tamuct01
Well-known member
"Background"
I embarked a few weeks back on what I think is a fairly ambitious project. I’ve long been a fan of the Bell Boeing V-22 Osprey. For those not familiar, the V-22 is an “American multi-mission, tiltrotor military aircraft with both vertical takeoff and landing (VTOL), and short takeoff and landing (STOL) capabilities. It is designed to combine the functionality of a conventional helicopter with the long-range, high-speed cruise performance of a turboprop aircraft.” (Wikipedia: https://en.wikipedia.org/wiki/Bell_Boeing_V-22_Osprey)
I’ve studied a few commercially produced V-22 radio control (RC) models, but they all seem to come up short. In the cases I studied serious design concessions were made to control costs and the model did not properly reproduce the real-world functionality of the V-22. Here are a couple of my observations:
E-flite V-22 Osprey VTOL BNF Basic 487mm
(https://www.horizonhobby.com/v-22-osprey-vtol-bnf-basic-efl9650)
Horizon Hobby, the makers of E-flite, are incredibly popular with RC enthusiasts. They have an extensive line of RC models for land, water, and air operations. I’m not sure of their market cap, but they are probably the largest RC manufacturer in the world.
On the surface, this model looks pretty good. It has a foam body with working tilting proprotors and the price is fairly reasonable. ($230 at the time of this writing for the BNF basic). However, closer examination reveals some significant flaws:
Rotormast V-22 Osprey
(https://www.rotormast.com/)
Rotormast is a small niche producer of scale V-22 kits. This model is much larger than the E-flite version and features working collective and cyclic pitch inputs. Each proprotor control utilizes a helicopter-style swashplate. The mixing of control inputs is done via a proprietary flight control package.
This is a much more realistic model, but still has some limitations:
A while back an RC club member gave me a box of parts for the Blade mCPX BL (https://www.horizonhobby.com/mcp-x-bl-bnf-with-as3x®-technology-blh3980)
This helicopter is now discontinued, but parts are still available. In the box of parts were enough components to build 2 complete models with many parts to spare. I figure that with these parts I should be able to construct an RC model of the V-22 at a very low cost.
(https://aggiehobbies.blogspot.com/2019/05/v-22-osprey-project-background.html)
I embarked a few weeks back on what I think is a fairly ambitious project. I’ve long been a fan of the Bell Boeing V-22 Osprey. For those not familiar, the V-22 is an “American multi-mission, tiltrotor military aircraft with both vertical takeoff and landing (VTOL), and short takeoff and landing (STOL) capabilities. It is designed to combine the functionality of a conventional helicopter with the long-range, high-speed cruise performance of a turboprop aircraft.” (Wikipedia: https://en.wikipedia.org/wiki/Bell_Boeing_V-22_Osprey)
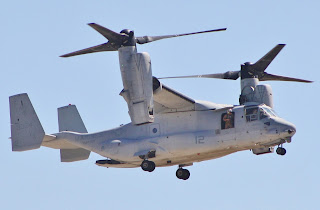
I’ve studied a few commercially produced V-22 radio control (RC) models, but they all seem to come up short. In the cases I studied serious design concessions were made to control costs and the model did not properly reproduce the real-world functionality of the V-22. Here are a couple of my observations:
E-flite V-22 Osprey VTOL BNF Basic 487mm
(https://www.horizonhobby.com/v-22-osprey-vtol-bnf-basic-efl9650)
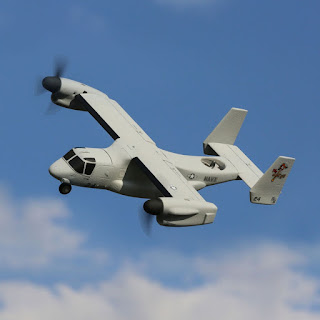
Horizon Hobby, the makers of E-flite, are incredibly popular with RC enthusiasts. They have an extensive line of RC models for land, water, and air operations. I’m not sure of their market cap, but they are probably the largest RC manufacturer in the world.
On the surface, this model looks pretty good. It has a foam body with working tilting proprotors and the price is fairly reasonable. ($230 at the time of this writing for the BNF basic). However, closer examination reveals some significant flaws:
- The main rotors are FAR too small. On the real Osprey, the rotor blades are so large that landing in airplane mode would cause the rotor blades to strike the ground. It appears that this model is using some high-KV motors requiring the use of smaller props. They may have also decided that for beginners having small props that would not strike the ground when landing as an airplane was an acceptable trade-off
- The main rotors are fixed-pitch blades and not capable of cyclic or collective pitch inputs. For details on how helicopter inputs work, there is a really good article on Wikipedia (https://en.wikipedia.org/wiki/Swashplate_(aeronautics)
- There is a 3rd propeller in the center-aft of the model. In order to provide stabilization in hover mode, E-Flite has added a small 3rd propeller in the rear to provide pitch control to the model. On the real V-22, this control is provided through the cyclic pitch of the proprotors.
Rotormast V-22 Osprey
(https://www.rotormast.com/)
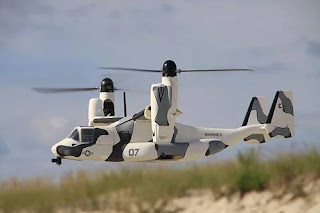
Rotormast is a small niche producer of scale V-22 kits. This model is much larger than the E-flite version and features working collective and cyclic pitch inputs. Each proprotor control utilizes a helicopter-style swashplate. The mixing of control inputs is done via a proprietary flight control package.
This is a much more realistic model, but still has some limitations:
- Price. Kits range from $1400 to $1750 depending on the desired scale look. This is out of my price range at this time.
- The controls on this model are done entirely with the collective and cyclic pitch of the proprotors. There are no traditional flight controls (aileron, elevator, rudder) in forward flight. As the model transitions from hover to forward flight the flight controller changes how control inputs are translated to the swashplate controls.
A while back an RC club member gave me a box of parts for the Blade mCPX BL (https://www.horizonhobby.com/mcp-x-bl-bnf-with-as3x®-technology-blh3980)
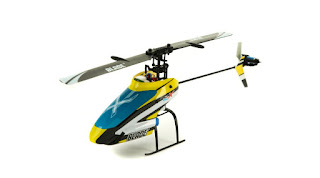
This helicopter is now discontinued, but parts are still available. In the box of parts were enough components to build 2 complete models with many parts to spare. I figure that with these parts I should be able to construct an RC model of the V-22 at a very low cost.
(https://aggiehobbies.blogspot.com/2019/05/v-22-osprey-project-background.html)
Last edited: