Learn how to solder thick gauge wire properly with today's Fast Tip! Whether you work with scratch build RC airplanes or you're just fixing up your RTF park flyer, this tip will come in handy!
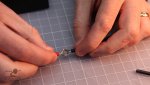
All you need to do is smash the two thick gauge wires together.
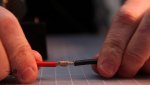
With speaker wire (or similar) wrap the thick gauge to creating a strong joint. This makes the connection very strong even before you solder.
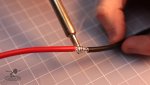
You'll need a solder iron that can heat properly solder your joint.
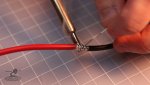
The solder will pull through the wire and create a very strong electrical connection!
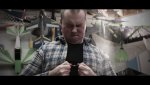
Did we mention this type of solder connection is strong!? Well, it is. We hope you enjoyed this Fast Tip!
Let us know if you have a cool tip, or better yet post it here on the website!