kulens
Member
Planes are my main interest, but looking at the episodes while building quadcopters triggered my curiosity. My first experience with quadcopters was the inductrix. But it didn't took long that I converted it into the tiny whoop.
So 2 months ago, I start wondering... why not build the versacopter. So I've ordered all the parts (luckily now available in Europe too via Graupner).
My setup:
I've chosen for an s-bus connection between the receiver and the naze32 FC.
The ESC's support BL-heli-s. The updates of the firmware went smooth, without any issues.
Pictures from my build:
Soldering the ESC's and the BEC:
Connecting the flight controller (Naze32) and the OrangeRX receiver via s.bus
Soldering the motors to the ESC's
Installation of the bars and mounting the motors:
Figuring out where to put each part inside the body:
Ready for a dry-run:
Ready for its maiden:
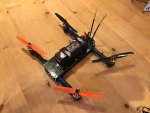
So 2 months ago, I start wondering... why not build the versacopter. So I've ordered all the parts (luckily now available in Europe too via Graupner).
My setup:
- motors: Scorpion M-2205-2350KV Brushless Outrunner
- ESC: Flycolor Raptor BLHeli-S 30A Multi-Rotor
- props: Gemfan 6030 Propellers
- Naze32 Rev6 Flight Controller
- OrangeRx R620X with s-bus
- Turnigy Graphene 2200mAh 4S 45C Lipo
- BEC (5v, 3Amp) from Graupner
I've chosen for an s-bus connection between the receiver and the naze32 FC.
The ESC's support BL-heli-s. The updates of the firmware went smooth, without any issues.
Pictures from my build:
Soldering the ESC's and the BEC:
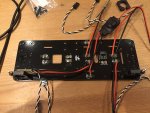
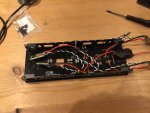
Connecting the flight controller (Naze32) and the OrangeRX receiver via s.bus
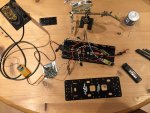
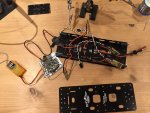
Soldering the motors to the ESC's
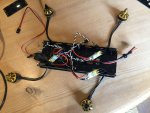
Installation of the bars and mounting the motors:
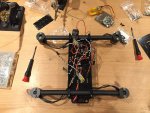
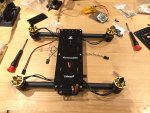
Figuring out where to put each part inside the body:
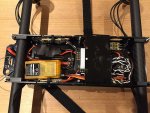
Ready for a dry-run:
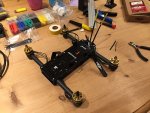
Ready for its maiden:
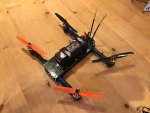