telnar1236
Elite member
The LW PLA components of the F-104 are now all designed. The major changes since my last update are the addition of the elevator and rudder servos and the addition of ventilation for the battery. The ventral fin is also now present and correct but should only be included if building the airplane with landing gear. I had hoped to have the STL files this past weekend but ended up being busier than expected so you should be able to expect them tomorrow and maybe a couple files later this evening depending on how easy it is to divide the airframe for printing. There are a couple of normal PLA and ABS parts that need to be designed around the landing gear still (the nose gear mount, the gear struts, and the gear doors). In addition, there are a few peripheral parts like the battery tray and latch for the battery hatch as well as the mold for the canopy and 3D printed canopy options. Once the F-104 is ready to print in its entirety, I will move on to the modifications for a U-2 in the CAD model.
All four servos are visible in these pictures with linkages for most of them. I did not add linkages for the rudder because I was lazy but the control rod just runs parallel to the elevator control rod to the tail and will run to a PLA bell crank (not yet in CAD but will mount in the larger hole in front of the aileron servo) for the nose gear if that option is selected. The link from the gear servo to the nose gear is also not in CAD because the PLA nose gear mount is not yet present, but it should be pretty clear how it is installed.
Finally, the battery vents consist of a conformal inlet in the nose and vents above the main inlets for exhaust.
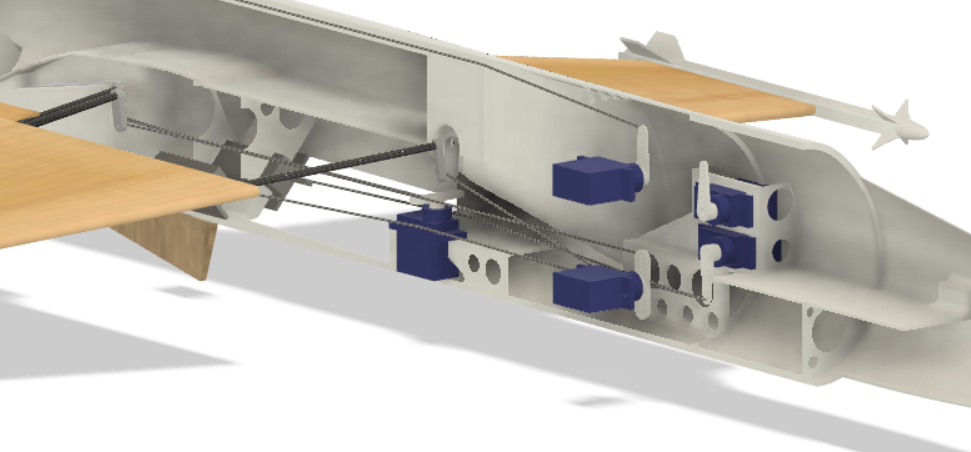
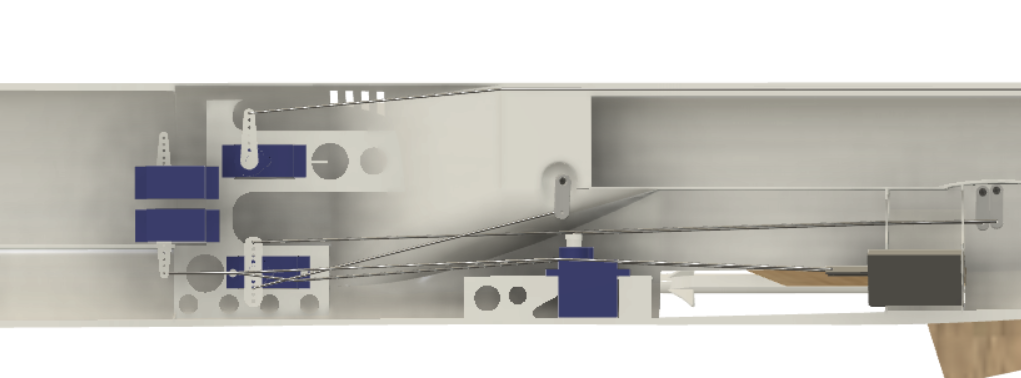
All four servos are visible in these pictures with linkages for most of them. I did not add linkages for the rudder because I was lazy but the control rod just runs parallel to the elevator control rod to the tail and will run to a PLA bell crank (not yet in CAD but will mount in the larger hole in front of the aileron servo) for the nose gear if that option is selected. The link from the gear servo to the nose gear is also not in CAD because the PLA nose gear mount is not yet present, but it should be pretty clear how it is installed.
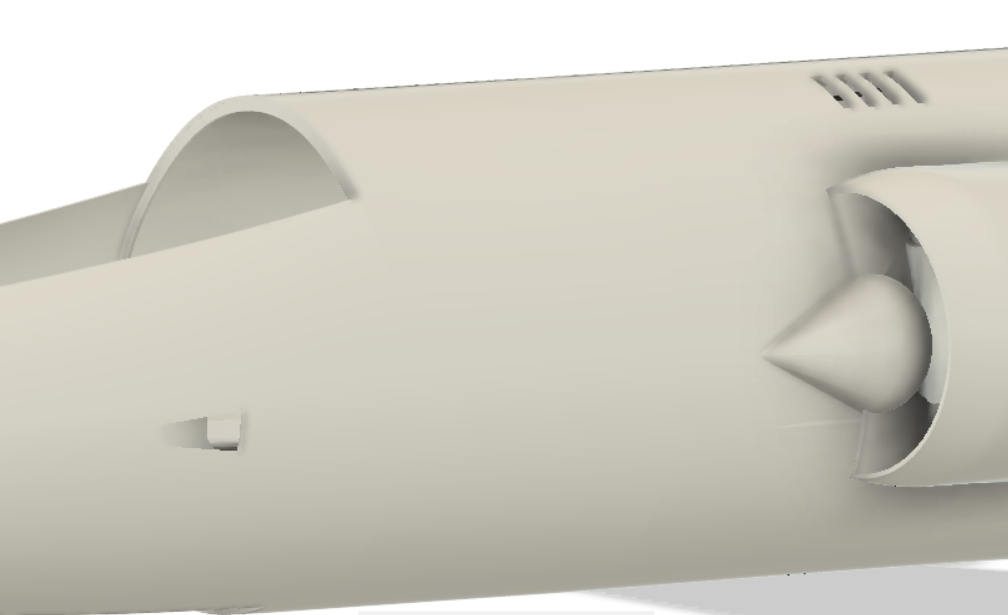
Finally, the battery vents consist of a conformal inlet in the nose and vents above the main inlets for exhaust.