that allow for a variety of internal set ups, the ones that are durable / maintainable. Guess what...
Alien 5"
QAV-R
MQC-Fusion
Dronewolf PUP II
The designer in me capitulated to the idea of DIY, even to originality. Maybe just playing with these designs and sucking it up an forking out for CNC carbon would be enough of an adventure, that's before you even get into the components and soldering / mounting / tuning and flying.
So I draw some stuff and some more stuff and go to all the UK CNC Carbon cutters i can find, and... the prices are ridiculous - £150 for a unibody design in 4mm and 1.4mm carbon. So I take a break and consider buying a Martian II.
I don't.
Then I find a CNC place in china on instagram - i send them a drawing of an alien style frame - the price difference is remarkable, but... minimum order is for 10 frames ($120) and a one off prototype is $70 inc. shipping.
Then i stumble across Armattan Productions...give it a shot I think, see what the prices come back like....
Not only are the prices excellent per item (only slightly more than the instagram CNC people) - there is no minimum order - what they are offering is pretty amazing. Sure the website is clunky but it does work. Make an account - upload files - wait for approval (48hrs) - then you can buy it - someone in Taiwan will cut it and send it to you (takes about a month including shipping time). You can make the design public, add a commission, set up a store, potentially make a little money.
If you want.
So here's the design. Whilst its not original in design terms and owes everything to the big shot frames out there - I like the look of it, i enjoyed the process and i did kinda do it myself...
225mm motor to motor
4mm arms (16mm wide) - keyed together at centre
2mm bottom plate and arm brace - you can mount the arms underneath or on top of the bottom plate
1.5mm camera plates for a Runcam Swift 2 including angle set screw - braced tight into standoffs to add strength.
1.5mm top plate - flat/clean spot for GoPro mounting
X truss cutouts to lighten top and bottom plates whilst distributing forces into standoffs
35mm standoffs.
Cost of carbon cutting and shipping £32 ($38)
The carbon arrived at the weekend - 89 grams - very smooth cut - i have some components on order - in lots of ways the journey is just beginning and i'm going to need your help...
The aspiration was to do it at home, with basic tools and inexpensive materials in the FT model - so others could maybe follow. I'd seen the UBMQ project here - which is fantastic, but I didn't want to get into 3d printing and really wanted a more H/X style-top mount battery situation - to get all "juicy" or whatever nonsense...
Inititally I started with the HMB 235 and then Versacopter's construction concepts to build on.
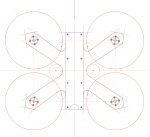
I came up with a design to cut from HDPE using a hole and hacksaw but the precision required was not feasible and the material too heavy and flexible to achieve decent performance. I really did try with this one - cut out two bottom plates spent ages filing / rasping but it was hooooorible.
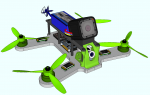
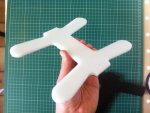
I also tried a development of the versacopter - splicing it with David's mini tricopter frame and using his booms and motor mounts. I called it the boom quad. After a bit of modelling and thinking i quit this for a few reasons. All those tasty swedish carbon booms were getting expensive - the plate designs were looking time consuming to cut, ESC mounting was an issue and also the prop line was ending up adjacent to the top plate and I was worried about clearance / propstrikes to the big ol' go pro up front (this was pre-Session 5/Runcam 3 times...feels like a lifetime right!?).
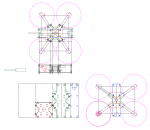
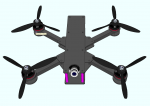
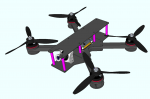
At this point I took a step back - I looked deeper into the frames i really liked the look of, the ones the youtube guy's fly, the ones that allow for a variety of internal set ups, the ones that are durable / maintainable. Guess what...
Alien 5"
QAV-R
MQC-Fusion
Dronewolf PUP II
The designer in me capitulated to the idea of DIY, even to originality. Maybe just playing with these designs and sucking it up an forking out for CNC carbon would be enough of an adventure, that's before you even get into the components and soldering / mounting / tuning and flying.
So I draw some stuff and some more stuff and go to all the UK CNC Carbon cutters i can find, and... the prices are ridiculous - £150 for a unibody design in 4mm and 1.4mm carbon. So I take a break and consider buying a Martian II.
I don't.
Then I find a CNC place in china on instagram - i send them a drawing of an alien style frame - the price difference is remarkable, but... minimum order is for 10 frames ($120) and a one off prototype is $70 inc. shipping.
Then i stumble across Armattan Productions...give it a shot I think, see what the prices come back like....
Not only are the prices excellent per item (only slightly more than the instagram CNC people) - there is no minimum order - what they are offering is pretty amazing. Sure the website is clunky but it does work. Make an account - upload files - wait for approval (48hrs) - then you can buy it - someone in Taiwan will cut it and send it to you (takes about a month including shipping time). You can make the design public, add a commission, set up a store, potentially make a little money.
If you want.
So here's the design. Whilst its not original in design terms and owes everything to the big shot frames out there - I like the look of it, i enjoyed the process and i did kinda do it myself...
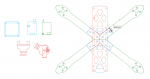
225mm motor to motor
4mm arms (16mm wide) - keyed together at centre
2mm bottom plate and arm brace - you can mount the arms underneath or on top of the bottom plate
1.5mm camera plates for a Runcam Swift 2 including angle set screw - braced tight into standoffs to add strength.
1.5mm top plate - flat/clean spot for GoPro mounting
X truss cutouts to lighten top and bottom plates whilst distributing forces into standoffs
35mm standoffs.
Cost of carbon cutting and shipping £32 ($38)
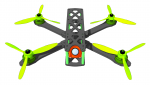
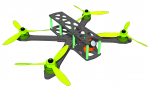
The carbon arrived at the weekend - 89 grams - very smooth cut - i have some components on order - in lots of ways the journey is just beginning and i'm going to need your help...
Last edited: