speedbirdted
Legendary member
Went over with the plug with 3 coats of finishing resin, sanded in between. Last coat was wet sanded, just to see how ridiculously smooth I could get it for giggles. Here it is, but I forgot to clean the residue off, so it still looks kinda dull, and not good for the camera 
I wanted to kind of paint it in plaster to make the female mold but I quickly determined it didn't dry fast enough and would all just drip off. So, I made this little container to put the plaster in and then put the plug in the plaster.
Unfortunately I did not have enough plaster to put the whole plug all the way in. It came up about 1/2 an inch short, which theoretically should not be a problem as I cut the plug a little long anyway. However if it is a problem I can reuse the plug as a negative mold instead - that way I would put the glass cloth directly on the plug using release wax to prevent it from just sticking to the plug permanently. Now to wait for the plaster to dry out...
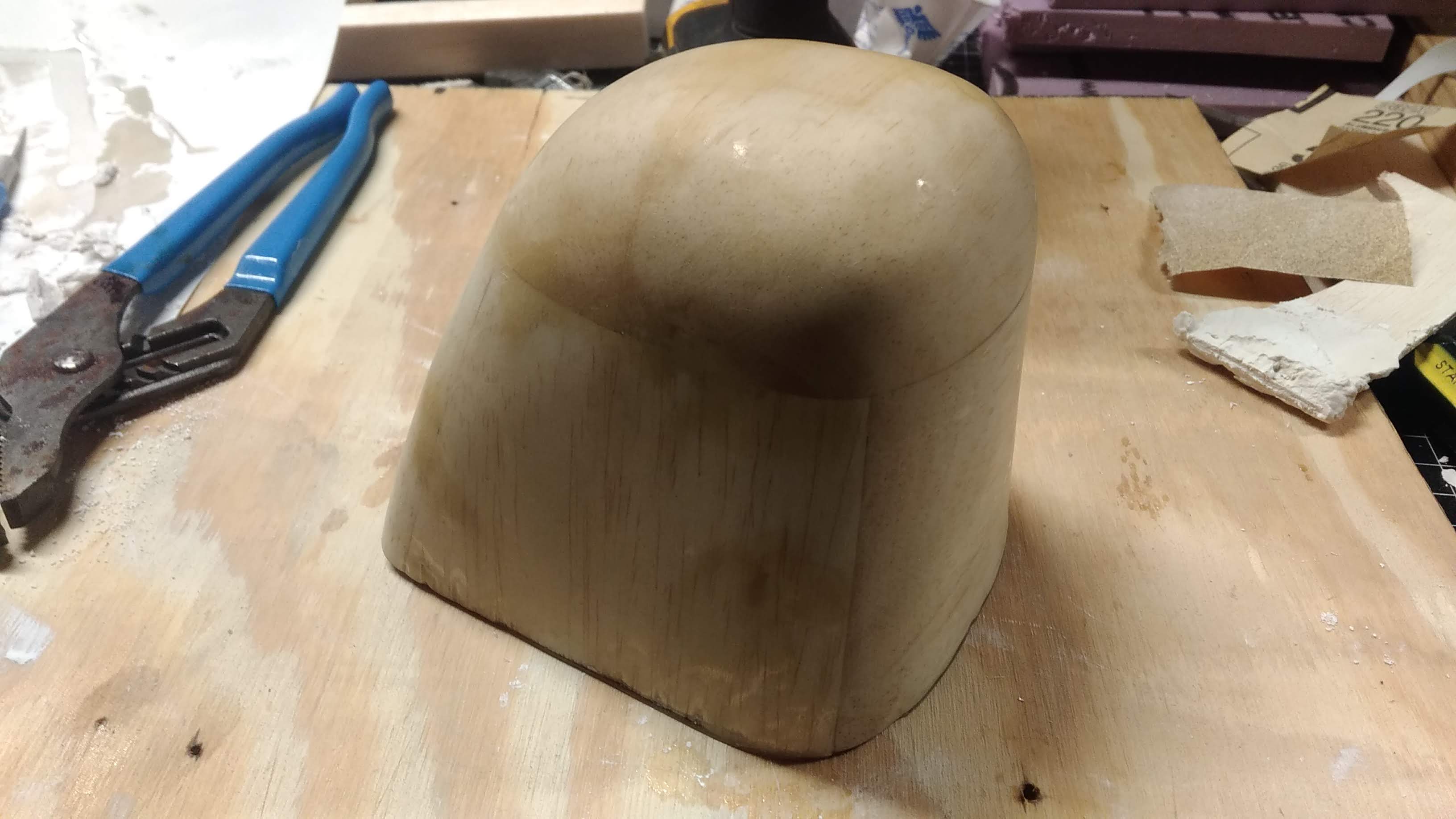
I wanted to kind of paint it in plaster to make the female mold but I quickly determined it didn't dry fast enough and would all just drip off. So, I made this little container to put the plaster in and then put the plug in the plaster.
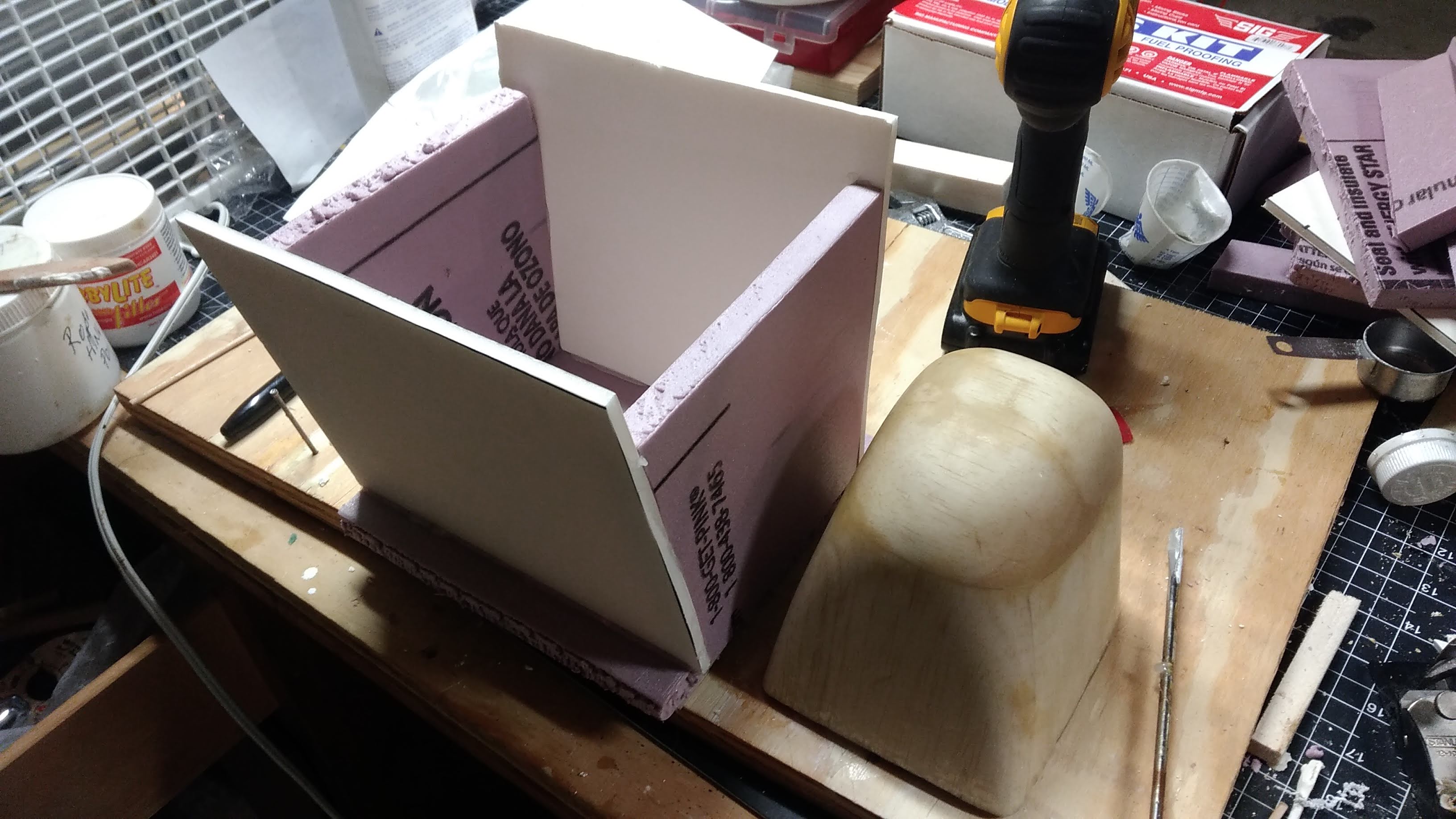
Unfortunately I did not have enough plaster to put the whole plug all the way in. It came up about 1/2 an inch short, which theoretically should not be a problem as I cut the plug a little long anyway. However if it is a problem I can reuse the plug as a negative mold instead - that way I would put the glass cloth directly on the plug using release wax to prevent it from just sticking to the plug permanently. Now to wait for the plaster to dry out...
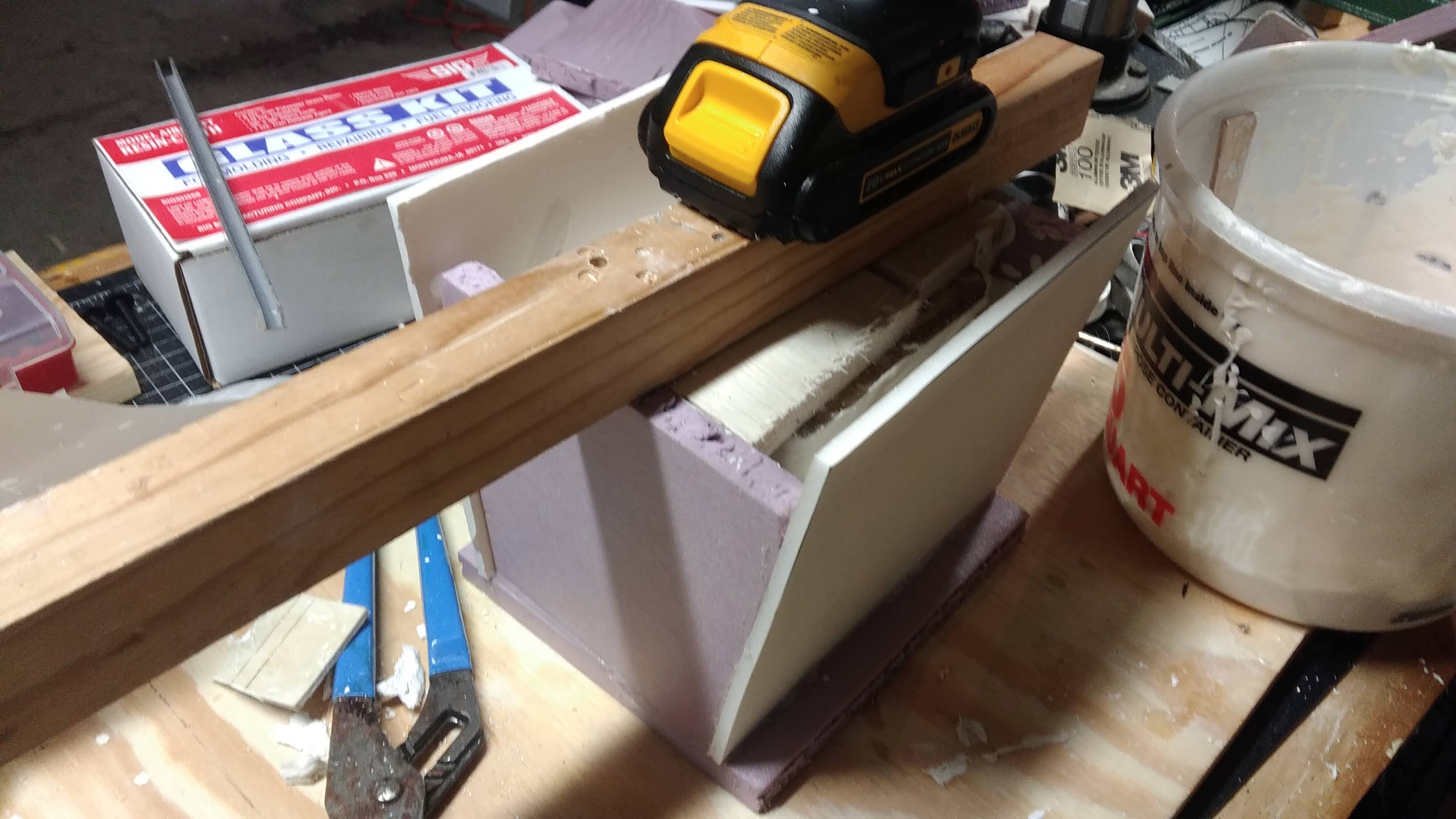