Build update
Got some good progress done this weekend and worked on the electric conversion engineering. Battery tray is mounted, motor mount is modified and the ESC mounting area is ready to accept the ESC. Here are some pics.
Making the battery tray. 3/32" ply, I used the Dremel to cut out the battery strap slots. I kind of mutilated it a bit, I was tired...
Installing the battery tray. I lined up the center of the battery with the motor thrust line, but it sat to high so I had to drop it down a little. I did leave enough room for a bigger battery also if I decide to go that way some day.
Battery tray mounting complete. I used balsa 3/8" angle epoxied in to strengthen the battery tray mounting area.
The business side of the tray.
Glued in some minicell foam for a battery pad and anti skid. I have some nice battery straps coming to hold it all down. You can see some slots cut in the foam for zip ties that will hold down the ESC mounted on the bottom side of the battery tray.
This 6s 4500 fits easily and I made sure to have extra room for a larger battery someday.
I decided to move the ESC as far back as possible for CG balance. After reviewing weights on gas/nitro motors and other types of builds people do, I think this is a good idea. If it is tail heavy I can always put in a larger battery. I also have a few inches to move the battery if needed. I am guessing at this point, but I think it will turn out pretty good.
The ESC has some minicell foam under it to help secure it when the zip ties are tightened. I may cut an access hatch in the bottom of the fuse for future access in case of service needs or a zip tie wears out.
I cut the motor mount shorter to fit the plans and the fiberglass cowl. I also decided to add a washer on the left side mounts for a slight bit of right thrust. After much review and even a reply from SIG, they say a little right thrust wont hurt, so now is a good time to add a little before I trim and mount the cowl.
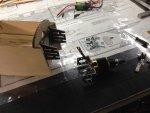