Hi, a while ago I found this alternative concept to making a gantry setup for cnc:
http://goodenoughcnc.eu/hybrid-cnc/
I really like the straightforwardness of the concept. The square tubes line up everything nice and perfectly square horisontally, and make for nice and wide rolling surfaces for the trolleys.
I was wondering if anyone in here has seen this or perhaps even tried it? Opinions on the construction?
I've already started a build myself, so far planned to be modified in 4 (or maybe 5) ways:
1) frame size will be 900x1200mm - this should supposedly give me a workable area of approx. 665x1000mm, making it possible to utilize most of a 700x1000mm sheet of depron. Nearly all the "depron" I use is 500x1000x6mm Climapor sheets, so the width is less of an issue. And the box table I plan to put under the gantry should also be able to take a 1200x800mm standard sheet of plywood this way, while still keeping the width down a bit, as my workshop space isn't all that huge. I plan to make the table flippable, so the bottom of the box will double as a work surface when the CNC is not in use. Should also help with cleaning the box out
.
2) I plan to add an extra X- and Z-axis assemblyy to one of the 900mm end tubes, as it is fairly straightforward to do. This should enable me to do cnc foam cutting as well, locking the Y-axis in place and adding hotwire guides to the ends of respective Z-axes.
3)I'll use proper Angular contact ball bearings for the Z-axis in stead of the proposed standard radial 608ZZ ones. Bit of a no-brainer in my opinion, since I can get those bearings easily locally - maybe not something everyone can....the apparently "everywhere-obtainable" 608ZZ's will properly do great for all the rest.
4) I'm using 40x40x2mm AISI316 stainless for the frame in stead of the spec'ed 40x40x3mm ordinary steel ones, so I won't have to keep the frame lubed or coated to avoid it rusting (In Denmark everyone practically lives on the ocean shore, at least with regard to salt in the air
), and to save a little weight. I haven't really done the math, but I'm betting on the higher "stiffness(?)" of the stainless to about even out the reduction in wall thickness.....also, it cuts the price of the stainless a bit.
5) I am also contemplating lengthening the 2 Z-axes a bit; I am considering ~100mm extra, giving me about 250mm of movement with the Z-axis assembly total height growing to 400mm. Partly because I already have the materials to do so at hand, so it won't really cost me any extra, partly because of my wish to incorporate the cnc hotwire ability. I am not all that worried with regard to the accuracy for depron or hotwire cutting, but I am a little concerned about the impact on accuracy for milling and 3D-printing. Any inputs on this?
My progress so far is:
- Sorting out drawings and build instructions, parts availability and cost.
- I've obtained, cut and drilled the steel tubes for the frame, I have cut out all the other steel parts for the trolleys(100x100x3x130mm steel tubes) and belt tighteners(from the leftover stainless tubing).
Next will be marking and drilling the 4 trolley tubes, which is probably going to be the most critical part.
http://goodenoughcnc.eu/hybrid-cnc/
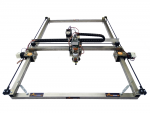
I really like the straightforwardness of the concept. The square tubes line up everything nice and perfectly square horisontally, and make for nice and wide rolling surfaces for the trolleys.
I was wondering if anyone in here has seen this or perhaps even tried it? Opinions on the construction?
I've already started a build myself, so far planned to be modified in 4 (or maybe 5) ways:
1) frame size will be 900x1200mm - this should supposedly give me a workable area of approx. 665x1000mm, making it possible to utilize most of a 700x1000mm sheet of depron. Nearly all the "depron" I use is 500x1000x6mm Climapor sheets, so the width is less of an issue. And the box table I plan to put under the gantry should also be able to take a 1200x800mm standard sheet of plywood this way, while still keeping the width down a bit, as my workshop space isn't all that huge. I plan to make the table flippable, so the bottom of the box will double as a work surface when the CNC is not in use. Should also help with cleaning the box out
2) I plan to add an extra X- and Z-axis assemblyy to one of the 900mm end tubes, as it is fairly straightforward to do. This should enable me to do cnc foam cutting as well, locking the Y-axis in place and adding hotwire guides to the ends of respective Z-axes.
3)I'll use proper Angular contact ball bearings for the Z-axis in stead of the proposed standard radial 608ZZ ones. Bit of a no-brainer in my opinion, since I can get those bearings easily locally - maybe not something everyone can....the apparently "everywhere-obtainable" 608ZZ's will properly do great for all the rest.
4) I'm using 40x40x2mm AISI316 stainless for the frame in stead of the spec'ed 40x40x3mm ordinary steel ones, so I won't have to keep the frame lubed or coated to avoid it rusting (In Denmark everyone practically lives on the ocean shore, at least with regard to salt in the air
5) I am also contemplating lengthening the 2 Z-axes a bit; I am considering ~100mm extra, giving me about 250mm of movement with the Z-axis assembly total height growing to 400mm. Partly because I already have the materials to do so at hand, so it won't really cost me any extra, partly because of my wish to incorporate the cnc hotwire ability. I am not all that worried with regard to the accuracy for depron or hotwire cutting, but I am a little concerned about the impact on accuracy for milling and 3D-printing. Any inputs on this?
My progress so far is:
- Sorting out drawings and build instructions, parts availability and cost.
- I've obtained, cut and drilled the steel tubes for the frame, I have cut out all the other steel parts for the trolleys(100x100x3x130mm steel tubes) and belt tighteners(from the leftover stainless tubing).
Next will be marking and drilling the 4 trolley tubes, which is probably going to be the most critical part.
Last edited: