breedatrad
New member
Good day, all,
I've had an FLSUN QQ-S 3D Printer for a year now and really like it. It's fast and makes great parts. Here's some sample parts I made with stock machine settings. They printed first time with no stringing or adjustments necessary.
Now, I'd like to start printing some of my own designs. What wall thickness have you guys been using for wing skins, airfoil ribs/supports, fuselage sides, etc?
Is there a thread that addresses these things or... How do I find out the current state of the art in 3D Printed, aircraft design?
Thanks!
Brian
I've had an FLSUN QQ-S 3D Printer for a year now and really like it. It's fast and makes great parts. Here's some sample parts I made with stock machine settings. They printed first time with no stringing or adjustments necessary.
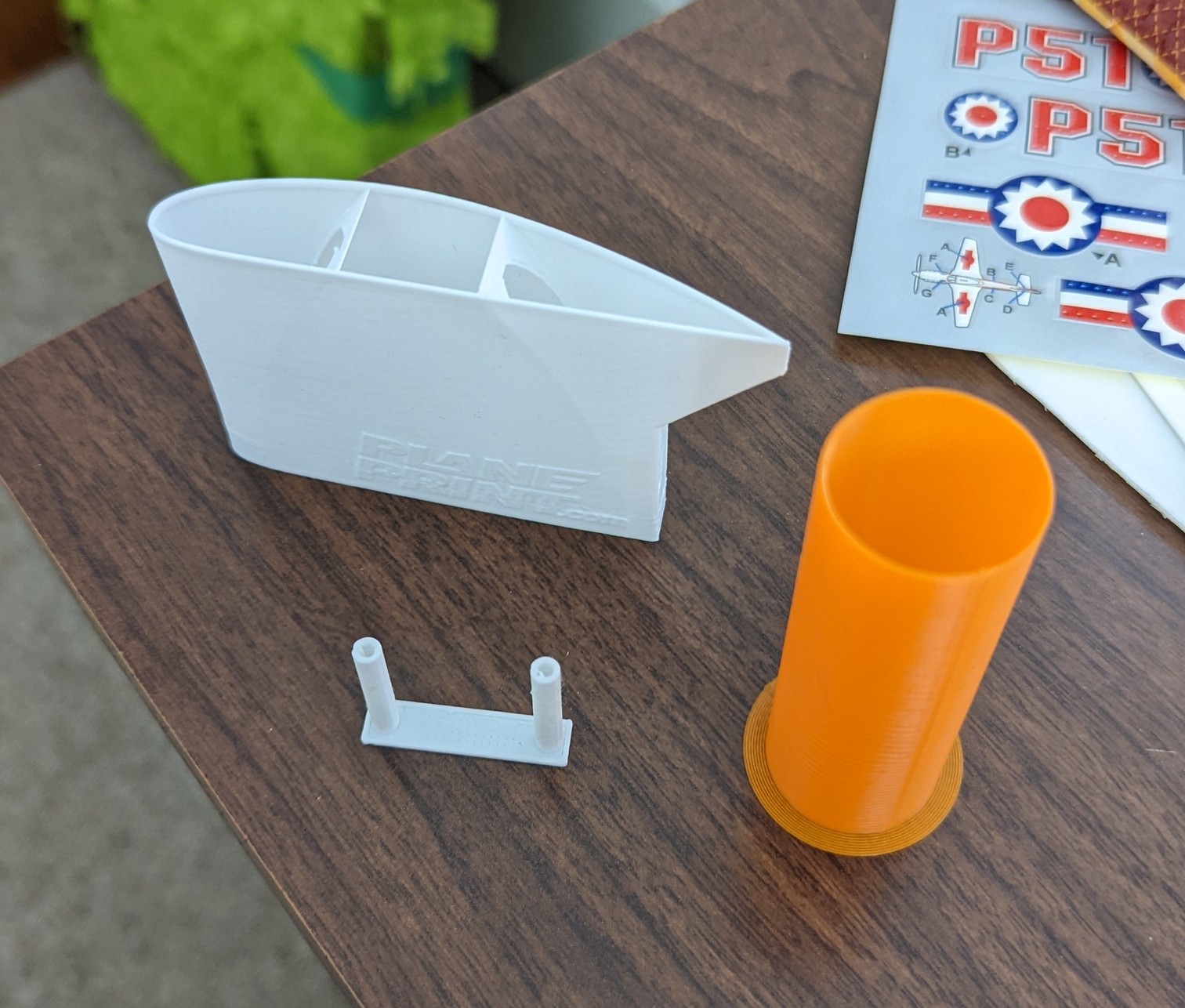
Now, I'd like to start printing some of my own designs. What wall thickness have you guys been using for wing skins, airfoil ribs/supports, fuselage sides, etc?
Is there a thread that addresses these things or... How do I find out the current state of the art in 3D Printed, aircraft design?
Thanks!
Brian