I had a request to show an update online of my progress on ANOTHER project I have going. Awhile ago I built a 1/6 scale SE5a that met its demise while encountering a light pole at a park. This was when I realized my eyesight was going a little and my depth perception was the issue. I wanted another one and decided to build another but lighter! Building lighter will allow for more challenges with building and allow for additional scale features. Fine by me!
First we have the makings of the landing gear and wheels. Landing gear is coat hangar wire that has been soldered to shape. Fairings are DTFB attached with gorilla glue and covered in tissue and WBPU. Ready for paint. Wheels will be DTFB core with PVC on the outside to help support the axle tube. Tire is a section of a gasket I salvaged. It is neoprene. You can also see in this picture three of the four interplane (IP) struts that go on the wings. These are coat hangar wire again and will be fared the same way as the landing gear.
Here is another image of the landing gear. Scrap tissue but once painted you will never see the printed portions.
WINGS! Yes, each piece was hand cut. The spar is DTFB and I may reinforce with carbon fiber. I wanted the scale ribs as well as the sub-ribs on the leading edge. Much more work to be done there. The bottom wing has a covering of posterboard that will be glassed for hardness for a better mount to the fuselage bottom. All four ailerons will be driven by a single servo in the bottom wing. I'll explain that as I get there. The top wing has the majority of the cap strips in place. These are scale and reinforcing. They give rigidity to the wing and serve to give the scale rib stitching once covered in doculam. The strips are 110# card stock that has had thread glued to it in a horizontal pattern at the scale spacing. I have to make more so I will explain how I did that when I make more. Wings are roughly 53" in span.
Last night I started on the fuselage. Here are the formers cut out and the bottom with markings for where the formers are to be glued. This worked well the last time and I will modify the engine location to mount the battery in the TOP of the fuselage rather than the bottom. A hatch will be cut (obviously) but the ease of battery connection is my main concern there.
I salvaged the V-stab/rudder and the H-stab/elevators from the last plane. Single layer of DTFB with hard balsa at the hinge points. Covered in tissue and WBPU and hinged with strips of solartex scraps I had laying around. Control surfaces are pull-pull style to help keep the back end light. Spider wire fishing line is my line of choice for this as it is SUPER light and strong. It also does not expand and slack when the summer heat is on. You can also see the hard balsa tail skid in this shot. Also salvaged from the old plane.
Power will be a Tacon Bigfoot 15 motor and a 40A Detrum ESC swinging an old timer top flite 13.5x4 wood prop. Shooting for room for a 2200 mAh 3S battery for very long flight times on this setup. Lots of thrust... no speed. 5-9g servos. Will probably go with a metal gear 9g on the ailerons. I should have plenty of room for my 1/6 scale full-body pilot. I'll keep posting as I build along.
First we have the makings of the landing gear and wheels. Landing gear is coat hangar wire that has been soldered to shape. Fairings are DTFB attached with gorilla glue and covered in tissue and WBPU. Ready for paint. Wheels will be DTFB core with PVC on the outside to help support the axle tube. Tire is a section of a gasket I salvaged. It is neoprene. You can also see in this picture three of the four interplane (IP) struts that go on the wings. These are coat hangar wire again and will be fared the same way as the landing gear.
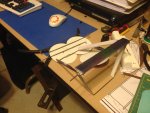
Here is another image of the landing gear. Scrap tissue but once painted you will never see the printed portions.
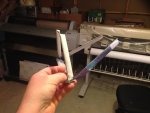
WINGS! Yes, each piece was hand cut. The spar is DTFB and I may reinforce with carbon fiber. I wanted the scale ribs as well as the sub-ribs on the leading edge. Much more work to be done there. The bottom wing has a covering of posterboard that will be glassed for hardness for a better mount to the fuselage bottom. All four ailerons will be driven by a single servo in the bottom wing. I'll explain that as I get there. The top wing has the majority of the cap strips in place. These are scale and reinforcing. They give rigidity to the wing and serve to give the scale rib stitching once covered in doculam. The strips are 110# card stock that has had thread glued to it in a horizontal pattern at the scale spacing. I have to make more so I will explain how I did that when I make more. Wings are roughly 53" in span.
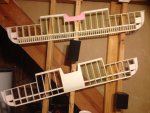
Last night I started on the fuselage. Here are the formers cut out and the bottom with markings for where the formers are to be glued. This worked well the last time and I will modify the engine location to mount the battery in the TOP of the fuselage rather than the bottom. A hatch will be cut (obviously) but the ease of battery connection is my main concern there.

I salvaged the V-stab/rudder and the H-stab/elevators from the last plane. Single layer of DTFB with hard balsa at the hinge points. Covered in tissue and WBPU and hinged with strips of solartex scraps I had laying around. Control surfaces are pull-pull style to help keep the back end light. Spider wire fishing line is my line of choice for this as it is SUPER light and strong. It also does not expand and slack when the summer heat is on. You can also see the hard balsa tail skid in this shot. Also salvaged from the old plane.
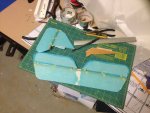
Power will be a Tacon Bigfoot 15 motor and a 40A Detrum ESC swinging an old timer top flite 13.5x4 wood prop. Shooting for room for a 2200 mAh 3S battery for very long flight times on this setup. Lots of thrust... no speed. 5-9g servos. Will probably go with a metal gear 9g on the ailerons. I should have plenty of room for my 1/6 scale full-body pilot. I'll keep posting as I build along.