quorneng
Master member
Sad to say but I lost my original very successful Endurance.
Too high and too far away I briefly lost sight of it when 'edge on' in a turn and I never saw it again.
Drat!
The 'follow on' Super Endurance
Flies well enough but demonstrated conclusively that cheap Li-ion batteries actually have nothing like (only about 15%!!) the capacity it 'says on the tin'!
Unfortunately 'quality' Li-ion cells end up considerably more expensive than the equivalent capacity LiPo.
The original Endurance was developed over quite a period of time with many changes so I wondered if I sat down and re-designed it from scratch might it be possible to do even better?
So in the best traditions of a movie follow on - Endurance II
with the same battery, motor, 48" span and as a similar pylon wing pod and boom pusher.
First the wing.
Using Depron it is possible to build a wing with swept up turned tips as used by most 'moulded' foamies. Now is this design aerodynamically more efficient or is it done simply because it is possible to do it cheaply and it looks neat. In theory a wing that controls and limits the tip vortex can be more efficient as it behaves as if it had a higher aspect ratio so the proposed Endurance II wing.
Light with a broad chord to give a low wing loading.
Something else I have wanted to try is 'direct acting' ailerons with no linkage whatsoever. Mechanically efficient and with nothing 'dangling in the breeze'!
It will also use a V tail.
Such an arrangement means virtually none of the airframe is directly in the relatively fast moving prop wash so it should reduce the drag.
Will it all actually make any difference?
I have my doubts so I will just have to build it and see.
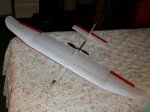
Too high and too far away I briefly lost sight of it when 'edge on' in a turn and I never saw it again.
The 'follow on' Super Endurance
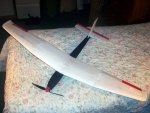
Flies well enough but demonstrated conclusively that cheap Li-ion batteries actually have nothing like (only about 15%!!) the capacity it 'says on the tin'!
Unfortunately 'quality' Li-ion cells end up considerably more expensive than the equivalent capacity LiPo.
The original Endurance was developed over quite a period of time with many changes so I wondered if I sat down and re-designed it from scratch might it be possible to do even better?
So in the best traditions of a movie follow on - Endurance II
First the wing.
Using Depron it is possible to build a wing with swept up turned tips as used by most 'moulded' foamies. Now is this design aerodynamically more efficient or is it done simply because it is possible to do it cheaply and it looks neat. In theory a wing that controls and limits the tip vortex can be more efficient as it behaves as if it had a higher aspect ratio so the proposed Endurance II wing.
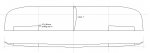
Light with a broad chord to give a low wing loading.
Something else I have wanted to try is 'direct acting' ailerons with no linkage whatsoever. Mechanically efficient and with nothing 'dangling in the breeze'!
It will also use a V tail.
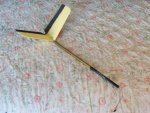
Such an arrangement means virtually none of the airframe is directly in the relatively fast moving prop wash so it should reduce the drag.
Will it all actually make any difference?
I have my doubts so I will just have to build it and see.