dkj4linux
Elite member
An quick update on my living situation...
I'm now getting settled in to my new home/hideout. Got new internet... quite the upgrade (for less $$, even) from 10Mbps to 250Mbps (fiber)! I've not got any machines set up yet... still trying to find stuff and get it out where I can find it again. Built a quick, crude "entertainment center" to house a couple of prized possessions (TV and Prusa printer) within eyeshot... and several other machines are rather unceremoniously pushed/piled into one corner yet.
Also enjoying having my grand-daughter, and her friend, just drop in unexpectedly, on a whim... they like to pile into my cheapie massage chair and crank it up to watch TV. And I'm getting educated to a few new shows...
Getting there... slowly.
-- David
I'm now getting settled in to my new home/hideout. Got new internet... quite the upgrade (for less $$, even) from 10Mbps to 250Mbps (fiber)! I've not got any machines set up yet... still trying to find stuff and get it out where I can find it again. Built a quick, crude "entertainment center" to house a couple of prized possessions (TV and Prusa printer) within eyeshot... and several other machines are rather unceremoniously pushed/piled into one corner yet.
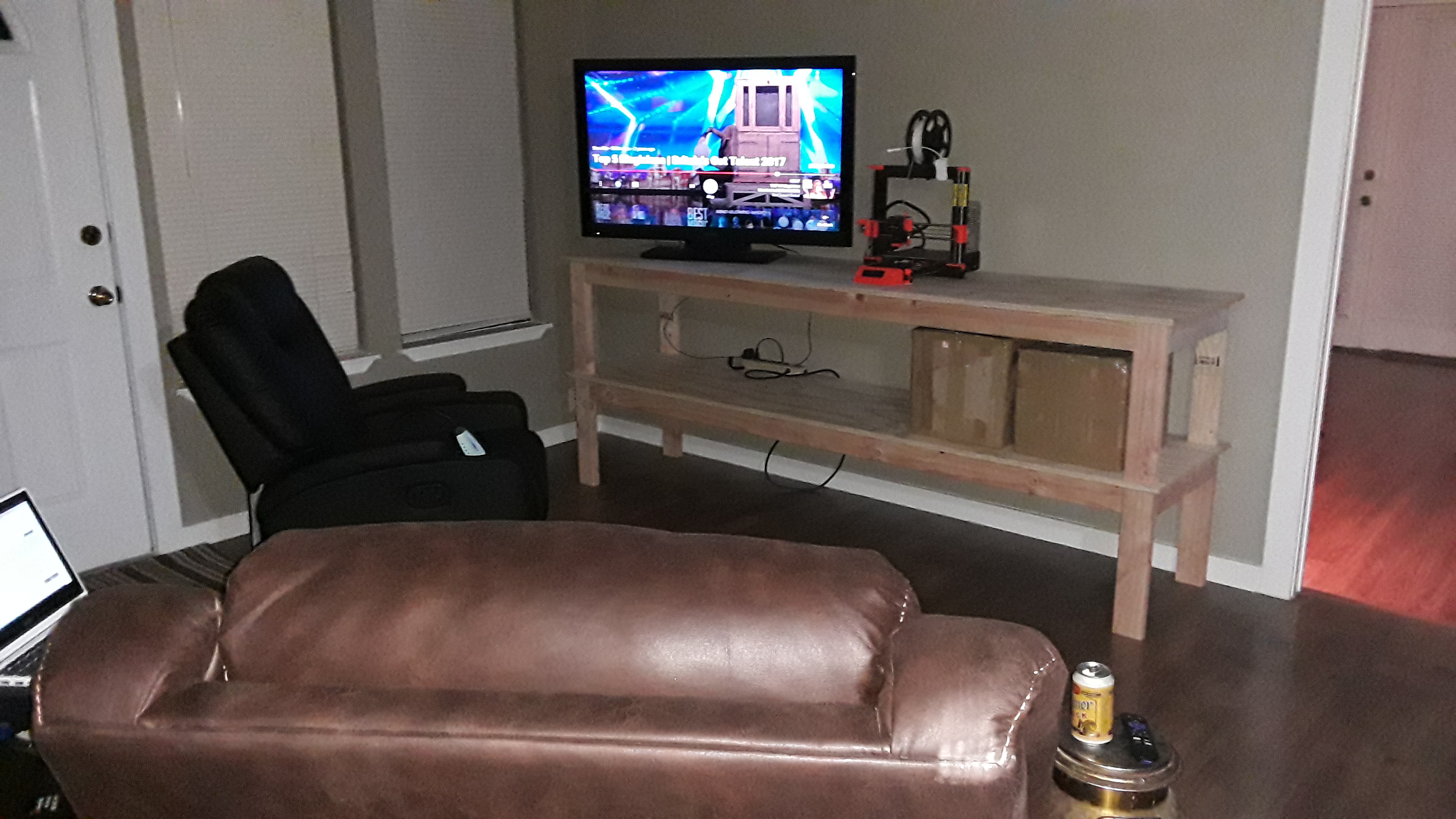
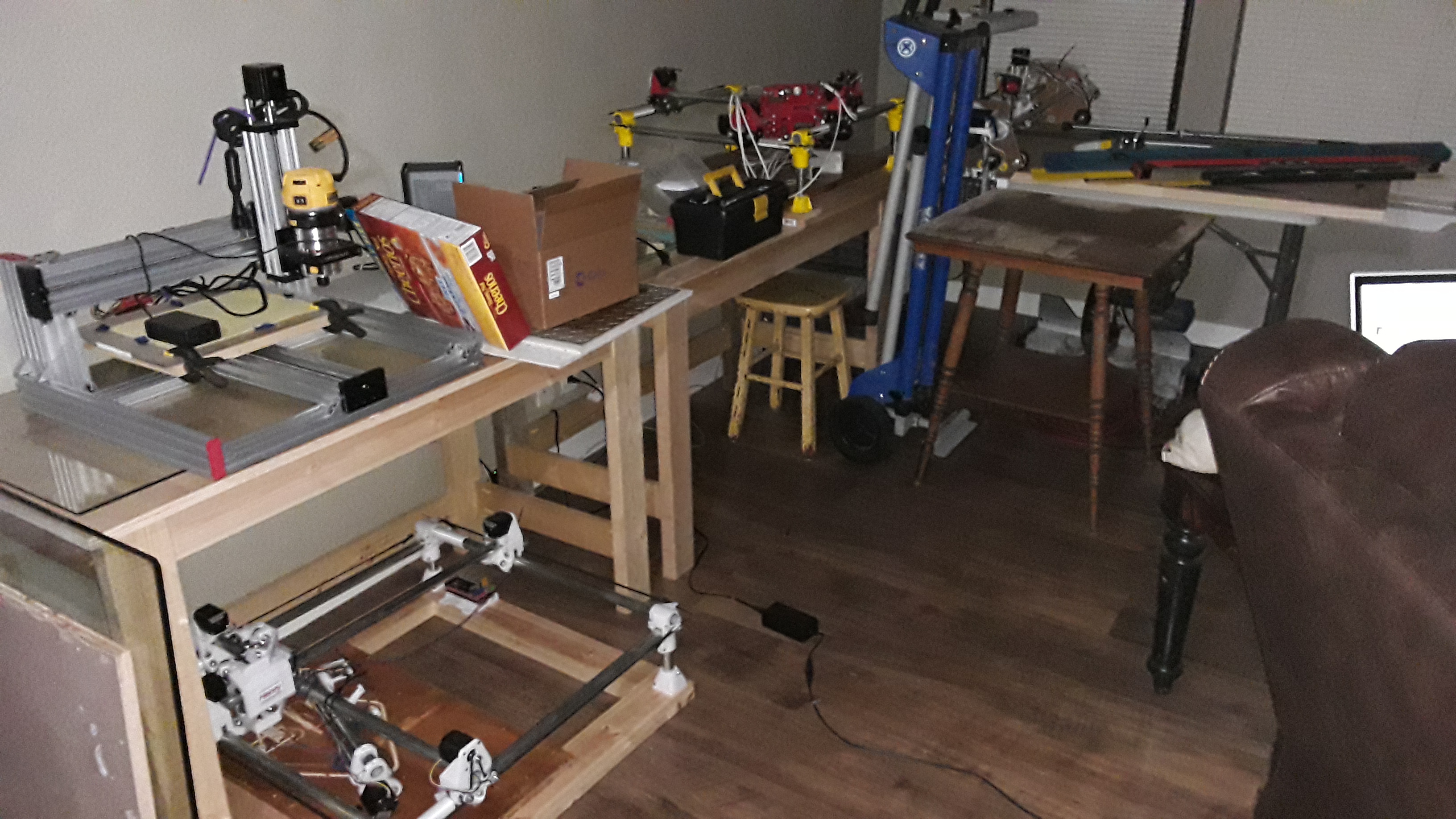
Also enjoying having my grand-daughter, and her friend, just drop in unexpectedly, on a whim... they like to pile into my cheapie massage chair and crank it up to watch TV. And I'm getting educated to a few new shows...
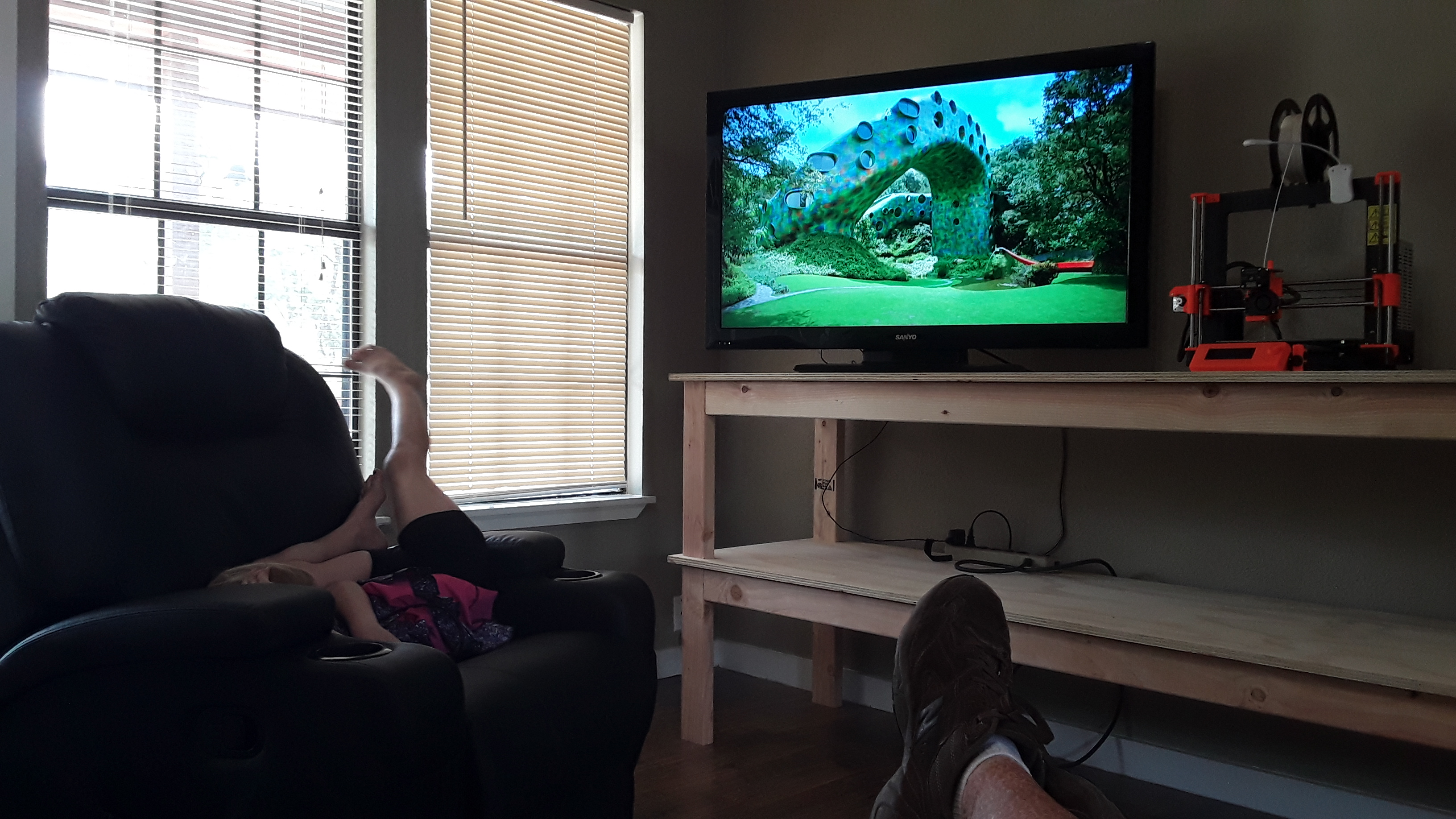
Getting there... slowly.
-- David
Last edited: