quorneng
Master member
The conventional approach to a lightweight plane wing is to use 'stick and tissue'.
Such a structure can be equalled using foam, particularly with thin sheet Depron, and it can be more robust too.
More out of curiosity than any likely benefit I wondered what could be done if the structure was not made of sticks of wood but from 3D printed parts.
I have already used printed ribs quite successfully with almost no weight penalty compared to even a foam rib.
This rib for an 8" (200 mm) chord wing printed in PLA weighs 1.2 g
The big question is would a spar printed in PLA be strong enough and how could a 1 m spar be printed with a bed limitation of 220 mm?
The first issue was to recognise that a printed structure is much stronger along the line of the filament than across it so it would be important that the print ran along the line of the spar.
All printer filament is heavy compared to balsa a hollow 'box' spar would provide strength and rigidity for minimum weight.
A 200 mm 'test' spar section carrying an 18 oz (500 g) centre load load with no visible distortion.
The spar itself weighs only 7.8 g
So far so good but how would it behave if 5 of these were joined end to end to create a 1000 mm spar?
Hmmmm!
Such a structure can be equalled using foam, particularly with thin sheet Depron, and it can be more robust too.
More out of curiosity than any likely benefit I wondered what could be done if the structure was not made of sticks of wood but from 3D printed parts.
I have already used printed ribs quite successfully with almost no weight penalty compared to even a foam rib.
This rib for an 8" (200 mm) chord wing printed in PLA weighs 1.2 g
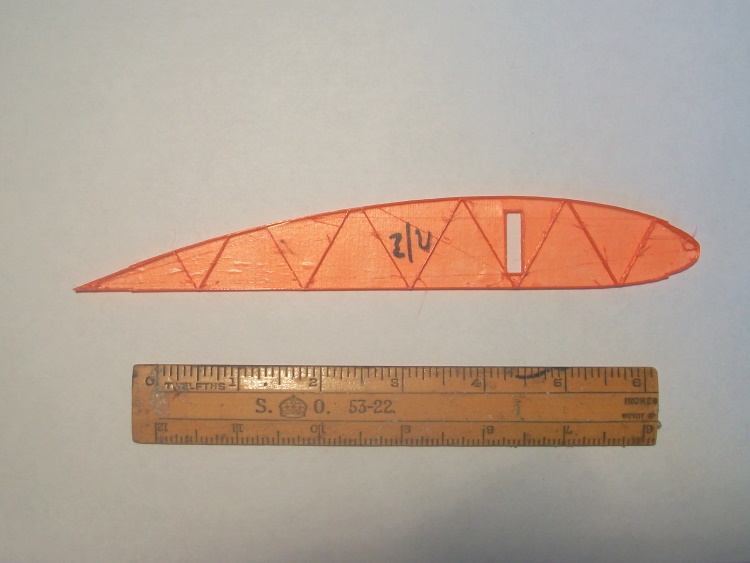
The big question is would a spar printed in PLA be strong enough and how could a 1 m spar be printed with a bed limitation of 220 mm?
The first issue was to recognise that a printed structure is much stronger along the line of the filament than across it so it would be important that the print ran along the line of the spar.
All printer filament is heavy compared to balsa a hollow 'box' spar would provide strength and rigidity for minimum weight.
A 200 mm 'test' spar section carrying an 18 oz (500 g) centre load load with no visible distortion.
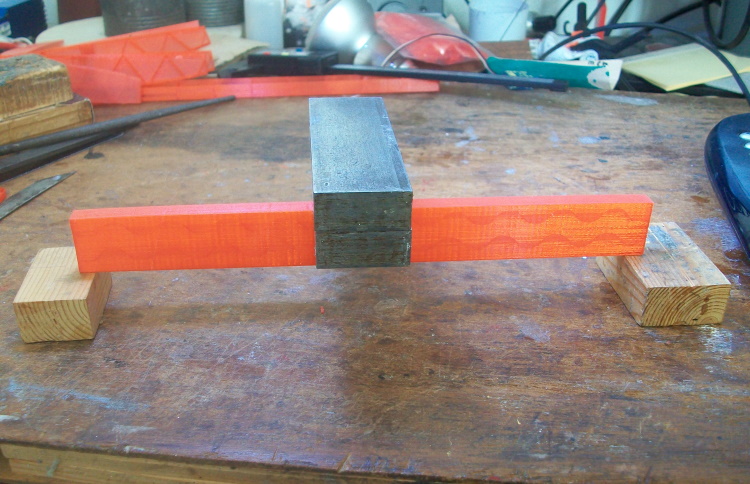
The spar itself weighs only 7.8 g
So far so good but how would it behave if 5 of these were joined end to end to create a 1000 mm spar?
Hmmmm!