https://www.google.com/url?sa=t&rct=j&q=&esrc=s&source=web&cd=&cad=rja&uact=8&ved=2ahUKEwjmjcynvPntAhXazjgGHVdqCdkQFjAFegQIBxAC&url=https://www.semanticscholar.org/paper/Quadcopter-thrust-optimization-with-Kuantama-Tarca/7e8efcd65702837b7883182b94489c6d16412437&usg=AOvVaw2nJKvlNXK5CGcT8NHD8Wid
These people show a thrust increase with a tapered duct outlet.
I don't agree that propeller shrouds are any good on quadcopters-you want to fly at an angle, and not interfere with propeller performance when airflow arrives at an angle , as with a helicopter.
the claim is +19 % on thrust and +17% on blade ejection velocity over unshrouded.
This sounds a little contrived, as generally blade performance is good with good tip shape, and relatively low velocity (20 m/s)
I have found that power varies directly with diameter for the same thrust.
1/2 diameter = 2x the power., Also, increasing diameter by 33 % drops power required for the same thrust on the same motor,
assuming torque remains the same over the rpm range, rpm drops by about 60 %
Ie: 54 amps becomes about 36 amps.
Find change in diameter to keep the same thrust?- use area effectiveness, as thrust depends directly on area.
area reduces by 19 %, so diameter reduces by about 10 %. Does this sound right?
example calc: 0.9 sq = 0.81, 1-.81 = 0.19
9 inch diameter becomes 8.18 inches. I need to cross-check these results elsewhere, as their measurement methodology may be suspect.
ve I I find it difficult to believe that constricting flow after the propeller improves efficiency. In free air, the flow naturally restricts to half the area and twice the velocity, anyway. Also, their tip clearance seems too great at 10mm over 400 mm prop diameter.
Also, they don't account for a curved inlet.
Other sources show that 10 % diameter reduction on inlet to the propeller diameter is desirable. for general flight.
Maybe a little outlet restriction matches into the free air conditions better.
The amount of restriction required reduces with increasing speed (V0, aircraft speed) , where V1 is the output velocity at the propeller.
Also, reducing the propeller diameter on a motor automatically increases rpm, until torque needed balances the engine torque again.
if A drops by 19%, V increases from 21 to 23 m/s for the same thrust,
power = TV = 1.1 times original, same torque, = 1.1 x rpm.
now 1.1x velocity also = 1.1 x rpm. If rpm was 8000, it will now be 8800, so we are now producing the same thrust plus an extra efficiency factor, which balances the power inefficiency factor.
Now this motor produces more thrust with less power by, one assumes, an 8 inch propeller? (the original motor table) - the table doesn't make sense- we need the original.
These people show a thrust increase with a tapered duct outlet.
I don't agree that propeller shrouds are any good on quadcopters-you want to fly at an angle, and not interfere with propeller performance when airflow arrives at an angle , as with a helicopter.
the claim is +19 % on thrust and +17% on blade ejection velocity over unshrouded.
This sounds a little contrived, as generally blade performance is good with good tip shape, and relatively low velocity (20 m/s)
I have found that power varies directly with diameter for the same thrust.
1/2 diameter = 2x the power., Also, increasing diameter by 33 % drops power required for the same thrust on the same motor,
assuming torque remains the same over the rpm range, rpm drops by about 60 %
Ie: 54 amps becomes about 36 amps.
Find change in diameter to keep the same thrust?- use area effectiveness, as thrust depends directly on area.
area reduces by 19 %, so diameter reduces by about 10 %. Does this sound right?
example calc: 0.9 sq = 0.81, 1-.81 = 0.19
9 inch diameter becomes 8.18 inches. I need to cross-check these results elsewhere, as their measurement methodology may be suspect.
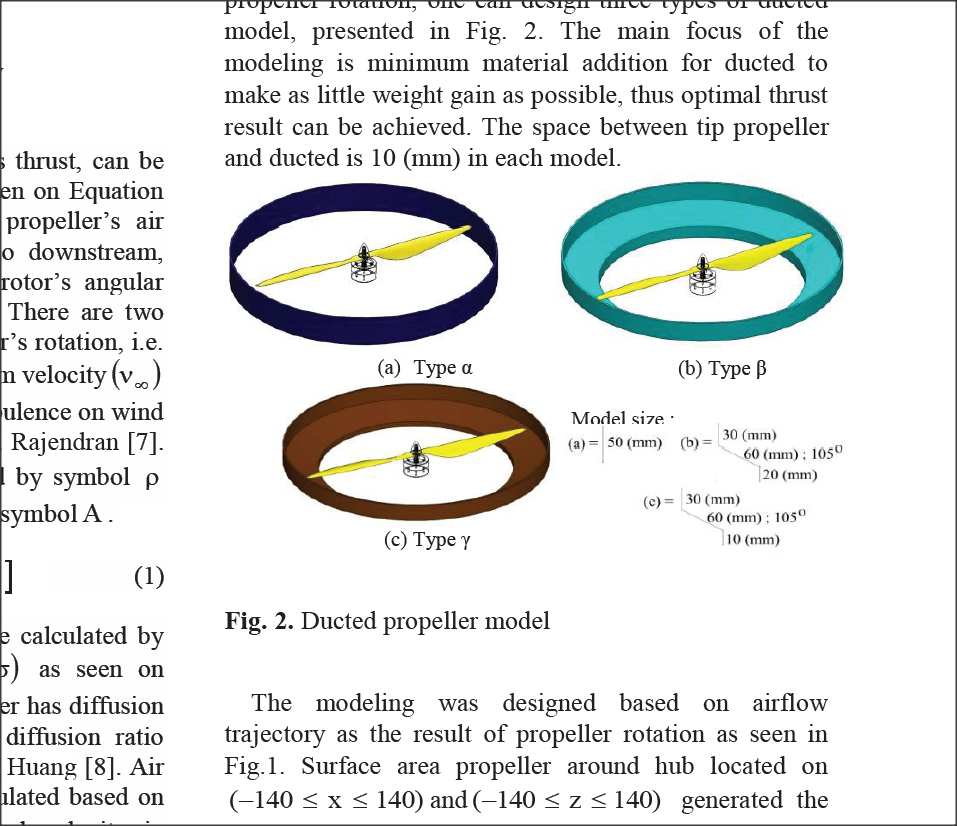
Also, they don't account for a curved inlet.
Other sources show that 10 % diameter reduction on inlet to the propeller diameter is desirable. for general flight.
Maybe a little outlet restriction matches into the free air conditions better.
The amount of restriction required reduces with increasing speed (V0, aircraft speed) , where V1 is the output velocity at the propeller.
Also, reducing the propeller diameter on a motor automatically increases rpm, until torque needed balances the engine torque again.
if A drops by 19%, V increases from 21 to 23 m/s for the same thrust,
power = TV = 1.1 times original, same torque, = 1.1 x rpm.
now 1.1x velocity also = 1.1 x rpm. If rpm was 8000, it will now be 8800, so we are now producing the same thrust plus an extra efficiency factor, which balances the power inefficiency factor.
Now this motor produces more thrust with less power by, one assumes, an 8 inch propeller? (the original motor table) - the table doesn't make sense- we need the original.
Last edited: