Hi, I've just joined the forum so hello, I've been in the hobby about 1 year.
I must admit first off I'm a pretty lousy pilot, but I really got hooked on building. I've done a couple of Flite Test kits, but prefer working with insulation board, and own designs.
I recently tried to build a conventional, mid-wing, and it was (for my low skill level) a real handful, and I was wondering if anybody could give me some pointers. Of course "this plane is too much for your skill level" is probably completely fair, but I wanted to check if I made design faults as well.
It was a rectangular mid-wing, 80cm*14cm, which I called "the V1" due to it's very simple shape and lack of canopy. Weight was 295g (originally), and it had a 2200 motor on 3S battery. Wing loading would then be about 8.6 oz/sq.ft US.
It flew, but very twitchy, especially in pitch. It may be that I had not yet discovered "expo" on my radio, but the throws looked reasonable, like 10mm. What I noticed on the first flight was that I was all over the place the first minute, trying to keep it level without crashing, but once I somehow "found the envelope" I flew several patterns fairly reasonably, but still with a lot of pitching associated with turns, if I didn't modulate the thrust perfectly smoothly with the banking and yanking. I swooped in nicely for a landing at about 3ft off the deck, held it there to bleed off speed, and it stalled very abruptly straight down, breaking a prop. Still, I thought not bad for a first flight.
What I noticed thinking about the design, that I had a quite large tail area (about 1/3 of wing area), the fuselage was rather long. Also, the tail was more or less in line with the main wing vertically, so perhaps in the wake of the main? Also, the tail plane was angled up respective the fuselage, and the other wing, and not down as I think should be correct.
After that, I installed trike undercarriage and a nose wheel servo coupled to the rudder, and was pleased to be able to do a take off run and get airborne. Of course the plane was 20g-25g heavier. But now the plane was a real handful, it would (I think, my eyesight's not great at distance) suddenly tip-stall possibly and get into a dive before I could correct it. Wings had zero downwash angle so maybe that was it.
I thought the balance was a bit tail heavy when I first built it (but think the U/C would have made it more nose heavy), but still, I also tried a bit bigger battery in the nose. I flew a couple of more times, it was like a bucking bronco in pitch, really hard work to stop it diving or rolling. This was strange for me, because I thought that usually tail-heavy planes would behave in this way, but all the mods I made were making it nose heavier, and it was getting worse.
Anyway I gave up and worked on a delta for a while, which flies great but a bit too quick! But I wanted to try and work out what went wrong with my conventional plane for future designs.
Thanks to anyone who read this far, I attach a picture of the machine, and hope that some experts out there can give me a couple of pointers.
Ed.
I must admit first off I'm a pretty lousy pilot, but I really got hooked on building. I've done a couple of Flite Test kits, but prefer working with insulation board, and own designs.
I recently tried to build a conventional, mid-wing, and it was (for my low skill level) a real handful, and I was wondering if anybody could give me some pointers. Of course "this plane is too much for your skill level" is probably completely fair, but I wanted to check if I made design faults as well.
It was a rectangular mid-wing, 80cm*14cm, which I called "the V1" due to it's very simple shape and lack of canopy. Weight was 295g (originally), and it had a 2200 motor on 3S battery. Wing loading would then be about 8.6 oz/sq.ft US.
It flew, but very twitchy, especially in pitch. It may be that I had not yet discovered "expo" on my radio, but the throws looked reasonable, like 10mm. What I noticed on the first flight was that I was all over the place the first minute, trying to keep it level without crashing, but once I somehow "found the envelope" I flew several patterns fairly reasonably, but still with a lot of pitching associated with turns, if I didn't modulate the thrust perfectly smoothly with the banking and yanking. I swooped in nicely for a landing at about 3ft off the deck, held it there to bleed off speed, and it stalled very abruptly straight down, breaking a prop. Still, I thought not bad for a first flight.
What I noticed thinking about the design, that I had a quite large tail area (about 1/3 of wing area), the fuselage was rather long. Also, the tail was more or less in line with the main wing vertically, so perhaps in the wake of the main? Also, the tail plane was angled up respective the fuselage, and the other wing, and not down as I think should be correct.
After that, I installed trike undercarriage and a nose wheel servo coupled to the rudder, and was pleased to be able to do a take off run and get airborne. Of course the plane was 20g-25g heavier. But now the plane was a real handful, it would (I think, my eyesight's not great at distance) suddenly tip-stall possibly and get into a dive before I could correct it. Wings had zero downwash angle so maybe that was it.
I thought the balance was a bit tail heavy when I first built it (but think the U/C would have made it more nose heavy), but still, I also tried a bit bigger battery in the nose. I flew a couple of more times, it was like a bucking bronco in pitch, really hard work to stop it diving or rolling. This was strange for me, because I thought that usually tail-heavy planes would behave in this way, but all the mods I made were making it nose heavier, and it was getting worse.
Anyway I gave up and worked on a delta for a while, which flies great but a bit too quick! But I wanted to try and work out what went wrong with my conventional plane for future designs.
Thanks to anyone who read this far, I attach a picture of the machine, and hope that some experts out there can give me a couple of pointers.
Ed.
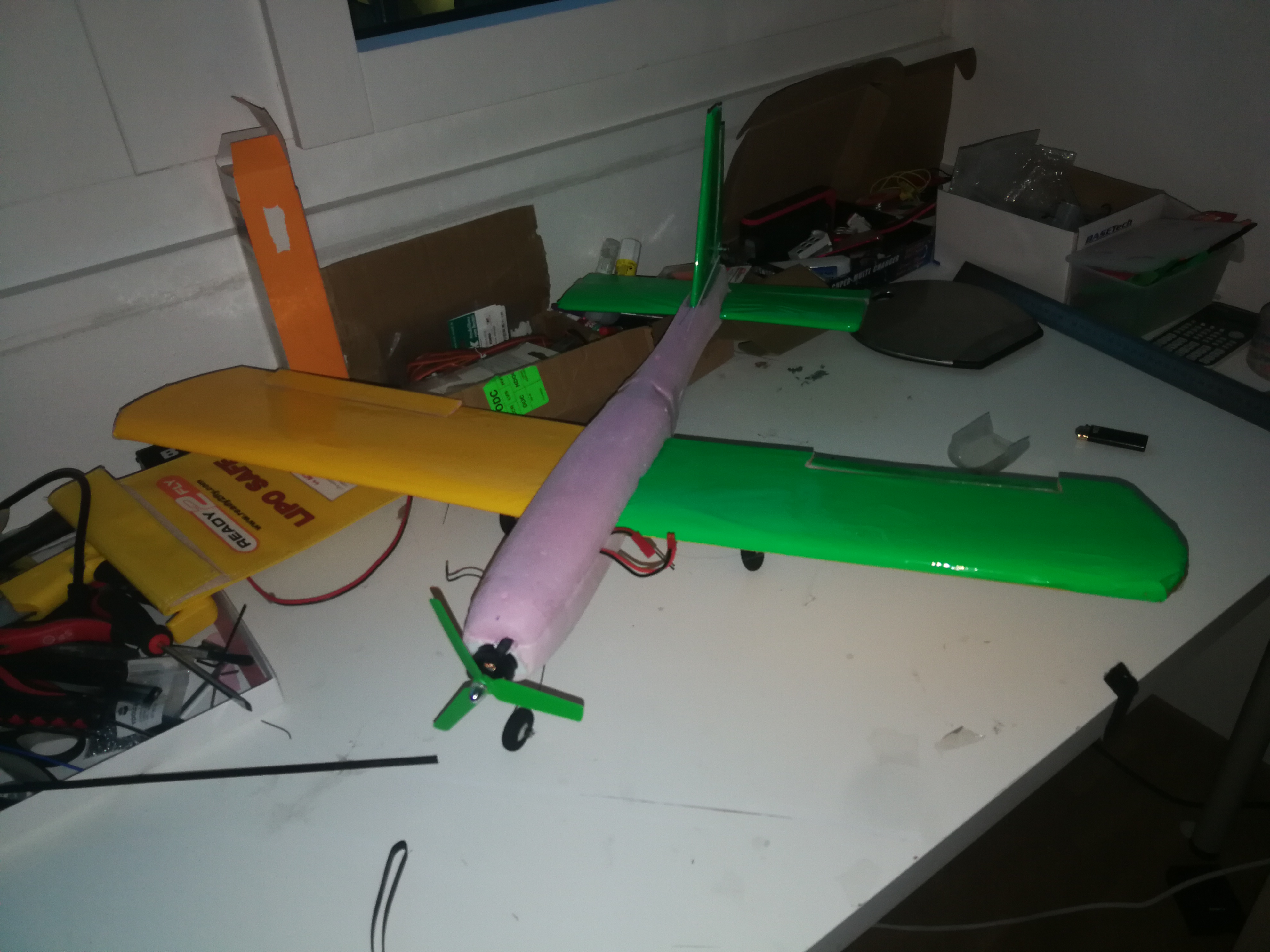