Inq
Elite member
I'm trying to self-educate on electric powering of a motor. The spreadsheet below is using data accumulated from:
My question is: If I don't have any constraints to fitting the windings on the tube, what else is a consideration for picking the wire gauge?
Thank you for your help.
- Gauge diameters - https://www.engineeringtoolbox.com/awg-wire-gauge-d_731.html
- Calculate length of wires from 1lb spool - https://www.omnicalculator.com/physics/copper-wire-weight
- Resistance of wire/length - http://hyperphysics.phy-astr.gsu.edu/hbase/Tables/wirega.html
- Assumption that motor wire shouldn't carry more than 4 amps/sq-mm.
- current for a certain wire gauge
- how long 1 pound of wire is
- How much voltage is needed to create the rated current (1) over the length (2)
- The number of turns over an arbitrary 10mm diameter tube for the length (2)
- And finally, the Amp-Turns of the 1-4 configuration for each gauge.
My question is: If I don't have any constraints to fitting the windings on the tube, what else is a consideration for picking the wire gauge?
Thank you for your help.
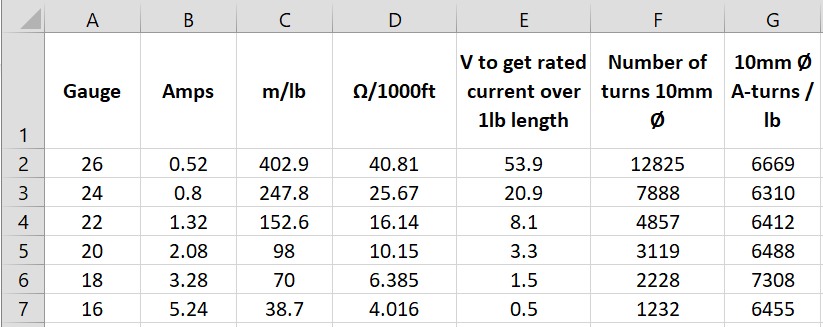
Last edited: