quorneng
Master member
The joys of own design printing to very tight limits, both in dimensions and weight and it was still not quite right.
As soon as you complete one you find a detail that would make it better and/or lighter.
The only plus is they are very light so use little filament. Each only weighs 6 g that's about 2.5 m of filament.
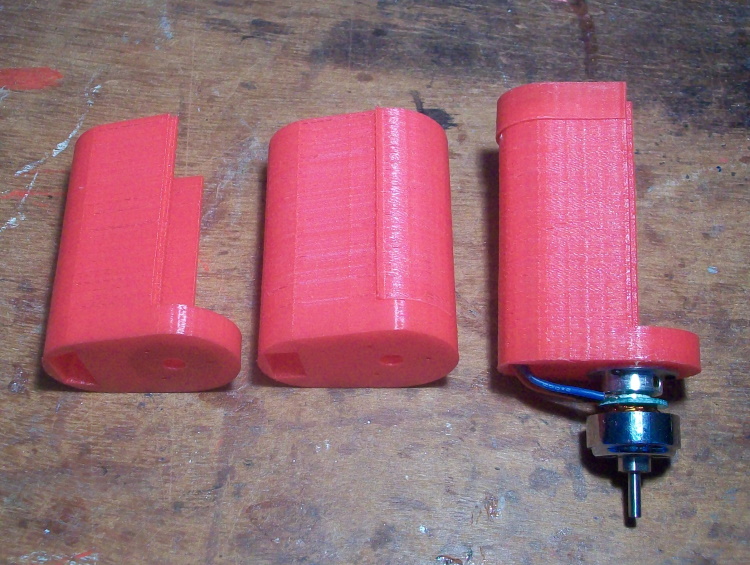
As soon as you complete one you find a detail that would make it better and/or lighter.
The only plus is they are very light so use little filament. Each only weighs 6 g that's about 2.5 m of filament.