Upon masking off my panels yesterday I made a great discovery, so lets get to it.
In the world of aviation there are three main ways of doing panels, as illustrated below. The first way is a simple butt joint. Two panels are butted together and riveted to the substructure. This has lower drag but increases weight as rivets are needed on both panels. The second way is panel overlap, where the panels are overlapped and single lines of rivets are used to secure them. This reduces weight but increases drag from the irregular surface. Both of these ways have their advantages and can be used in strategic ways for mass-produced aircraft. The THIRD way incorporates tooling and metal work to create a lip where there is panel overlap but the panels are butted to reduce drag AND weight. It is more complex and requires more machine work and is something that war-time aircraft may not have used due to ease of repair in the field and speed/cost of manufacture.
I made this realization while observing the following picture. The rivets are along the trailing edge and there is a single line of rivets showing that there is panel overlap. What did not make sense was that if there was panel overlap there the drag from the top panel would create a lip that would create more drag than if the fore panel was over top of the aft panel. Also note the slight gap at the "T" junction in the middle left of the image. This was the key indicator to me that what we are seeing is a lipped overlap.
I wanted to be sure that this method was used all around the panels and this image showed me the complexity of wood and metal construction that this aircraft faced. You can see that the fairings for the empennage are just overlapped and do not incorporate a machined lip. This is because the stabilizers are wood and the fairings are metal. So, in this area there is a simple overlap and a different modeling technique must be used.
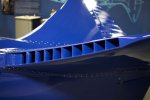