FlyMike
New member
I searched but did not see any topics for 3D printed parts, planes, etc. Though I have been blind to things in front of my face before. So forgive me if its been done before.
I thought it would be great to have a thread for everyone to share their RC related 3D models, or even just cool things they have found online that may be useful to others.
I have a few models on Thingiverse I recently uploaded, but 2 of them I would like to throw out into this forum for people to test out if they have access to a 3D printer.
The Skewer Pushrod Fitting. Have not tested in flight yet, but seems to work well on the bench.
https://www.thingiverse.com/thing:2519626
And the Servo Mounting Clip. This one was already shared in my hello message in the new section, but I thought it was worth sharing in a normal thread also.
https://www.thingiverse.com/thing:2516174
Let me know if you test out any of my parts and how it turned out for you.
Now here's a few Things I found that I think are impressive that I didn't model, but will probably print.
Landing gear bracket. Simple design using zip ties, Its perfect.
https://www.thingiverse.com/thing:1076800
RC Switch Lock. I always use a throttle kill switch. This is perfect for it.
https://www.thingiverse.com/thing:2440350
FT Transmitter limiters. I thought it was cool someone modeled them.
https://www.thingiverse.com/thing:1537448
Gotta have a pilot for any open top aircraft.
https://www.thingiverse.com/thing:485324
Please share anything you've made, or just really like.
I have a few more models I am working on that are new ideas I will probably share here in the near future.
I thought it would be great to have a thread for everyone to share their RC related 3D models, or even just cool things they have found online that may be useful to others.
I have a few models on Thingiverse I recently uploaded, but 2 of them I would like to throw out into this forum for people to test out if they have access to a 3D printer.
The Skewer Pushrod Fitting. Have not tested in flight yet, but seems to work well on the bench.
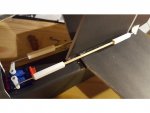
https://www.thingiverse.com/thing:2519626
And the Servo Mounting Clip. This one was already shared in my hello message in the new section, but I thought it was worth sharing in a normal thread also.
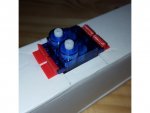
https://www.thingiverse.com/thing:2516174
Let me know if you test out any of my parts and how it turned out for you.
Now here's a few Things I found that I think are impressive that I didn't model, but will probably print.
Landing gear bracket. Simple design using zip ties, Its perfect.
https://www.thingiverse.com/thing:1076800
RC Switch Lock. I always use a throttle kill switch. This is perfect for it.
https://www.thingiverse.com/thing:2440350
FT Transmitter limiters. I thought it was cool someone modeled them.
https://www.thingiverse.com/thing:1537448
Gotta have a pilot for any open top aircraft.
https://www.thingiverse.com/thing:485324
Please share anything you've made, or just really like.
I have a few more models I am working on that are new ideas I will probably share here in the near future.