Robert S
Well-known member
The concept came to me, as most things do I imagine for most people, from multiple sources of inspiration. Some time last year, I added a Creality bed leveling sensor and upgraded to a direct drive on the ENDER V2. At some point, I bought some .2mm feeler gauges to use in order to set my nozzle height. Using paper always made me feel uncertain that I was at the correct height because I figured I was probably squishing the paper too much and, also I'm not sure what, "a slight drag" was supposed to feel like. I wanted something that was either going to slide under the nozzle or it wasn't... a more positive indicator I guess is what I'm trying to say. The gauges seemed to work just fine the one time I used it before I packed up my printer while I did some construction.
One day I was watching an episode of "This Old Tony" on You Tube (
) and observed a neat accessory on his milling machine that allowed him to set tool height zero automatically between tool changes. I thought that would be a convenient feature to have on a 3D printer. I would love to change my tip size more often so I could print things faster if the design allowed it , but I don't because its a pain to reset the z axis. Afterwards, the thought quickly slipped into the murky depths of my mind and was forgotten.
Fast forward a bit and last week and I found myself needing to change my tip to steel so I could print with carbon-fiber PLA. After the change, I needed to reset my Z Axis height. As I was doing it, it occurred to me that it was hard to see when the tip just touched the feeler gauge. I was dragging it back and forth and feeling for when it did and didn't go under the tip, but I wished that i could just drop the head down and see when the tip just barely touched the gauge.
Then "vola!" I had an idea, what if I used the continuity feature of my multi-meter. Could I put a probe on the gauge and then somewhere on the head so that when the two touched it just beeped at me? Would that work? So I tried it and "Yes... yes it does." I used it to set the z axis and tried a test print. I brought it down until it beeped and then I backed it off .01mm. I used the most problematic filament I had (some Olive Green Hatchbox stuff that I always have issues with) because I figured if I had good results with that stuff, everything ells would be good to go. Here is what I got...
I couldn't imagine that no one else had tried something like this so I googled it and was surprised that I didn't find much. I did find, "Inexpensive Piezoelectric Elements for Nozzle Contact Detection and Build Platform Leveling in FFF 3D Printers " by Michael Simpson and Simon Khoury (https://www.mdpi.com/257320). Same concept, but a far more elegant design executed by people who obviously have some skills far beyond my own. If I can find one of their piezoelectric sensors cheap, I might use a Arduino nano to make something easier to use and that I can just keep with the printer. I have some arduinos and it might be a fun project. For now though, I basically just integrated the game "Operation" into my 3D printer.
Anyways, here are some pictures. I can't film the operation while holding the camera. I'm sure people get the idea though. I just clipped the alligator clip test leads to the end of the wire soldered to the feeler gauge and the other to the top of extruder. When I first tried it, I just used the regular pointed probes as a proof of concept, but that meant I had to hold the probes in place while also manipulating everything ells so that's why I came up with the wire and alligator clips.
View attachment 20230721_124051.jpg View attachment 20230721_205754.jpg
Couple of notes:
- Make sure the tip is clean. No filament can be on the bottom of the tip preventing metal to metal contact.
- Tip and build table should be at temperature. The gauge will expand when it gets hot so compete the operation as fast as feasible. That being said, its not going to expand that much. Calipers tell me that my cheap .2mm amazon gauge at room temp is actually .16mm at room temp. After sitting on my heated bed for a minute, it grew to ~ .18mm. So in my case, the expansion actually helps to bring it closer into spec.
- Feeler gauges rust (at least the one I have do). Might want to put a very light coat of oil or WD40 on them although if a wire is soldered on like mine, the gauge must be oil free so the solder will adhere.
One day I was watching an episode of "This Old Tony" on You Tube (
Fast forward a bit and last week and I found myself needing to change my tip to steel so I could print with carbon-fiber PLA. After the change, I needed to reset my Z Axis height. As I was doing it, it occurred to me that it was hard to see when the tip just touched the feeler gauge. I was dragging it back and forth and feeling for when it did and didn't go under the tip, but I wished that i could just drop the head down and see when the tip just barely touched the gauge.
Then "vola!" I had an idea, what if I used the continuity feature of my multi-meter. Could I put a probe on the gauge and then somewhere on the head so that when the two touched it just beeped at me? Would that work? So I tried it and "Yes... yes it does." I used it to set the z axis and tried a test print. I brought it down until it beeped and then I backed it off .01mm. I used the most problematic filament I had (some Olive Green Hatchbox stuff that I always have issues with) because I figured if I had good results with that stuff, everything ells would be good to go. Here is what I got...
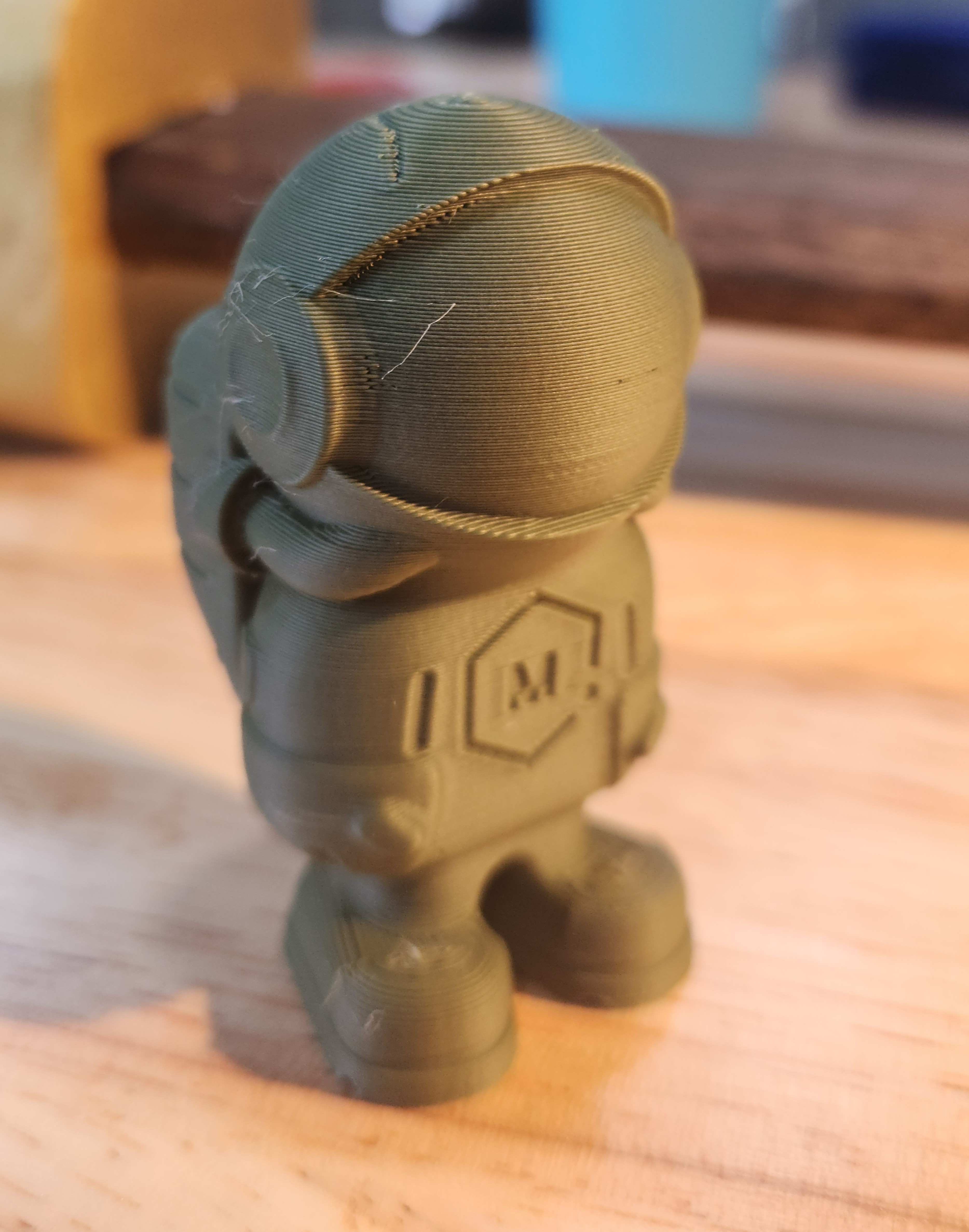
I couldn't imagine that no one else had tried something like this so I googled it and was surprised that I didn't find much. I did find, "Inexpensive Piezoelectric Elements for Nozzle Contact Detection and Build Platform Leveling in FFF 3D Printers " by Michael Simpson and Simon Khoury (https://www.mdpi.com/257320). Same concept, but a far more elegant design executed by people who obviously have some skills far beyond my own. If I can find one of their piezoelectric sensors cheap, I might use a Arduino nano to make something easier to use and that I can just keep with the printer. I have some arduinos and it might be a fun project. For now though, I basically just integrated the game "Operation" into my 3D printer.
Anyways, here are some pictures. I can't film the operation while holding the camera. I'm sure people get the idea though. I just clipped the alligator clip test leads to the end of the wire soldered to the feeler gauge and the other to the top of extruder. When I first tried it, I just used the regular pointed probes as a proof of concept, but that meant I had to hold the probes in place while also manipulating everything ells so that's why I came up with the wire and alligator clips.
View attachment 20230721_124051.jpg View attachment 20230721_205754.jpg
Couple of notes:
- Make sure the tip is clean. No filament can be on the bottom of the tip preventing metal to metal contact.
- Tip and build table should be at temperature. The gauge will expand when it gets hot so compete the operation as fast as feasible. That being said, its not going to expand that much. Calipers tell me that my cheap .2mm amazon gauge at room temp is actually .16mm at room temp. After sitting on my heated bed for a minute, it grew to ~ .18mm. So in my case, the expansion actually helps to bring it closer into spec.
- Feeler gauges rust (at least the one I have do). Might want to put a very light coat of oil or WD40 on them although if a wire is soldered on like mine, the gauge must be oil free so the solder will adhere.
Last edited: