broken flyer
Member
Hello everyone 
I'm new to the forums here, just joined actually, but I've been following Flite Test for quite some time and I've been designing, scratch building, and flying model aircraft for most of my life and I thought you all might be interested in seeing what I have been working on over the past year. Granted the base air frame is a Versa Wing with the payload bay addition, so this may not fall under the "mad scratch built" category for some of you(I have seen some amazing builds on here), the power system for this plane which turned it into the versa rocket has been a little on the mad side though. Now as well as being an airplane guy I am a bit of a space nut and anyone who knows me knows that it is my dream to work in the private space industry and I've been working towards this goal in whatever capacity I've been able to since high school so when I started getting into rocket engine design a little over a year ago it was a logical leap for me. This story begins during a cold Minnesota winter in 2015 when I began experimenting with DIY amateur rocket engines and found moderate success with my third engine design of a PVC sugar rocket.
As I figured out the chemistry and the mechanics of rocket propulsion more I began to push the boundaries a bit and as is so often the case with rocket science the learning curve is pretty steep and I had my fair share of catastrophic failures.
Eventually though I got it dialed in and began flying what was essentially an overgrown bottle rocket to test the engines in flight.
All the while though in the back of my head I kept thinking that as cheap as these home built DIY engines were, they were inconsistent performance wise and still more expensive than the propellant itself that was inside them. I wanted a fully reusable rocket engine that I could just keep refilling again and again so that I could fly rocket powered model airplanes with it frequently and not have it be prohibitively expensive. So as I refined my understanding of solid propellant rocket engine design, I began the design for what would become the XR58 rocket engine...
I designed this new engine to be 3D printed out of stainless steel, but I realized right away that it was going to expensive and heavy so before I spent any money on a full blown prototype I went back to my DIY engine building experience and built what I would call an analog of the design to validate the sizing and general operating principal, the XR58E for expendable. This engine worked beautifully, it worked exactly as intended, no unpredictable behavior and it had an almost linear thrust profile which was exactly what I wanted knowing that I would be using this to fly a rocket plane at some point.
With renewed confidence I decided to get an engine printed, but I still wasn't ready to spend the money to do one out of steel and I was wary of how much it would weigh, so I did a variation of the design that I believed would work with 3D printed ceramic instead. The 3D printed ceramic engine had an excellent surface finish(since was glazed after being printed), was heat resistant to over 3,000 degrees Fahrenheit, was lighter, and was approximately 10% of the cost to produce the initial design out of stainless so despite knowing beforehand how brittle ceramic alone could be I decided to try it anyway. Unfortunately it just crumbled essentially when ignited(well cracked actually), but you get the idea. Not a good material for making a rocket engine out of(by itself anyway, larger solid propellant engines have used ceramic inserts in the throat of the nozzle). At the time the only 3D printing service that offered ceramic was located in Europe and if I recall correctly I believe this first 3D printed engine of mine was printed in Germany.
Finally admitting to myself that ceramic alone wasn't going to cut it, I broke down and dished out the money to do the first prototype out of 3D printed stainless steel.
Now with an engine that could handle the pressure and the heat(for the most part, I did have an issue with nozzle erosion initially), I began testing and I fired that engine 5 or 6 times over the course of a couple of weekends and proved to myself that it was possible to do a fully reusable engine this way. This engine was heavy though and because I had opted for a longer burn duration and lower thrust, the power to weight ratio on that first engine was not good enough to fly anything really.
It was around this time that the internet began to take notice. 3DPrint Article on the XR58 Engine
The prototype engine was heavy though as aforementioned and I was not happy with the quality of the product. The design at the time lent itself to the nozzle twisting during the manufacturing process and there was an unacceptable amount of nozzle erosion for the desired lifespan of the engine, so I went back to the drawing board, taking my design and iterating to a new design that would have the same performance, be significantly cheaper, lighter, more versatile/adjustable, and durable. Behold the second version or the "production"version of the XR58 Engine. While I was still having some quality issues with the prints I received(and still am, though I'm working on this with the supplier), the performance of this engine was perfect, I couldn't have asked for it to work any better or be more consistent, especially given the inconsistent nature of the propellant(more on this further down). I did experience a number of failures with this engine during testing when I was trying to get more thrust out of the engine than it was designed to do, but in the baseline configuration as designed, it performed flawlessly on the test stand.
Finally I had something I could put on an airplane... However, now I needed an airframe and it was surprisingly hard to find an airframe suitable for a rocket engine and a relatively heavy one(the trade off for making it out of steel so it'll last rather than cardboard or plastic like most disposable model rocket engines). Having designed and built quite a few models before I instantly started getting grandiose ideas of all the cool models I could build and fly with this engine(a profile model of a Me163 is currently at the top of my list when I get to that point), but I needed something quick that I knew would fly to try it on so I could eliminate a variable or two and in stepped my friend and co-worker(we both work at Cirrus Aircraft full time in the manufacturing engineering department for SF50 product development) and he offered up his old tried and true Versa Wing for the task as he was an avid Flite Test follower as well and has a small fleet of their designs. Thus was born the "Versa Rocket".
We have "flown" the Versa Rocket a couple times now and attempted to fly it many times, but it's been rough. Lacking a purpose built launch rail and the combination of the Versa Wing being slightly too large/heavy for the XR58 engine we haven't had the best luck getting it off the pad(it's veered off sideways a couple times because it wasn't placed perfectly center and has gotten hung up on the ground a few times).
The most successful flight we had ended in a tip stall/snap roll that put the wing into the ground after a few seconds of air time(the XR58 actually has a 7 second burn duration in the baseline configuration so it should be really awesome on a purpose built airframe) and the least successful flights ended in destruction...
We have suffered two explosions during all of these flight attempts, both due to irregularities/anomalies in the fuel(cracks, air pockets, voids, etc), but I am confident this can be avoiding in the future by closely inspecting everything after fueling and potentially be alleviated altogether in the future with more thermally stable propellant mixes.
Anyway, I have lots more pictures and video of both partial success and failures that I have yet to upload so keep an eye out for those soon! With any luck when we get another wing built(planning on using a modified mini arrow for the next attempts) and the time to work on this stuff some more there should be rocket flights galore and lots of great video!
What do you guys think? Anything I missed that you'd like to know? Things you'd like to see pictures of or videos? I'll try to oblige you if I have them. Or just project ideas for reusable RC rocket gliders in the future?
I know I've got a few I can hardly wait to build once we get some solid(no pun intended) rocket flight experience under our belts 
I'm new to the forums here, just joined actually, but I've been following Flite Test for quite some time and I've been designing, scratch building, and flying model aircraft for most of my life and I thought you all might be interested in seeing what I have been working on over the past year. Granted the base air frame is a Versa Wing with the payload bay addition, so this may not fall under the "mad scratch built" category for some of you(I have seen some amazing builds on here), the power system for this plane which turned it into the versa rocket has been a little on the mad side though. Now as well as being an airplane guy I am a bit of a space nut and anyone who knows me knows that it is my dream to work in the private space industry and I've been working towards this goal in whatever capacity I've been able to since high school so when I started getting into rocket engine design a little over a year ago it was a logical leap for me. This story begins during a cold Minnesota winter in 2015 when I began experimenting with DIY amateur rocket engines and found moderate success with my third engine design of a PVC sugar rocket.
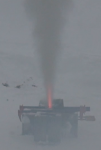
As I figured out the chemistry and the mechanics of rocket propulsion more I began to push the boundaries a bit and as is so often the case with rocket science the learning curve is pretty steep and I had my fair share of catastrophic failures.
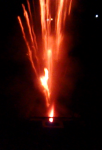
Eventually though I got it dialed in and began flying what was essentially an overgrown bottle rocket to test the engines in flight.
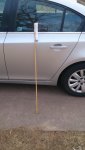
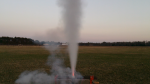
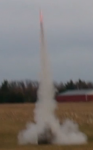
All the while though in the back of my head I kept thinking that as cheap as these home built DIY engines were, they were inconsistent performance wise and still more expensive than the propellant itself that was inside them. I wanted a fully reusable rocket engine that I could just keep refilling again and again so that I could fly rocket powered model airplanes with it frequently and not have it be prohibitively expensive. So as I refined my understanding of solid propellant rocket engine design, I began the design for what would become the XR58 rocket engine...
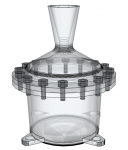
I designed this new engine to be 3D printed out of stainless steel, but I realized right away that it was going to expensive and heavy so before I spent any money on a full blown prototype I went back to my DIY engine building experience and built what I would call an analog of the design to validate the sizing and general operating principal, the XR58E for expendable. This engine worked beautifully, it worked exactly as intended, no unpredictable behavior and it had an almost linear thrust profile which was exactly what I wanted knowing that I would be using this to fly a rocket plane at some point.
With renewed confidence I decided to get an engine printed, but I still wasn't ready to spend the money to do one out of steel and I was wary of how much it would weigh, so I did a variation of the design that I believed would work with 3D printed ceramic instead. The 3D printed ceramic engine had an excellent surface finish(since was glazed after being printed), was heat resistant to over 3,000 degrees Fahrenheit, was lighter, and was approximately 10% of the cost to produce the initial design out of stainless so despite knowing beforehand how brittle ceramic alone could be I decided to try it anyway. Unfortunately it just crumbled essentially when ignited(well cracked actually), but you get the idea. Not a good material for making a rocket engine out of(by itself anyway, larger solid propellant engines have used ceramic inserts in the throat of the nozzle). At the time the only 3D printing service that offered ceramic was located in Europe and if I recall correctly I believe this first 3D printed engine of mine was printed in Germany.
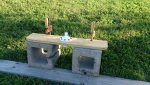
Finally admitting to myself that ceramic alone wasn't going to cut it, I broke down and dished out the money to do the first prototype out of 3D printed stainless steel.
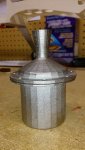
Now with an engine that could handle the pressure and the heat(for the most part, I did have an issue with nozzle erosion initially), I began testing and I fired that engine 5 or 6 times over the course of a couple of weekends and proved to myself that it was possible to do a fully reusable engine this way. This engine was heavy though and because I had opted for a longer burn duration and lower thrust, the power to weight ratio on that first engine was not good enough to fly anything really.
It was around this time that the internet began to take notice. 3DPrint Article on the XR58 Engine
The prototype engine was heavy though as aforementioned and I was not happy with the quality of the product. The design at the time lent itself to the nozzle twisting during the manufacturing process and there was an unacceptable amount of nozzle erosion for the desired lifespan of the engine, so I went back to the drawing board, taking my design and iterating to a new design that would have the same performance, be significantly cheaper, lighter, more versatile/adjustable, and durable. Behold the second version or the "production"version of the XR58 Engine. While I was still having some quality issues with the prints I received(and still am, though I'm working on this with the supplier), the performance of this engine was perfect, I couldn't have asked for it to work any better or be more consistent, especially given the inconsistent nature of the propellant(more on this further down). I did experience a number of failures with this engine during testing when I was trying to get more thrust out of the engine than it was designed to do, but in the baseline configuration as designed, it performed flawlessly on the test stand.
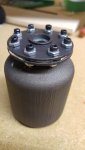
Finally I had something I could put on an airplane... However, now I needed an airframe and it was surprisingly hard to find an airframe suitable for a rocket engine and a relatively heavy one(the trade off for making it out of steel so it'll last rather than cardboard or plastic like most disposable model rocket engines). Having designed and built quite a few models before I instantly started getting grandiose ideas of all the cool models I could build and fly with this engine(a profile model of a Me163 is currently at the top of my list when I get to that point), but I needed something quick that I knew would fly to try it on so I could eliminate a variable or two and in stepped my friend and co-worker(we both work at Cirrus Aircraft full time in the manufacturing engineering department for SF50 product development) and he offered up his old tried and true Versa Wing for the task as he was an avid Flite Test follower as well and has a small fleet of their designs. Thus was born the "Versa Rocket".
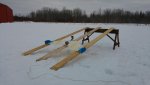
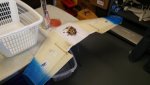
We have "flown" the Versa Rocket a couple times now and attempted to fly it many times, but it's been rough. Lacking a purpose built launch rail and the combination of the Versa Wing being slightly too large/heavy for the XR58 engine we haven't had the best luck getting it off the pad(it's veered off sideways a couple times because it wasn't placed perfectly center and has gotten hung up on the ground a few times).
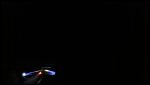
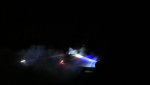
The most successful flight we had ended in a tip stall/snap roll that put the wing into the ground after a few seconds of air time(the XR58 actually has a 7 second burn duration in the baseline configuration so it should be really awesome on a purpose built airframe) and the least successful flights ended in destruction...
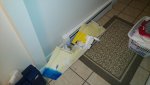
We have suffered two explosions during all of these flight attempts, both due to irregularities/anomalies in the fuel(cracks, air pockets, voids, etc), but I am confident this can be avoiding in the future by closely inspecting everything after fueling and potentially be alleviated altogether in the future with more thermally stable propellant mixes.
Anyway, I have lots more pictures and video of both partial success and failures that I have yet to upload so keep an eye out for those soon! With any luck when we get another wing built(planning on using a modified mini arrow for the next attempts) and the time to work on this stuff some more there should be rocket flights galore and lots of great video!
What do you guys think? Anything I missed that you'd like to know? Things you'd like to see pictures of or videos? I'll try to oblige you if I have them. Or just project ideas for reusable RC rocket gliders in the future?
Last edited: