So, it's been a hell of a long time since I've done anything RC/fliteTest related, and it's entirely because of the bane of existance well known to everyone between the ages of 16 and 25: Exams. The past couple of months have been absolute hell, but I'm pleased to say I've finally finished all of my exams, and am ready to reach for the skies. The other bit of good news that has arisen, is that I'm now officially taking a gap year. Some of the reasons for this decision are a little complicated, but the main one is because I want to pursue all of the crazy projects that I never really had time for while I was at school. Of course, included in these "projects" are all of my RC related endeavors. It was a little unfortunate that the moment I was actually getting somewhere with this wonderful hobby, my A level exams and coursework hit me like a freight train. The gap year, and other university related developments that have come into effect mean there is a high probability I will attend a flite fest in the next few years. If not next year, hopefully in three years time, as the university where I have chosen to study offers a one year study abroad scheme, with places available in three different american universities. This would be idea for me in terms of establishing connections, as living and working in America has long been a well cemented plan of mine and why not attend a flite fest along the way?
But what good would this post be in the Mad Builder's Corner, if I was only going to spend the entire time rambling on about my extremely boring life developments, that franctly matter not to the flite test community.
No, instead I also want to present a 1:10 Bf 109 Build. I've been working on this for a while, and before my entire life was overrun with education, I managed to complete the foam cut fuselage, as well as ordering some the electronics.
On the list for the next week is hopefully getting the wing spars laser cut from 3mm plywood, and cutting the rest of the foam wing ribs, to hopefully have a finished framework before I leave to travel for three weeks.
When I return I intend to cover this framework with a skin of 2mm depron, and additionally I should hopefully have access to my own 3D printer, allowing me to create 3d printed wing tips, tail section and cockpit.
The final stages of the build should comprise of applying a lightweight filler to the fuselage, to fill in all the ugly lips and gaps in the hot wire cut foam. Sanding it down to make it all nice, neat and symmetrical. Adding a single layer of ultra lightweight fiberglass for some added rigidity and to create a very smooth surface. And finally, weight allowing, painting the thing to make it look like the real deal.
I do hope that everyone has some good plans for summer, as well as the coming year.
But what good would this post be in the Mad Builder's Corner, if I was only going to spend the entire time rambling on about my extremely boring life developments, that franctly matter not to the flite test community.
No, instead I also want to present a 1:10 Bf 109 Build. I've been working on this for a while, and before my entire life was overrun with education, I managed to complete the foam cut fuselage, as well as ordering some the electronics.
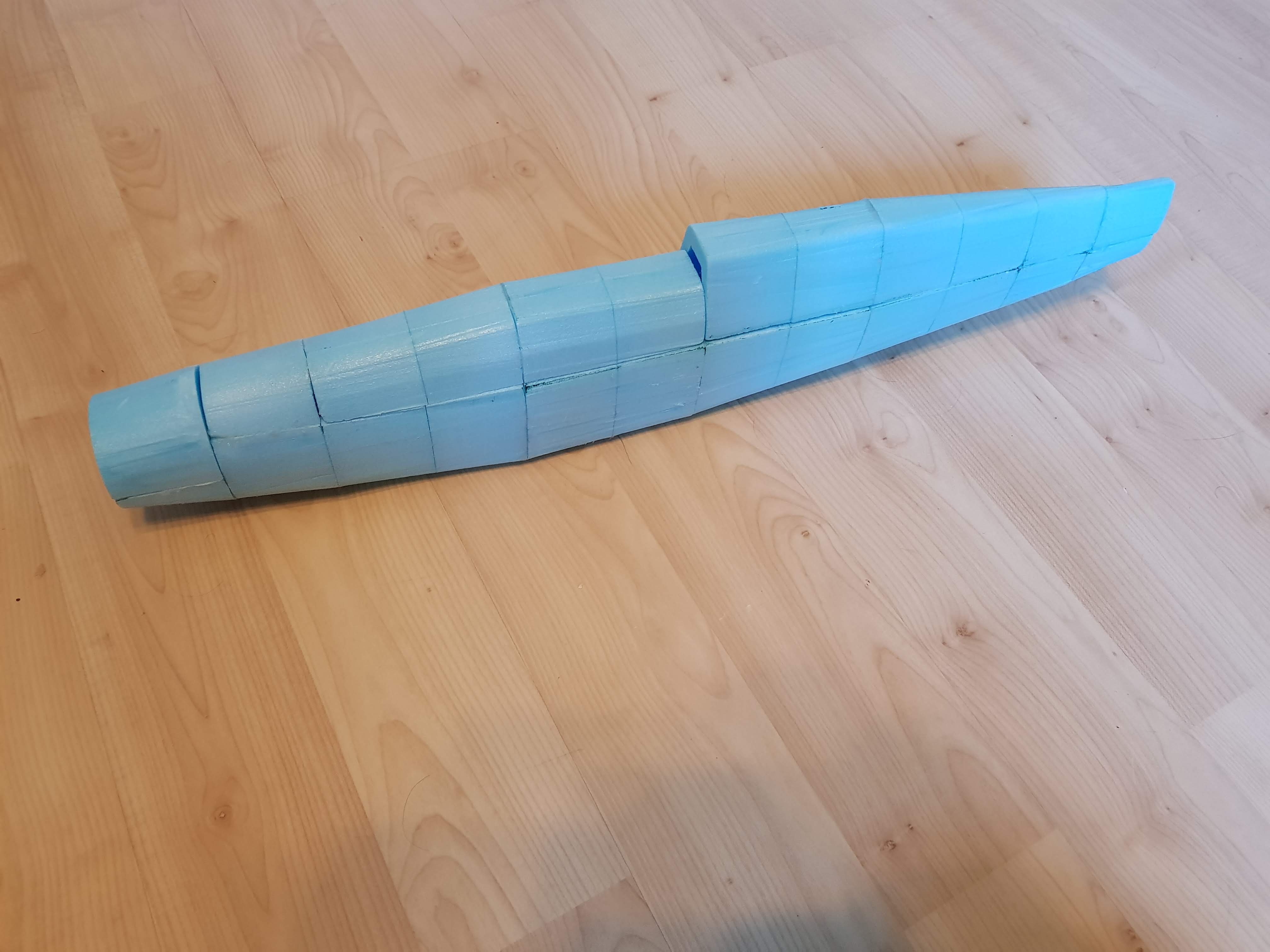
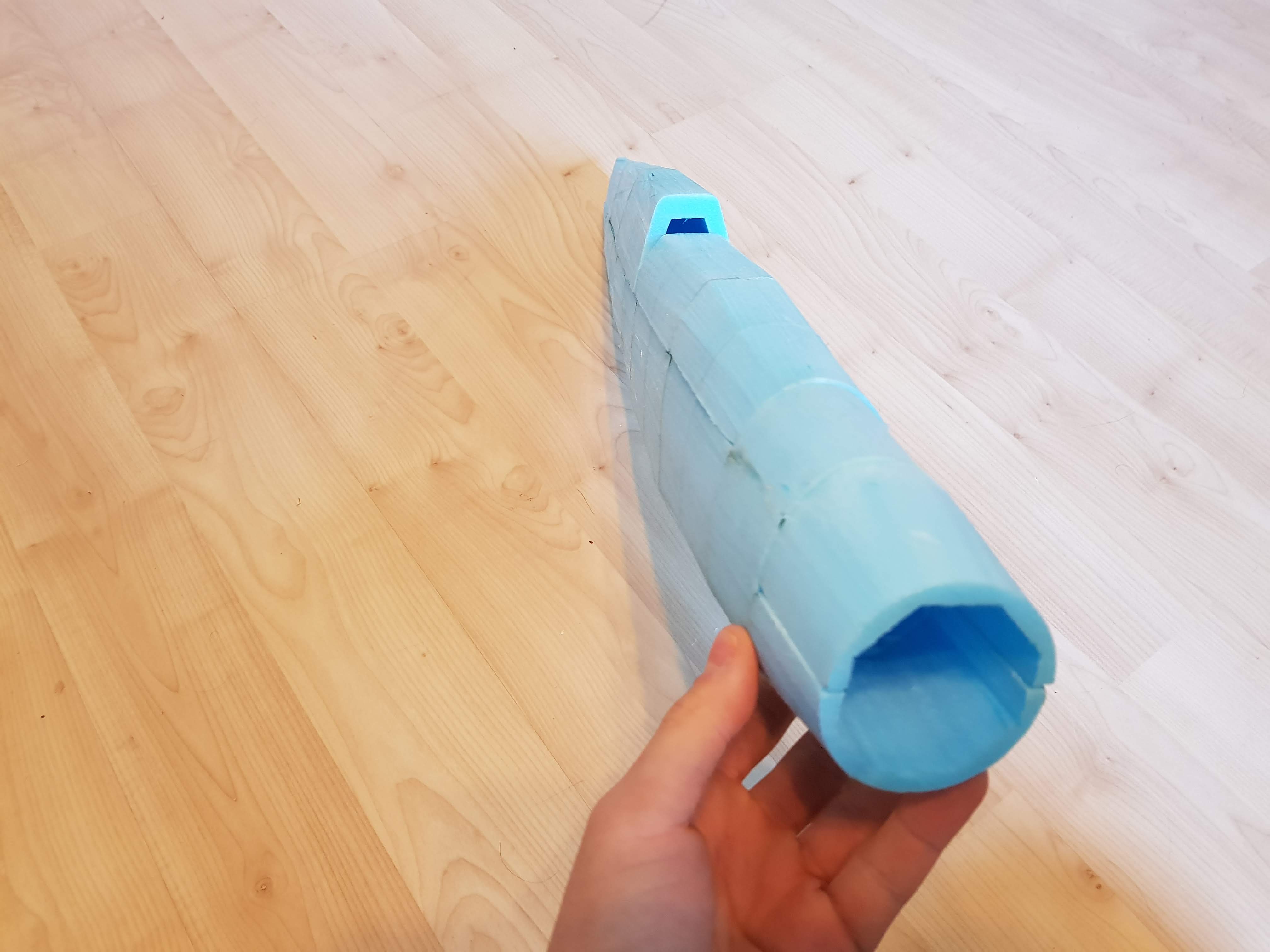
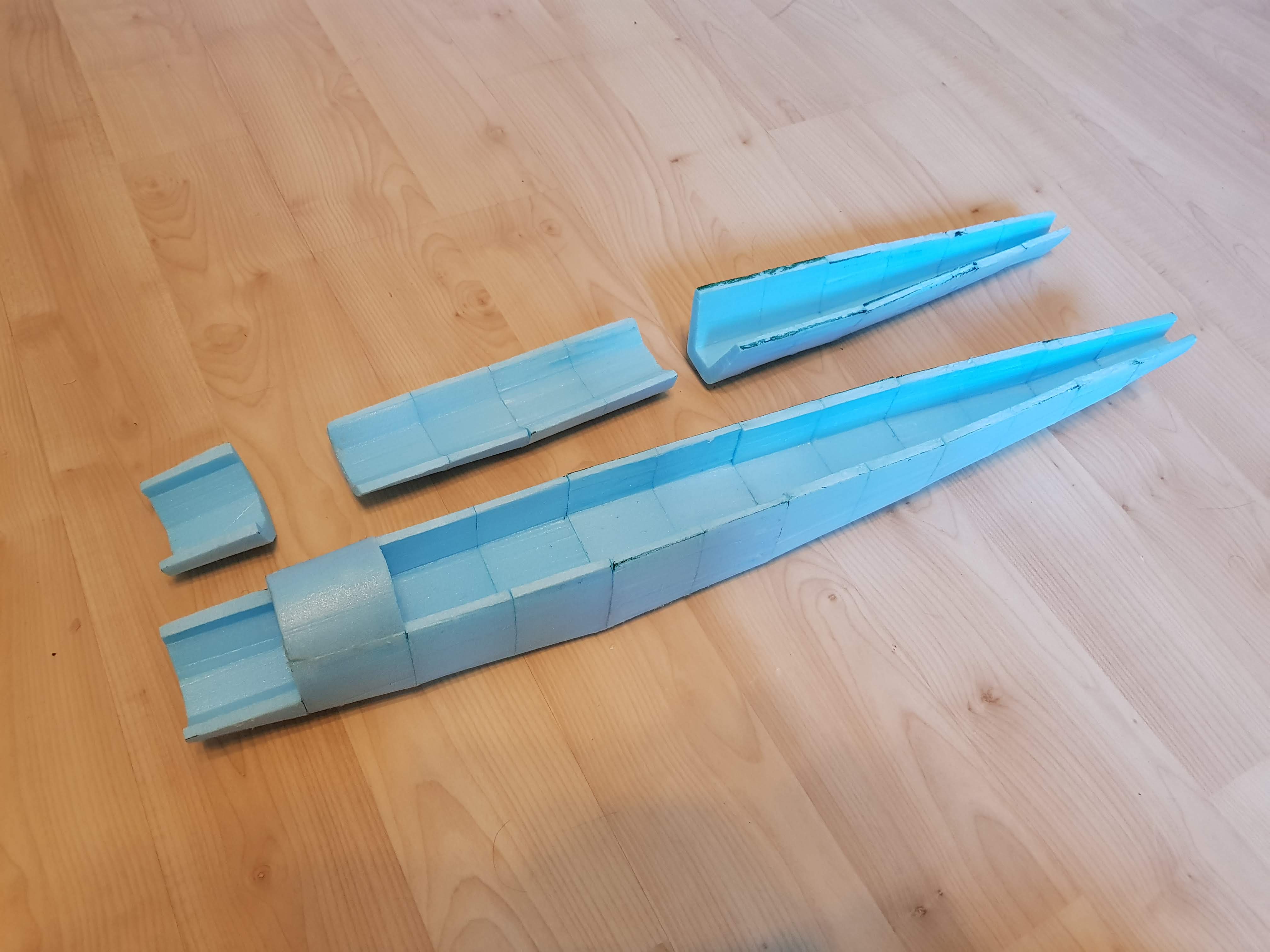
On the list for the next week is hopefully getting the wing spars laser cut from 3mm plywood, and cutting the rest of the foam wing ribs, to hopefully have a finished framework before I leave to travel for three weeks.
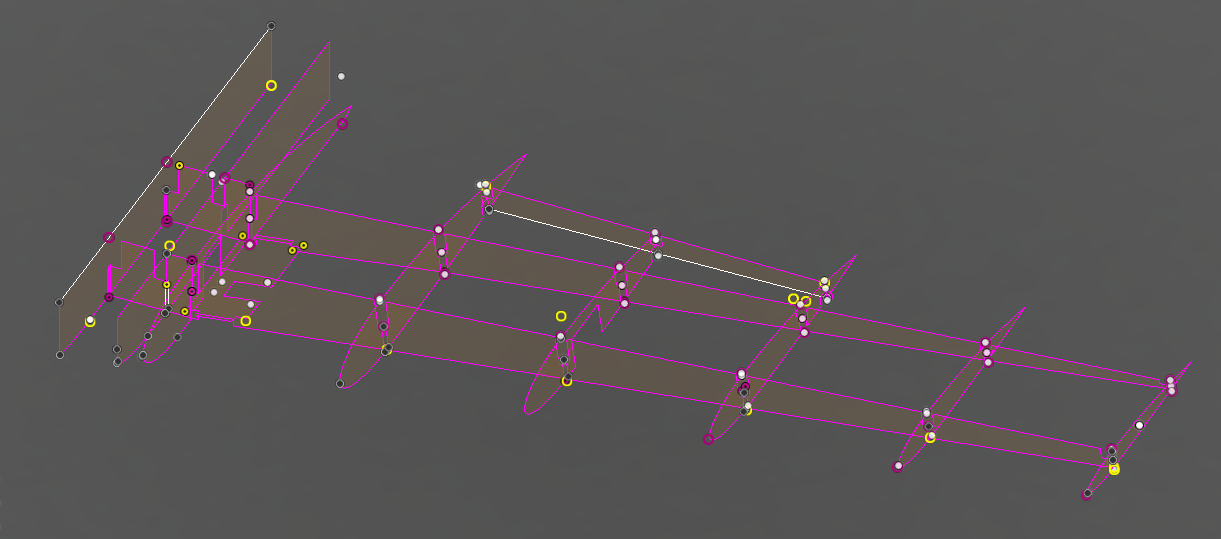
When I return I intend to cover this framework with a skin of 2mm depron, and additionally I should hopefully have access to my own 3D printer, allowing me to create 3d printed wing tips, tail section and cockpit.
The final stages of the build should comprise of applying a lightweight filler to the fuselage, to fill in all the ugly lips and gaps in the hot wire cut foam. Sanding it down to make it all nice, neat and symmetrical. Adding a single layer of ultra lightweight fiberglass for some added rigidity and to create a very smooth surface. And finally, weight allowing, painting the thing to make it look like the real deal.
I do hope that everyone has some good plans for summer, as well as the coming year.