Our local Wal-Mart finally started stocking the 88-cent Ross foamboard, so I picked up some sheets to try out. I decided to take off the paper and build a 3D profile plane. I found a cool design by a forum user called "Matchless" on flyinggiants.com. It's based on the JUKA, a full-scale aerobatic prototype designed by Lithuanian pilot Jurgis Kairys in 2004 and still flying today:
(photo by Flicker user joolsgriff, March 2019)
The plans I'm working from can be found here: https://www.flyinggiants.com/forums/attachment.php?attachmentid=80089&d=1198020057
The original plans were for an indoor plane made with 3mm Depron, with 33-inch wingspan and an all-up weight on the order of 145g. The Ross foamboard is 5mm and I don't have an indoor space, so I beefed everything up and went for a heavier outdoor build. The current version comes to 185g including a 2s 450mAh battery. Here's a photo:
The airframe is something of a work in progress at the moment. Results with the Ross foamboard have been mixed. On the positive side, it's very light and dimensionally consistent with the paper removed, unlike the wavy, unevenly-thick foamboard that Adams has been turning out in recent years. But unfortunately the Ross foam is quite floppy. It ends up needing as much carbon reinforcement as EPP, but without the durability of EPP. I decided to forge ahead anyhow. I figure once this one crashes, I can take the electronics and carbon bits and cut a new airframe out of 5mm EPP.
More to come!
(photo by Flicker user joolsgriff, March 2019)
The plans I'm working from can be found here: https://www.flyinggiants.com/forums/attachment.php?attachmentid=80089&d=1198020057
The original plans were for an indoor plane made with 3mm Depron, with 33-inch wingspan and an all-up weight on the order of 145g. The Ross foamboard is 5mm and I don't have an indoor space, so I beefed everything up and went for a heavier outdoor build. The current version comes to 185g including a 2s 450mAh battery. Here's a photo:
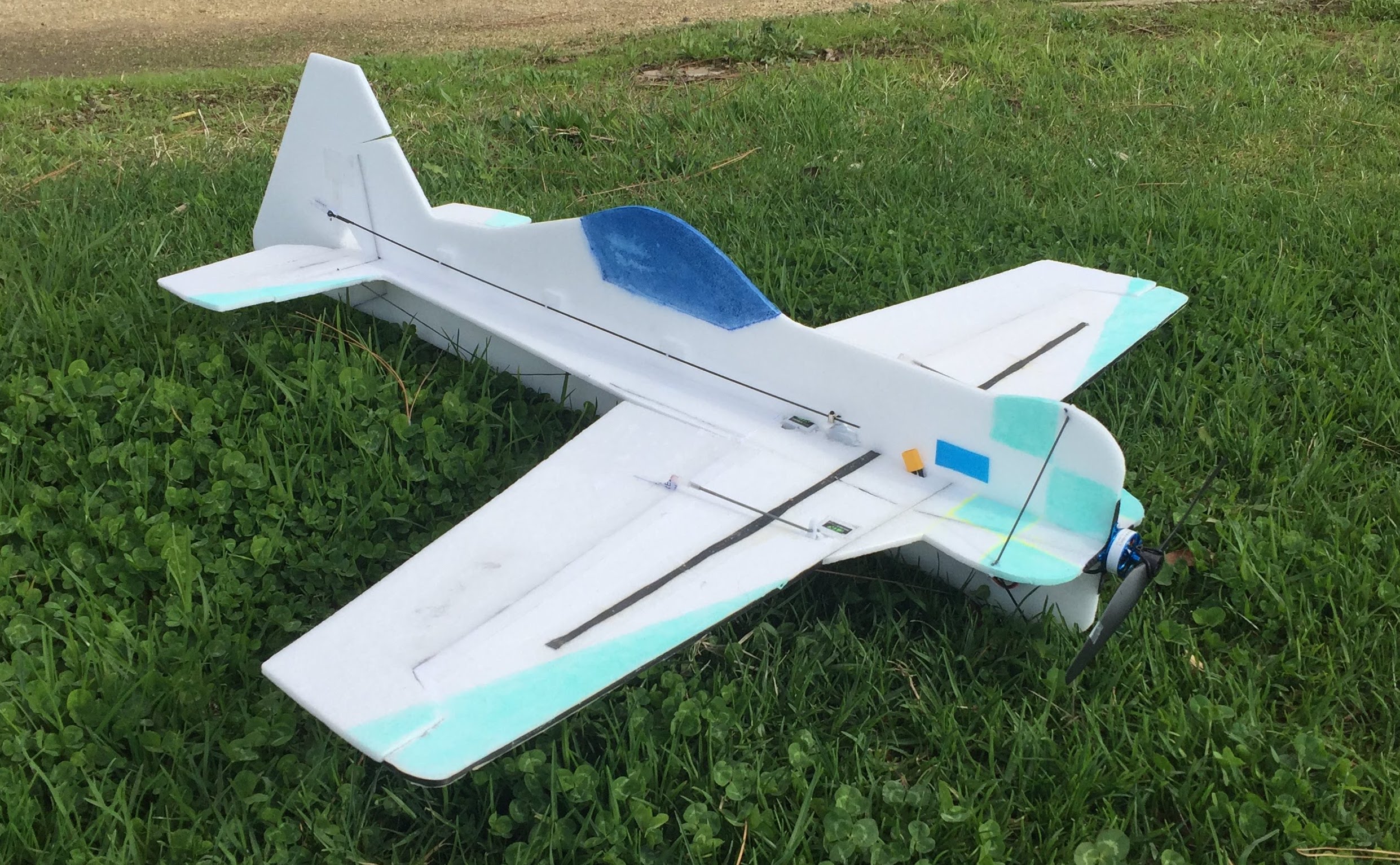
The airframe is something of a work in progress at the moment. Results with the Ross foamboard have been mixed. On the positive side, it's very light and dimensionally consistent with the paper removed, unlike the wavy, unevenly-thick foamboard that Adams has been turning out in recent years. But unfortunately the Ross foam is quite floppy. It ends up needing as much carbon reinforcement as EPP, but without the durability of EPP. I decided to forge ahead anyhow. I figure once this one crashes, I can take the electronics and carbon bits and cut a new airframe out of 5mm EPP.
More to come!