Jackson T
Elite member
I've wanted to make something out of fibreglass for ages, mainly because that would allow me to make new shapes and curves that I couldn't with balsa. After hearing about plaster molds, I found some cornice cement (a building material similar to plaster) at home, and set to work making a sample plug. I covered the plug with tape, but that left imperfections in the mold where the tape wrinkled. I will try painting it next time. I placed it on a taped wooden board and 'spooned' on a thick mixture of the cornice cement with a paddle pop stick. It popped off the board nicely after it dried and the plug came out almost as easily. I didn't want to buy proper mold release, so I did some research and tried some $3 boot polish. I wiped it on with a rag, let it dry for a while, then repeated 2 more times before laying up the fibreglass. It took a little encouragement, but wasn't a hassle to get out. Pics below. The black stuff on the mold in the last photo is paint. I don't think it made any difference though, so I won't be painting the next one.
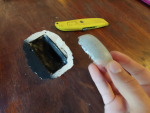
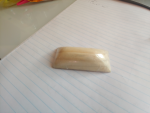
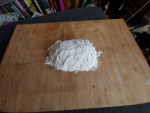
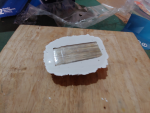
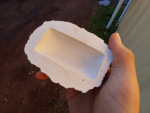
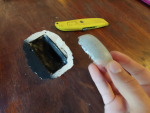
Last edited: