telnar1236
Elite member
I automated leading edge flaps, but looking to do it by differential max high static pressure between upper and lower surfaces.
That sounds like a neat project. The immediate issue that comes to mind is that aerodynamics is nonlinear so even if you had an easy way to tell the LE flaps which way to go, you might just end up at a local maximum instead of an overall maximum for lift. I think the simplest way to go would be to gather a ton of data on the lift vs. angle of attack for your wing with multiple LE flap deflections and then use that data to generate a curve mapping LE flap deflection to angle of attack which you could then measure with either two pressure probes (which would require more data gathering) or more simply with the more conventional airfoil stuck to a rotary pot.
That's some great piloting of that F-22. I have noticed some EDFs are much more sensitive to inlet area than others. I had an old six blade 64mm from Hobbyking that ran on 3s and would outperform most of my 4s EDFs even with far too small of inlet/exhaust areas, but for most EDFs there is a notable difference. It's hard to find good data from the manufacturer but this is one of the few examples. It shows thrust and efflux speed vs. nozzle area and there is definitely a difference. It is also worth noting that efflux speed translates to thrust at speed so what might not be a huge deal at 10 or 20 mph is a big deal at 60 or 70 mph. Inlet area and inlet duct efficiency are even more critical.Played around with different techniques dealing with high alpha, stalls, and ducting with EDF's inlets as well as exhaust areas. Did testing to back it up. Interesting one was the SR-71 were I picked up good info on inlets and exits. Best project was trying to take a single 5 bladed EDF and bleeding off pressure to the end of the wing to counteract yaw so it will hover. Some success, watch the video.
Interested on your problems with stalls and ducting. You should see how I choked the EDF and it performed well.
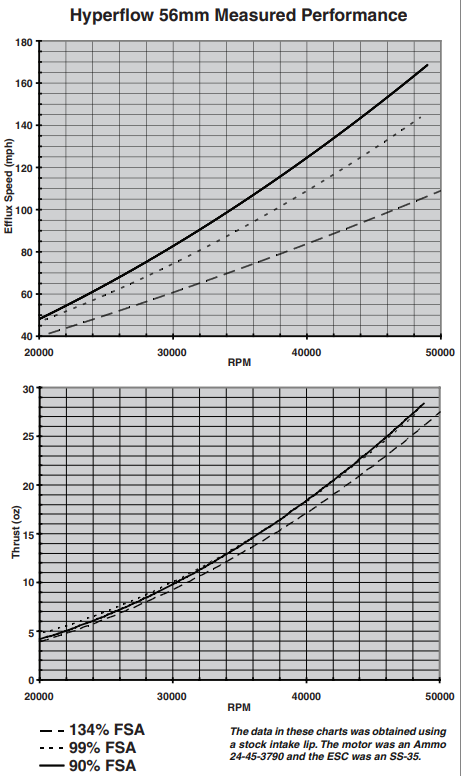
Last edited: