I'm continuing to have fun experimenting with more exotic filaments
After being impressed by Taulman 910 I decided to give string trimmer line a try. I've been looking for some to try locally since I got my v6 but haven't found any round in 1.75ish size, only in 3mm. Then it hit me...Amazon! As I mentioned back in early October I grabbed the cheapest roll of nylon trimmer line I could find off of Amazon for $3....it's not quite 1.75mm - 0.065" which is more like 1.6mm but I gave it a try:
First print worked...but wasn't spectacular:
The layer bonding was better than the Taulman 910...but surface finish was terrible. I suspected moisture was the issue. So decided to try drying it out. My wife has this "super dri-aid" from when she used in-the-ear hearing aids before switching to behind the ear:
https://www.amazon.com/Super-Dri-Hearing-Dehumidifier-Hal-Hen/dp/B000B7I8FQ So I took the lid off of it, and put it in a zip-loc with the trimmer line. Then I put it out in the backyard in the sun for a few days.
Re-printed the test with the same settings and got MUCH better results:
The photo doesn't show it well, but the new print was VERY nice while the original was fuzzy. The layer bonding wasn't as good but it still made very usable prints. It's not as strong as the 910 but it's a fraction of the price.
I printed a heart gear keychain in it and it came out wonderful - and is the first one of those I've printed that I'd actually consider using as a keychain since it's durable enough to survive my pocket
Like the Taulman it's "softer" as well as strong. I'll have to do a little video showing the heart gears printed in the various materials I've tried (ABS/PLA/PETG/Nylon) and how they compare....
And this week I finally decided to give TPU a try. I ordered a roll of Hatchbox off Amazon for just <$30 since it was the most affordable TPU I found. Oddly enough Hatchbox says it print it at 190-210 even though my research online shows most TPU should be printed at 230-250. Most sources also said to use a 60 degree heated bed...but I went with 70 since some said to run it hotter.
My first test was at 200c and the bed at 70c with PVA gluestick. It printed amazingly well:
One of the cleanest first prints I've ever had! Oddly enough though it was very slightly underextruded even though I expected it to be slightly overextruded based on my slicer settings. (I had my filament diameter set to 1.70 even though it measures 1.75...well...kind of...more in a second.) I was expecting 0.48mm walls and got 0.46mm instead...Not perfect but pretty darn close. The layer adhesion is crazy strong. And the flexibility is ridiculous:
The material itself is very...weird. That's really the best I can put it. It's almost like a rubber band. Feeding it into my extruder was a bit tricky, but thankfully the extruder I'm using is fairly well suited to flexible filaments since there's very little space between the PTFE tube and the drive gear:
That was actually one of the reasons I started using this extruder in the first place, it's just taken longer than I anticipated for me to get some flexible filament
Back to the weird. I mentioned that it measured 1.75mm pretty accurately...but it actually doesn't. It's not very round at all. At almost any point on the filament I can measure it at 1.75mm...but twist the calipers a bit and it's not. I don't think it's that the filament wasn't extruded well..it's just that it's soft and has taken a bit of a set from being wound on the spool and then put in a vac bag. I wonder if this is why I got slight underextrusion when I was expecting overextrusion.
The tensile strength also appears to be very strong. I extruded some into the air to purge my nozzle and then stretched it and holy cow did it stretch a lot before breaking. it did turn white and loose it's elasticity, but took a lot more stretching after that before actually breaking.
It also isn't sticking to my elmers purple glue stick as well as I expected. I may try some hair spray or blue tape with it. My first test stuck fine while printing...but immediately after before the bed could really cool it came off just by touching it. My second test a stretchlet (
http://www.thingiverse.com/thing:13505) didnt' stick at all and just made a mess. My third attempt (the stretchlet again) failed but was a slicer failure...for some reason sli3er does not slice that model well and leaves big gaps

A fresh coat of glue stick kept it on just fine.
Fourth attempt I tried a different stretchlet (
http://www.thingiverse.com/thing:445476) and tried something else new printing it in spiral vase mode. It came out great. Sorry I don't have any photos but it's gorgeous. No seam, smooth layers...stretchy...just perfect. And again fresh glue stuck it fine.
Really looking forward to experimenting with this material some more. I want to tackle printing a RC car or tank and will use this for the tires or treads

I'm also curious to see how it does printing more "solid" objects. I know a lot of people like it for FPV camera mounts and pods....but the
pod I'm designing on my 3D printed quad is structural so I don't think this would work for it:
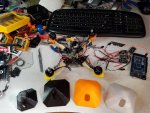