Fluburtur
Cardboard Boy
I know, I hate maths unless it is practical for what I want to do.
I was rebuilding the nose of my 3d printed VG-33 (again) and was thinking about how I could increase the speed, right now it has loads of air torque but top speed is low, so I was thinking I could trade torque for speed without changing the power system.
Then I thought about how the spinner was blocking some prop area, in this case my propeller is a 10" triblade and the spinner is 70mm in diameter, there is also the hub of the propeller that is 23mm in diameter and won't produce thrust anyways unless something is seriously wrong.
I always use this calculator for my RC stuff so I will assume it is somewhat accurate and it seems to be from my experience.
Anyways, I then calculated the area of the prop and stuff like that and the results are as follow:
Area of the prop excluding the hub: 502.6 cm² (the calculator thinks the whole diameter of the prop is producing thrust, if I include the hub it is 506.7 so close enough)
Area of the propeller minus spinner: 494.9 cm²
As you can see the difference isn't big, the area of the prop with spinner is equivalent to that of a 9.8" propeller however so far I have been ignoring RPM and pitch. My initial goal was to find a rule of thumb to get correct propeller size when using a spinner that covers part of it however the change in area isn't significant at that scale, the difference would be more important with a smaller propeller or larger spinner.
I initially planned to put a prop larger by 1" on that but then I think I would only lose efficiency and adding more pitch for the same diameter would also lower efficiency so I would need to put a smaller, more pitchy prop on the plane but that would kinda ruin the scale looks.
There is also the fact that a slightly larger propeller will produce more thrust in a non linear way because the speed of the propeller will get higher the furter away from the center if keeping the same RPM.
Im now realizing that this thread is turning into "help me build a better power system" but there is probably something I overlooked and that problem is worth thinking about I think.
I was rebuilding the nose of my 3d printed VG-33 (again) and was thinking about how I could increase the speed, right now it has loads of air torque but top speed is low, so I was thinking I could trade torque for speed without changing the power system.
Then I thought about how the spinner was blocking some prop area, in this case my propeller is a 10" triblade and the spinner is 70mm in diameter, there is also the hub of the propeller that is 23mm in diameter and won't produce thrust anyways unless something is seriously wrong.
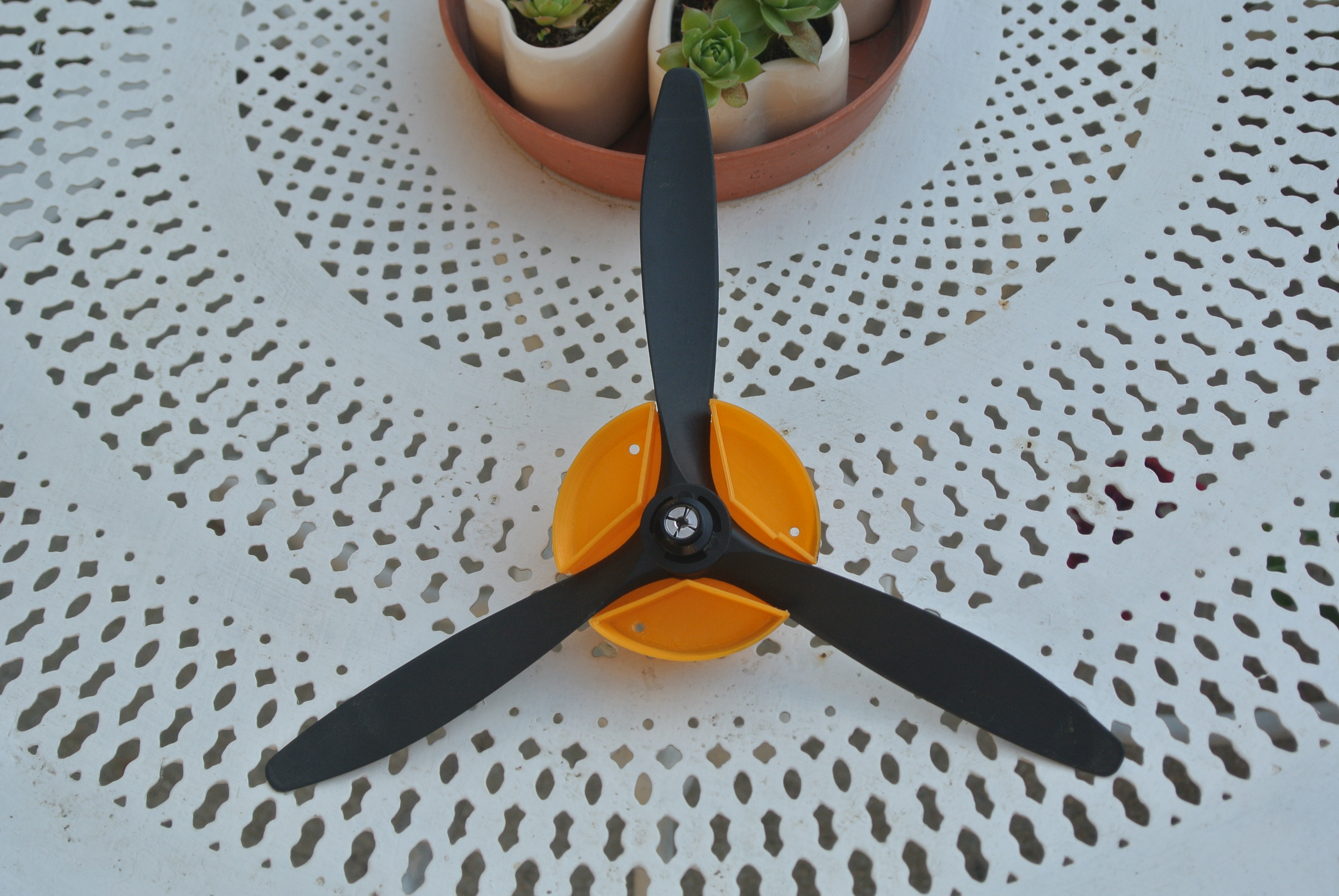
I always use this calculator for my RC stuff so I will assume it is somewhat accurate and it seems to be from my experience.
Anyways, I then calculated the area of the prop and stuff like that and the results are as follow:
Area of the prop excluding the hub: 502.6 cm² (the calculator thinks the whole diameter of the prop is producing thrust, if I include the hub it is 506.7 so close enough)
Area of the propeller minus spinner: 494.9 cm²
As you can see the difference isn't big, the area of the prop with spinner is equivalent to that of a 9.8" propeller however so far I have been ignoring RPM and pitch. My initial goal was to find a rule of thumb to get correct propeller size when using a spinner that covers part of it however the change in area isn't significant at that scale, the difference would be more important with a smaller propeller or larger spinner.
I initially planned to put a prop larger by 1" on that but then I think I would only lose efficiency and adding more pitch for the same diameter would also lower efficiency so I would need to put a smaller, more pitchy prop on the plane but that would kinda ruin the scale looks.
There is also the fact that a slightly larger propeller will produce more thrust in a non linear way because the speed of the propeller will get higher the furter away from the center if keeping the same RPM.
Im now realizing that this thread is turning into "help me build a better power system" but there is probably something I overlooked and that problem is worth thinking about I think.