http://crimsonskies.wikia.com/wiki/Hughes_P21-J_Devastator
So, I was making landing gear for the Flapjack this weekend, then some wheels for a corsair, and needed to get better loft profiles. Started watching youtube videos on rails for lofts, and thought it would work good for wingtips.
Also been messing with updating the foamboard version of the Devastator, and couldn't resist trying it on something I already had a bunch of stuff drawn up for in 2D.
Here's a lofted wingtip with rail guides. Much cleaner that stuff I was getting before.
Kinda went overboard as I usually do. I'm too easily distracted. Testing lofts and rails kinda started turning into a whole plane.
It's decently sized as well. 50" Wingspan. 873.43 sq in of wing area, so I don't think 3D printing weight will be an issue on this plane.
I may redraw the top wing, I did a much better job with the bottom. Still have the Canard at the front to do, then a bunch of internal structure stuff which is getting easier. Also gonna need a canopy, and maybe an airscoop under the engine in the back similar to a P-51. We'll see how quickly stuff goes. I've solved a lot of problems that were giving me tons of grief on the Hall Bulldog I was working on last year and things are progressing smoothly so far.
*********************************************************************
Current Model status:
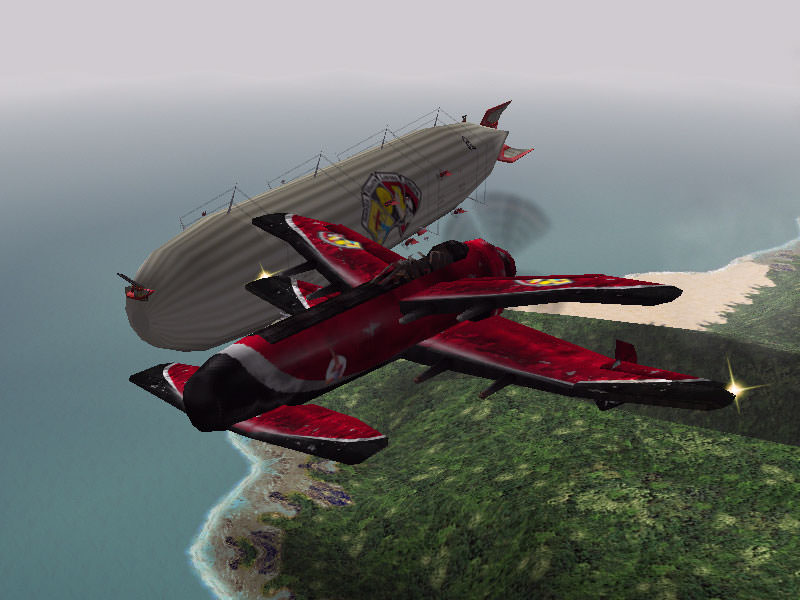
So, I was making landing gear for the Flapjack this weekend, then some wheels for a corsair, and needed to get better loft profiles. Started watching youtube videos on rails for lofts, and thought it would work good for wingtips.
Also been messing with updating the foamboard version of the Devastator, and couldn't resist trying it on something I already had a bunch of stuff drawn up for in 2D.
Here's a lofted wingtip with rail guides. Much cleaner that stuff I was getting before.
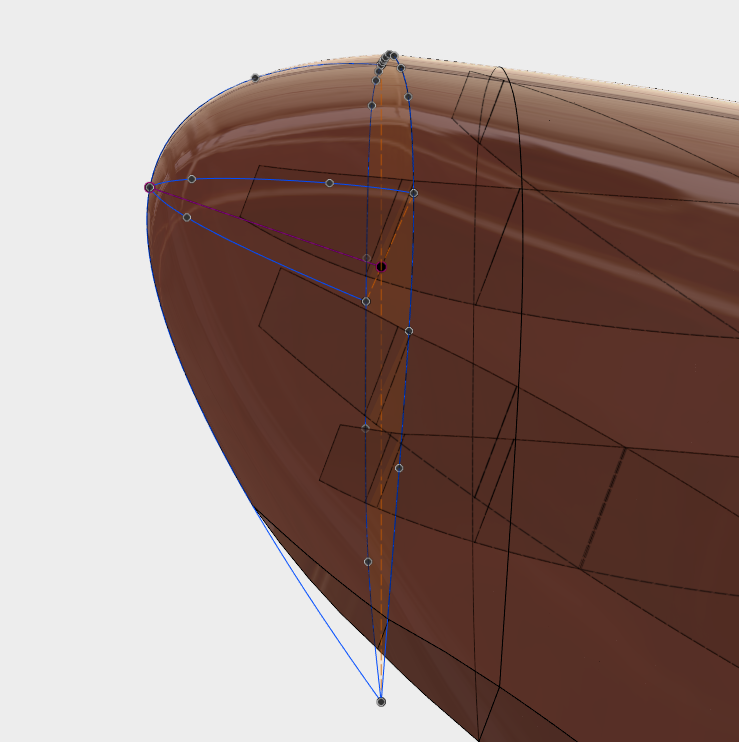
Kinda went overboard as I usually do. I'm too easily distracted. Testing lofts and rails kinda started turning into a whole plane.
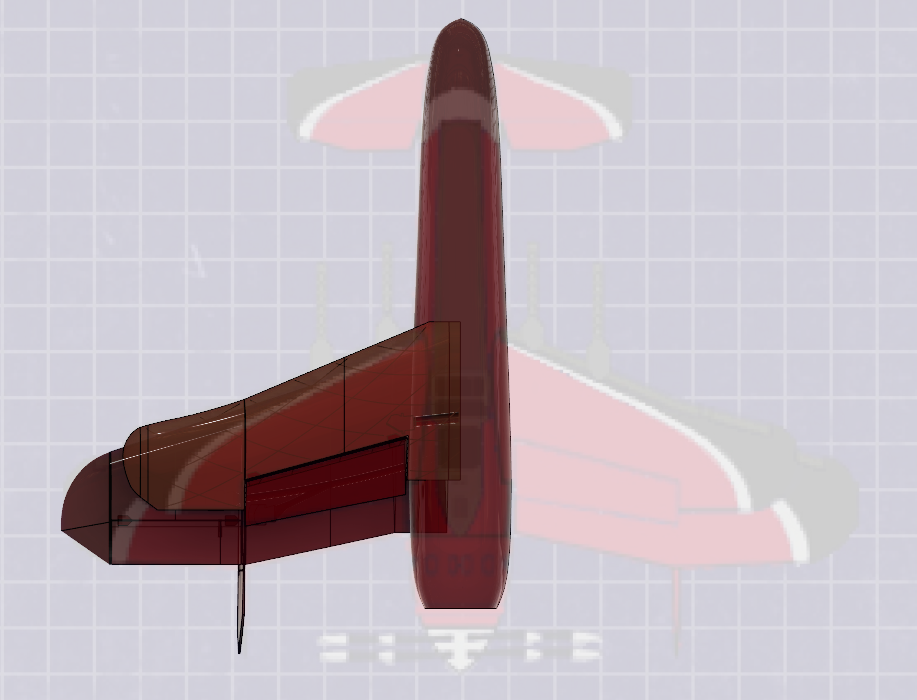
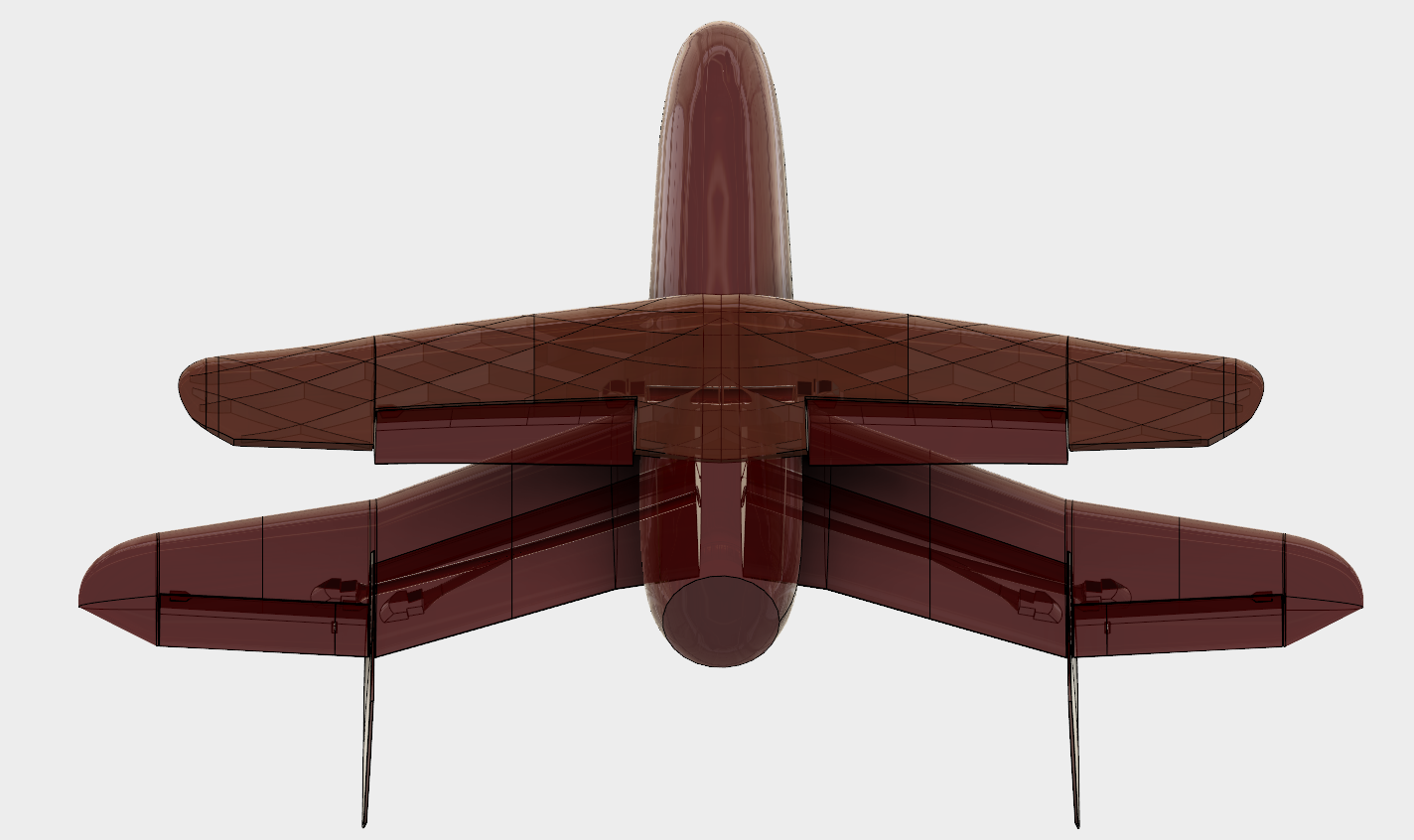
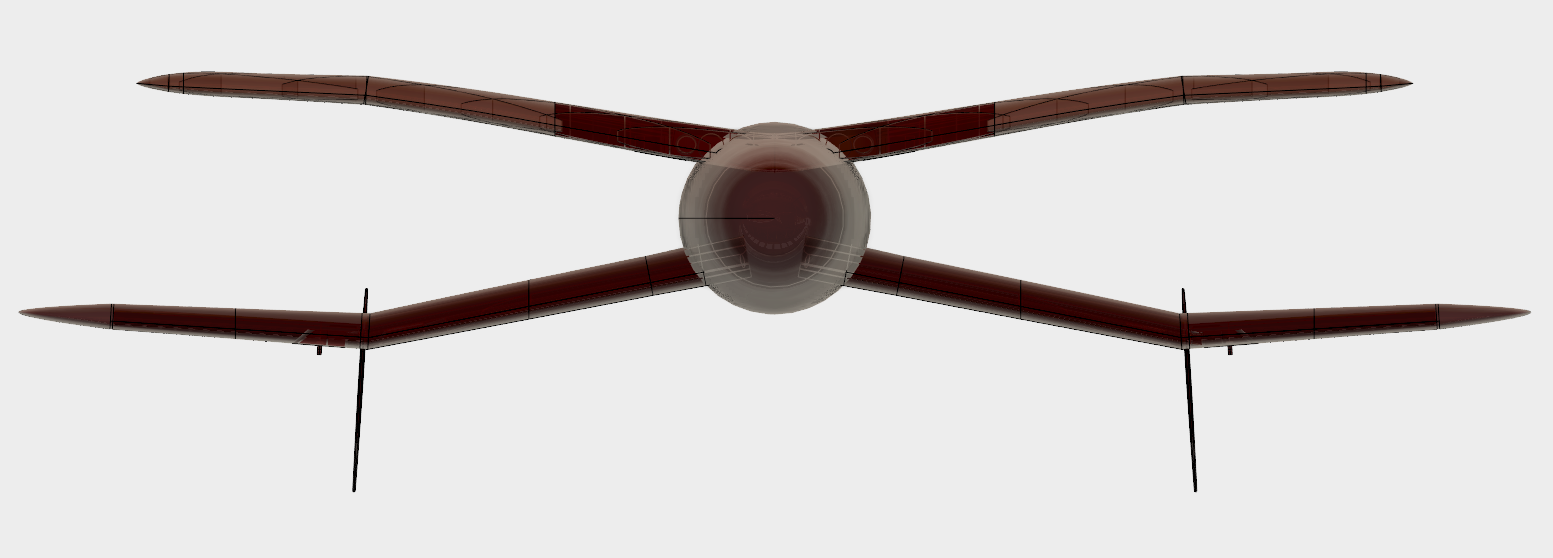
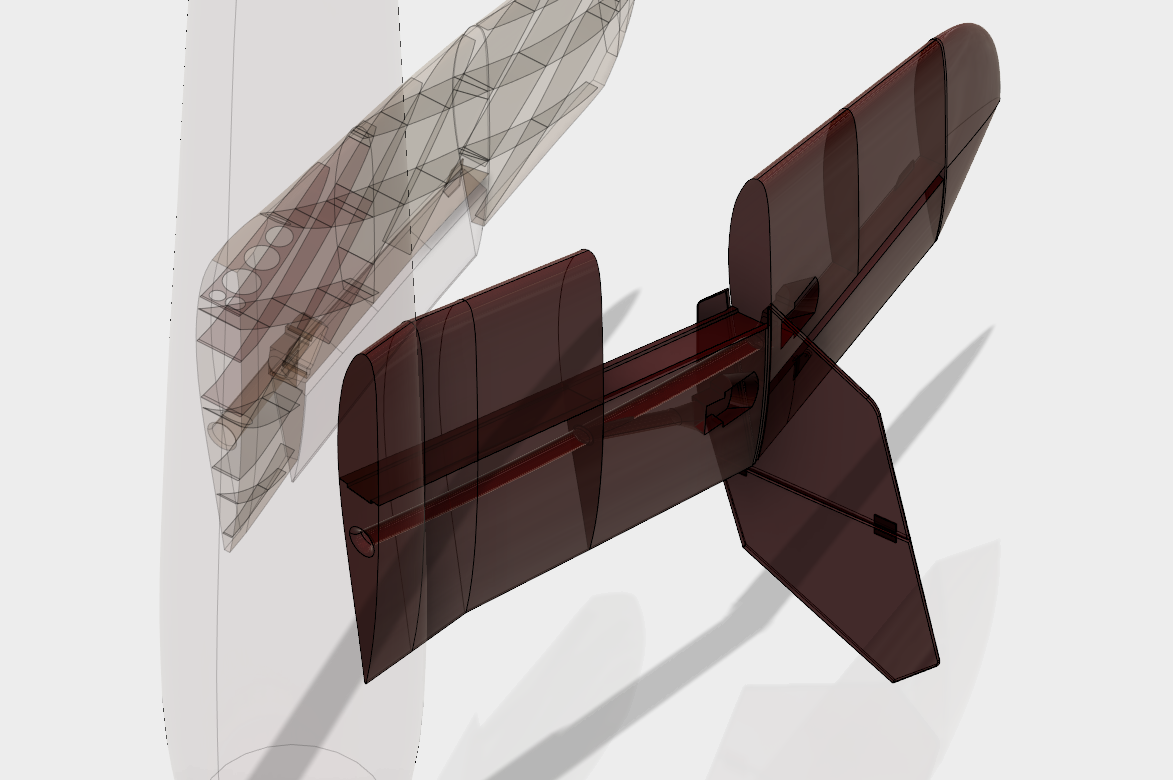
It's decently sized as well. 50" Wingspan. 873.43 sq in of wing area, so I don't think 3D printing weight will be an issue on this plane.
I may redraw the top wing, I did a much better job with the bottom. Still have the Canard at the front to do, then a bunch of internal structure stuff which is getting easier. Also gonna need a canopy, and maybe an airscoop under the engine in the back similar to a P-51. We'll see how quickly stuff goes. I've solved a lot of problems that were giving me tons of grief on the Hall Bulldog I was working on last year and things are progressing smoothly so far.
*********************************************************************
Current Model status:
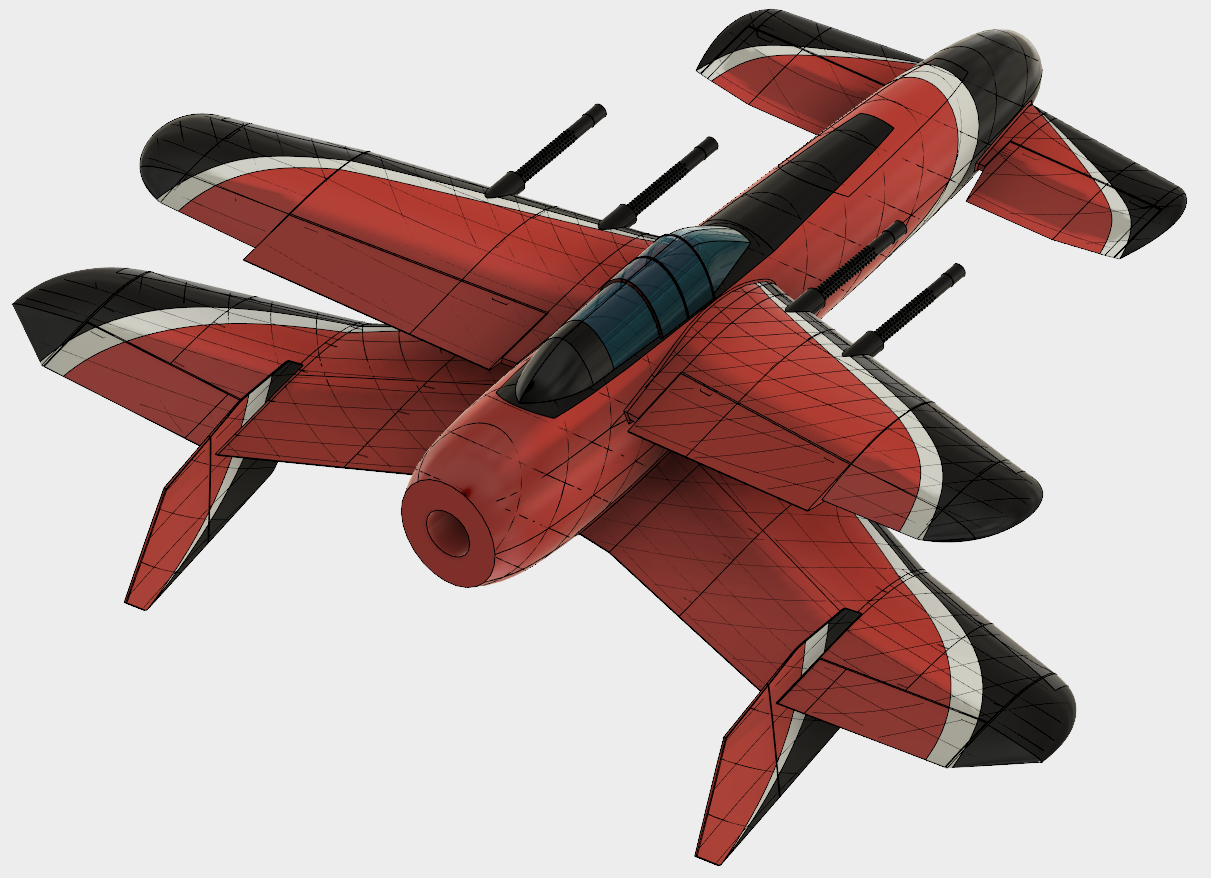
Last edited: