FlyingTyger
Elite member
The Great Planes Electro Streak was a plane that always caught my eye when I would page through the Tower Hobbies catalog as a kid. Electrics were something I never really explored until the advent of lipo batteries and brushless motors. At that point the Electro Streak kit was gone or at least off of my radar. When The RC Plane Lab Podcast announced that they were going to host an Electro Streak group build, I thought it would be the perfect time to satisfy my childhood desire to have one. It would also be a very convenient opportunity to do a foam build alongside several balsa builds and see how the two techniques compare.
I started by cutting the wing ribs from DTFB (paper removed). I left a section of foam attached to the bottom of each rib and trimmed them to be a consistent distance from the wing's centerline. This way they were able to be spot glued to my bench and everything would be aligned.
I noticed that the R2 rib did not line up with the fuse sides which would limit the twisting strength of the wing connection. I opted to leave the R2 ribs out and added perpendicular webs between R1 & R3 that will then bear on the fuse sides in the saddle.
1/8" x 1/4" balsa spars were added along with foam shear webs.
With the internal framework complete, I glued down the top wing skins.
Once dry, I will be able to break the ribs free from that bottom spacer and work on the bottom.
I started by cutting the wing ribs from DTFB (paper removed). I left a section of foam attached to the bottom of each rib and trimmed them to be a consistent distance from the wing's centerline. This way they were able to be spot glued to my bench and everything would be aligned.
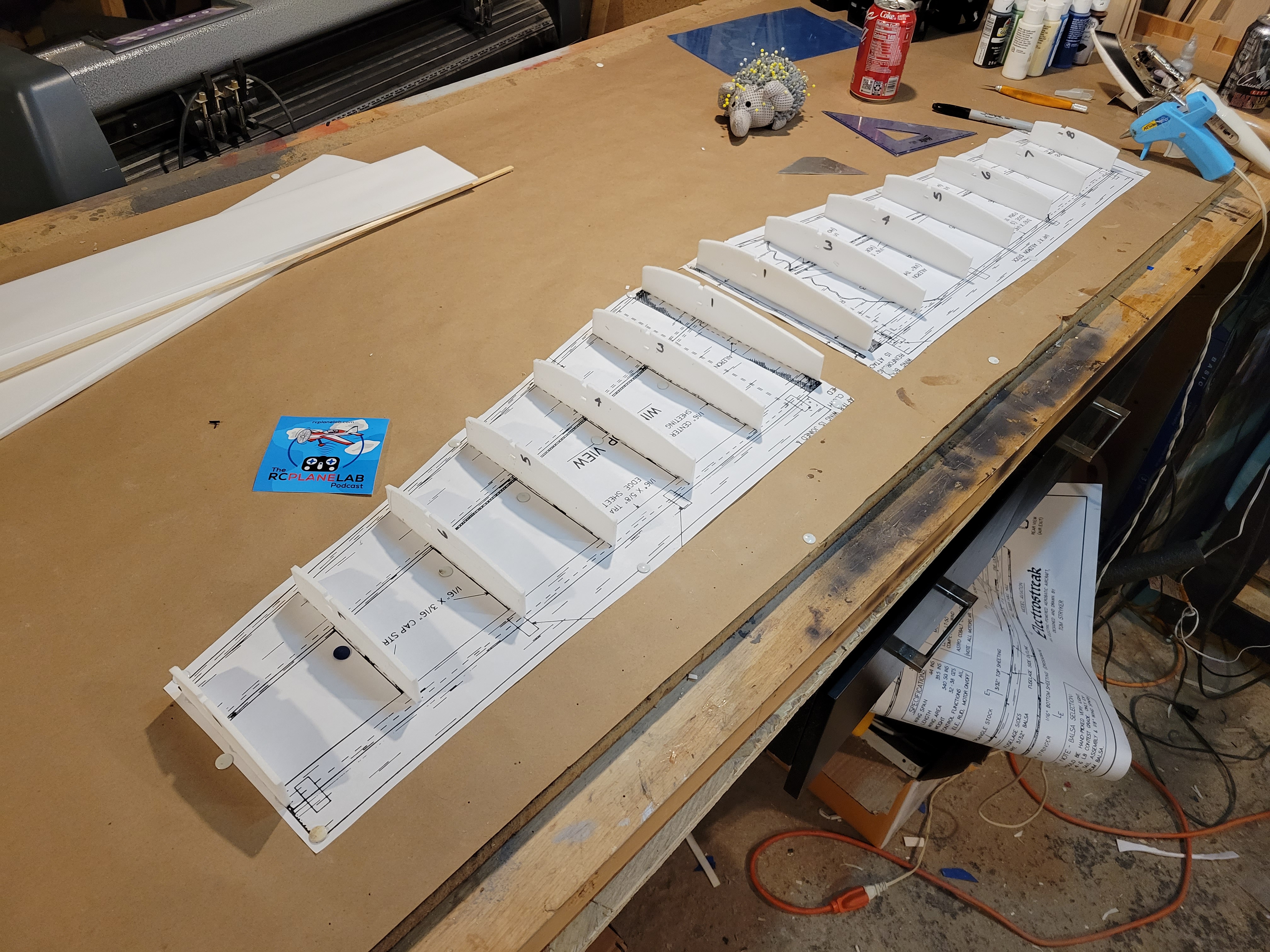
I noticed that the R2 rib did not line up with the fuse sides which would limit the twisting strength of the wing connection. I opted to leave the R2 ribs out and added perpendicular webs between R1 & R3 that will then bear on the fuse sides in the saddle.
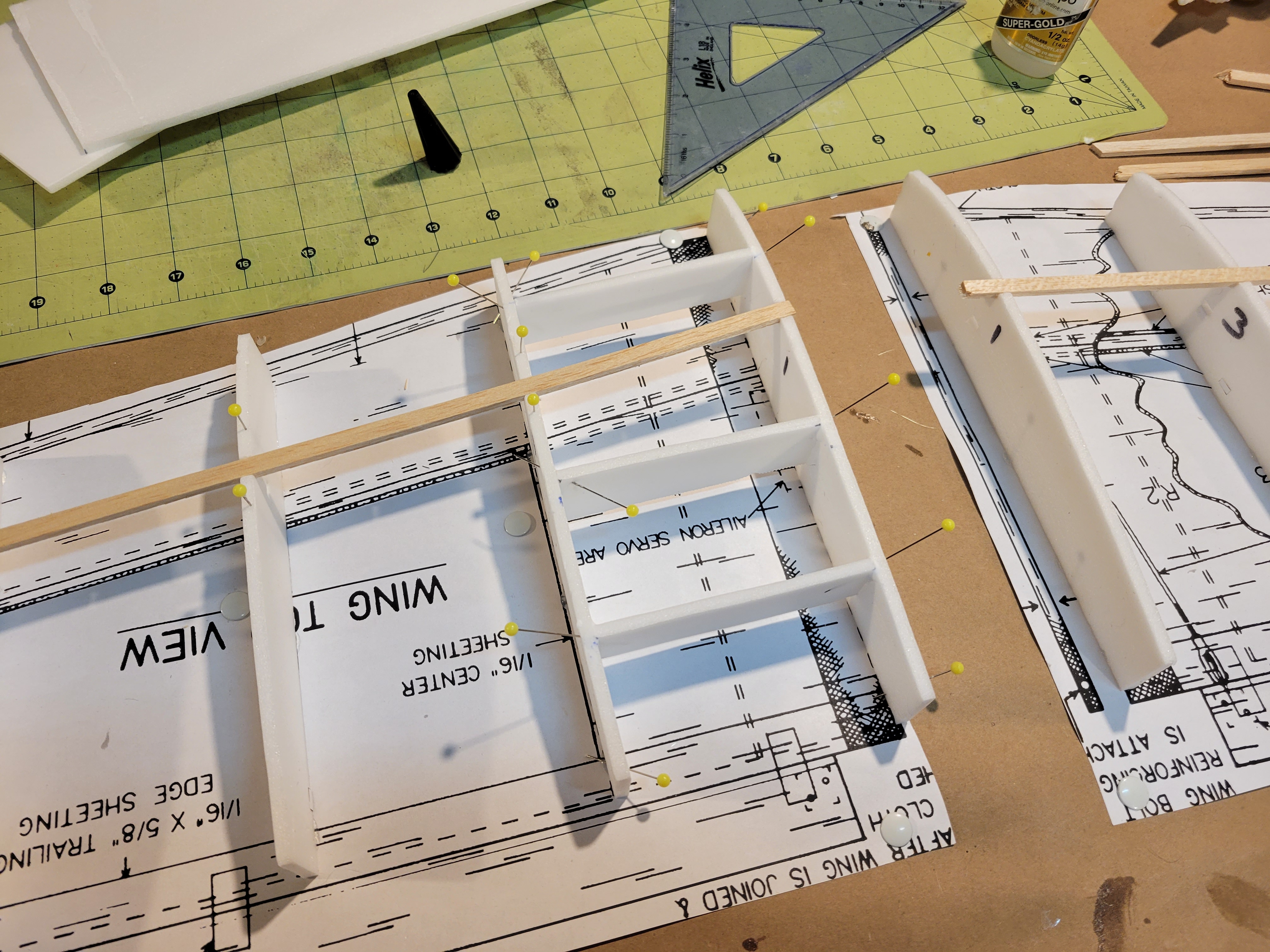
1/8" x 1/4" balsa spars were added along with foam shear webs.
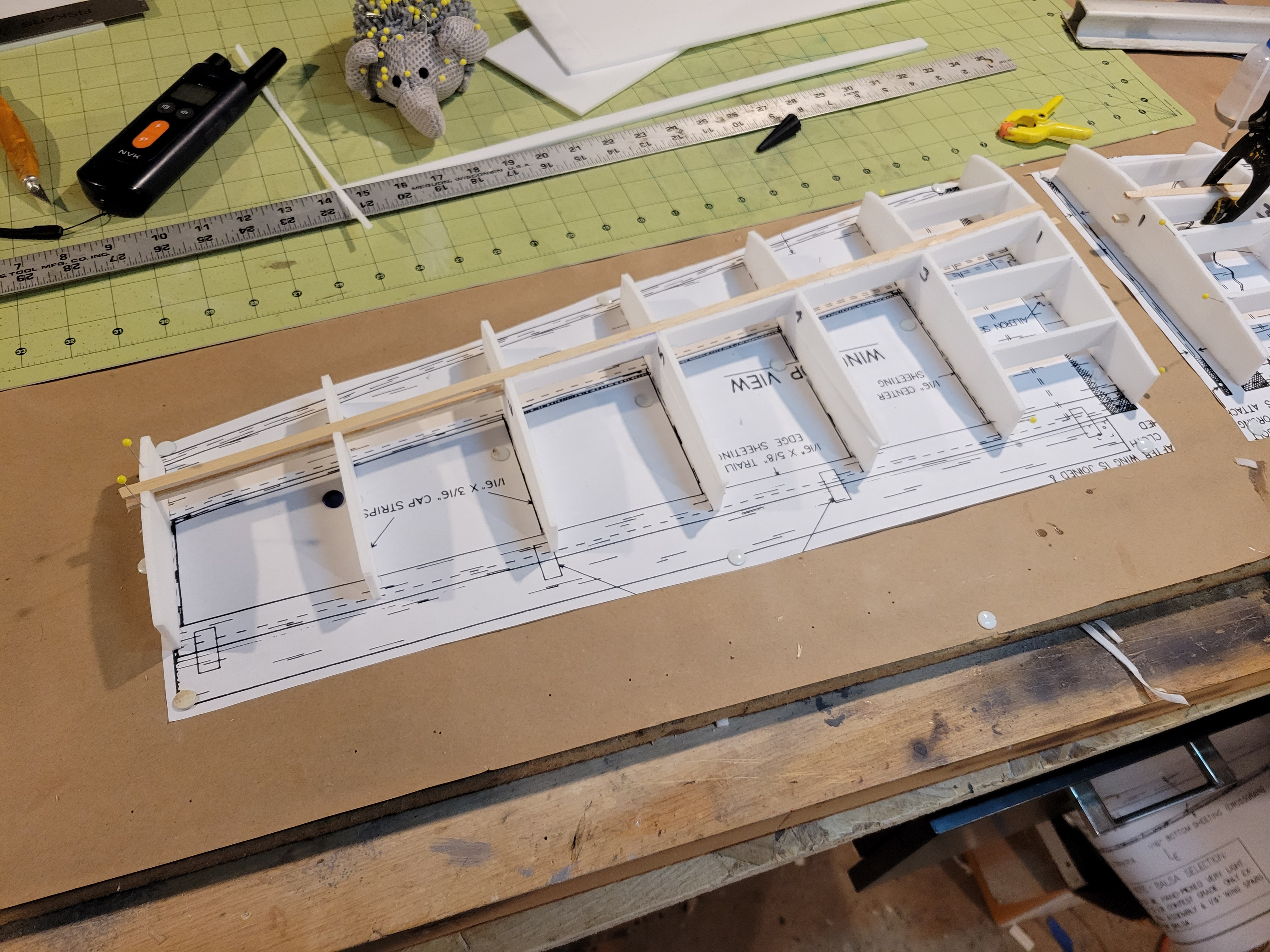
With the internal framework complete, I glued down the top wing skins.
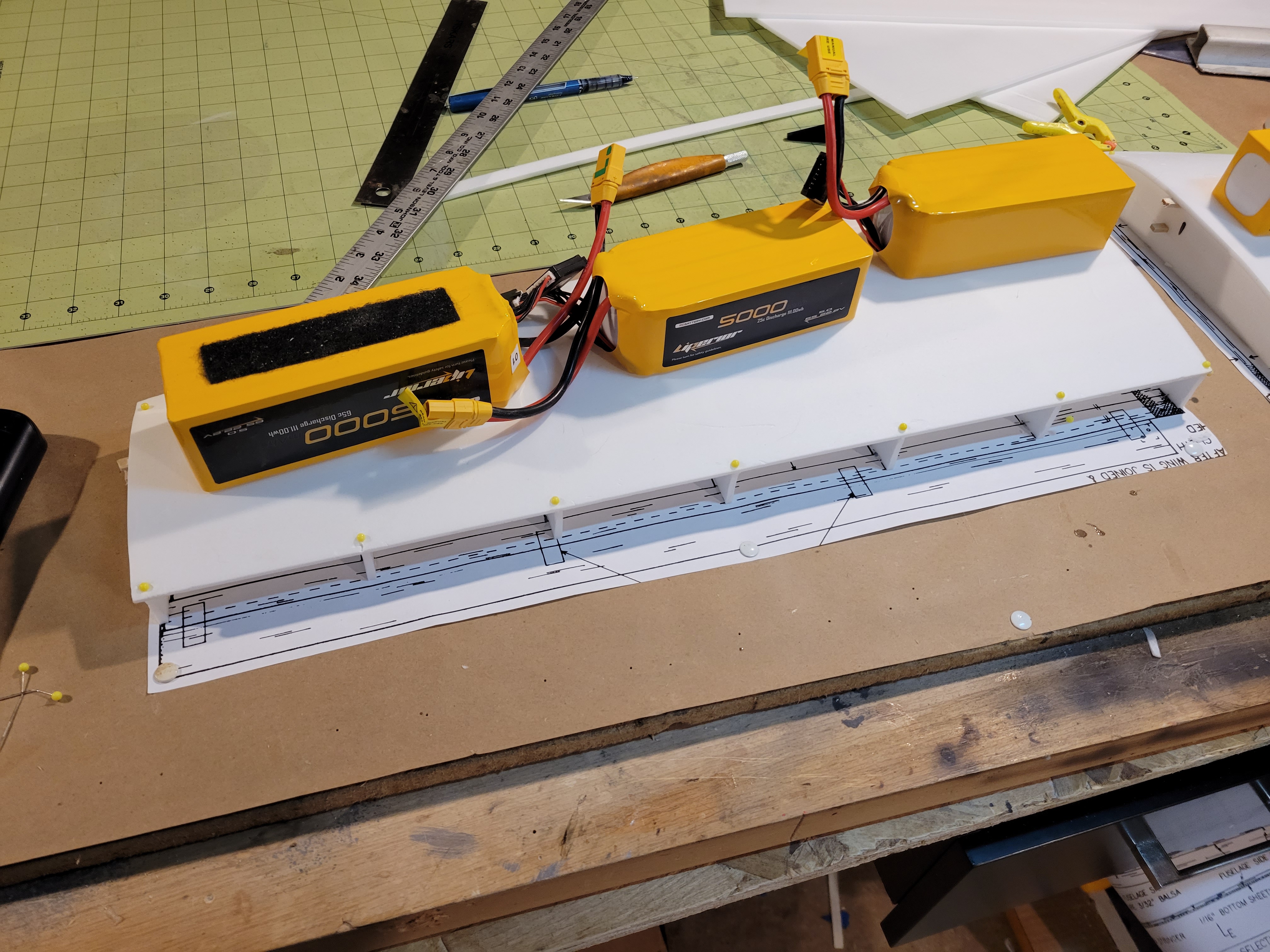
Once dry, I will be able to break the ribs free from that bottom spacer and work on the bottom.