NickRehm
Member
Got absolutely ransacked by exams/assignments the past two weeks, but I finally found some time to finish up the CAD (added upper fixed pitch rotor, and other small updates). Parts are slowly but surely coming off the printer still--I'm trying out PETG and its taking some time to dial it all in.
The motors I ordered are finally in after 4 weeks too. I think the next giant leap in this project is committing to some of the shaft lengths in CAD and heading into the workshop to cut them all down to size. Then I'll need to spend a bit (a lot) of time dealing with bearing and shaft tolerances being not quite up to spec. Then I'll focus on blades....I've got some root inserts, 5mm carbon shafts, and I'll sand them down to shape before maybe covering them with something (tape? would be a lot easier than a layer of fiberglass)
The motors I ordered are finally in after 4 weeks too. I think the next giant leap in this project is committing to some of the shaft lengths in CAD and heading into the workshop to cut them all down to size. Then I'll need to spend a bit (a lot) of time dealing with bearing and shaft tolerances being not quite up to spec. Then I'll focus on blades....I've got some root inserts, 5mm carbon shafts, and I'll sand them down to shape before maybe covering them with something (tape? would be a lot easier than a layer of fiberglass)
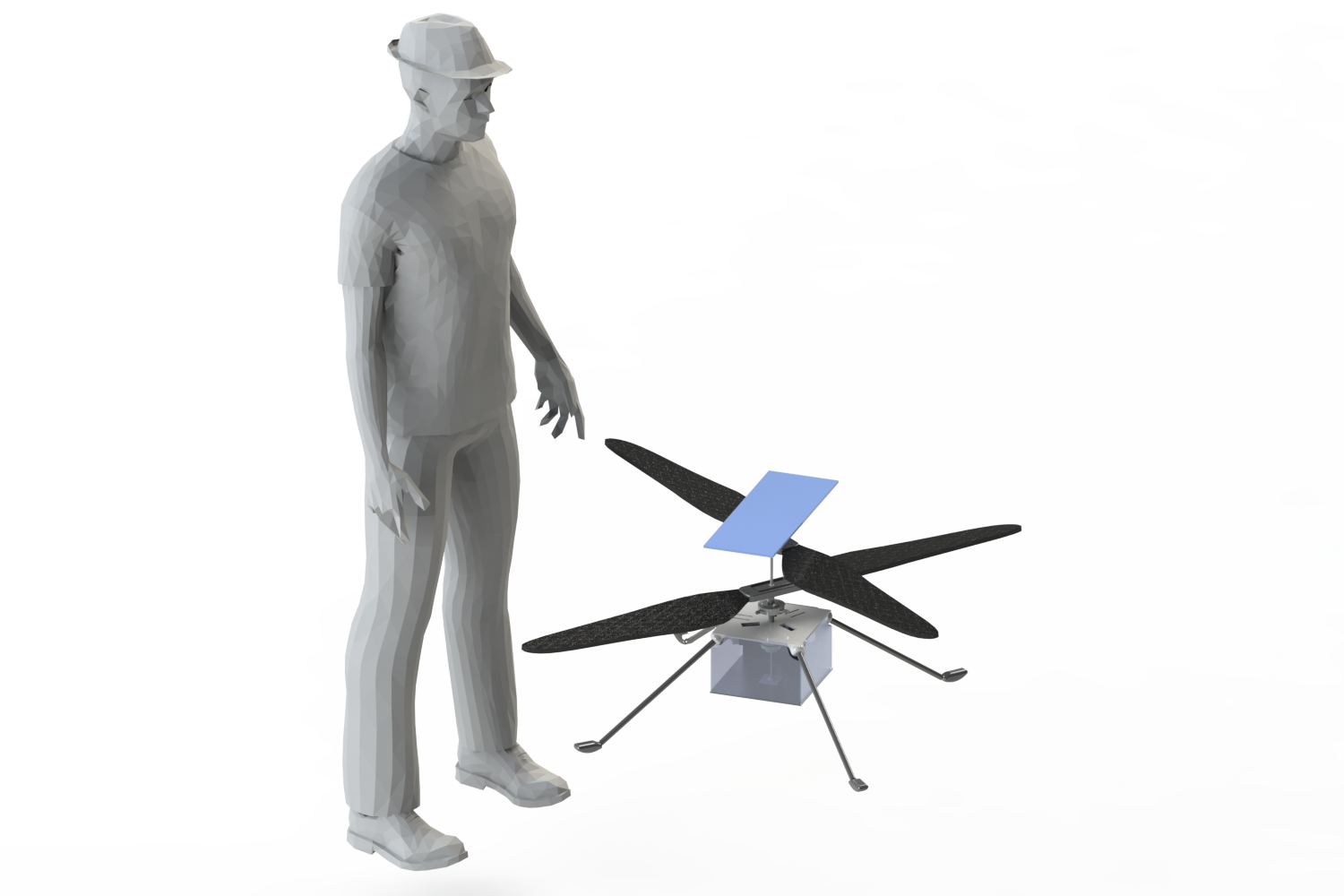