Taildragger
Legendary member
Not a bad bush plane tbh
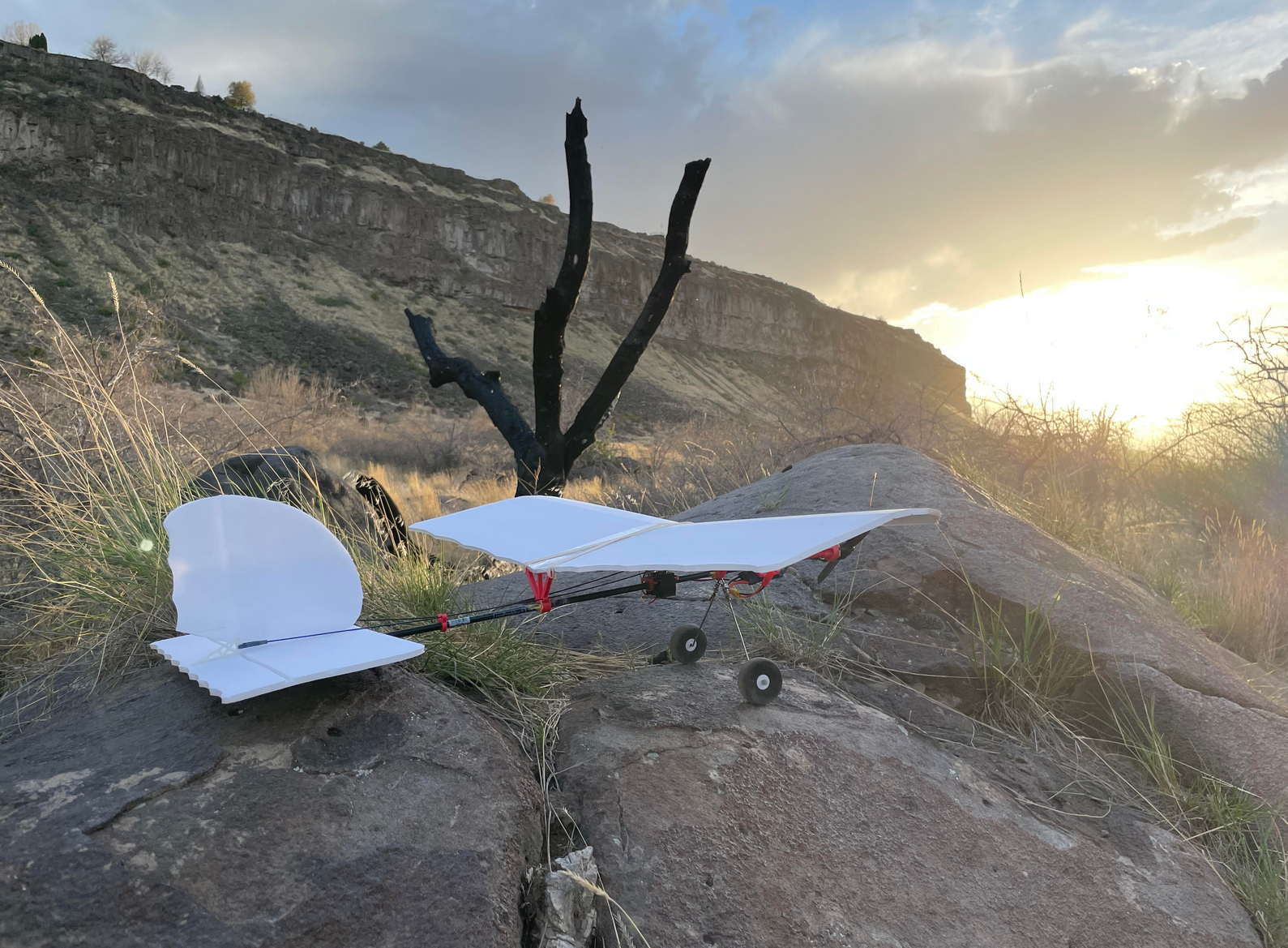
love the backgroundNot a bad bush plane tbh
View attachment 237360
do you have to be part of FTCA to get the plans
You do have to join but you can be a free memberdo you have to be part of FTCA to get the plans
Hello, I compared and scaled the placement of the parts,Can we get a hold of FT and see if they can add some details to the plans.... like shaft length, where to put the wing supports on the shaft, etc
I have arrow shafts, and some regular carbon shafts (with same dia.) that I ordered way back when.
Im doing the 3ch build as we speak
Edit: Also what dihedral? How to form wing under camber curve.... I know they are free plans but all they really gave ya was the basic wing and tail shapes and some STL files (that need modded as the rubber bands wont stay on the little nubs) 🤔🤦♂️🤷♂️
On mine, the PLA would snap when I tried to remove the supports from the print process. I finally decided if I couldn't manage to even get it cleaned up to install onto the plane, I was probably best not trusting it to hold up in flight. The servos are held into place in typical FT fashion, using hot glue. If I were making another and repeated this modification, I think I would make the servo box a bit longer, so I could move the tail surface servos farther back on the plane, and shorten the push rods for them. As it is, I used two of the wire guides to help make sure I wouldn't have problems with the rods flexing instead of activating the surfaces.Hi Everyone,
I have most of my parts printed out but having a problem with the servo holder. One of loops on the end of the servo holder wants to break in have. Has this happened to you ? I see Hoomi has a different idea to hold his servos. I don't know how to beef up the loops on the servo holder. I also don't know how to use TinkerCad.
Is it possible to print this if it is view only?For those of us who only have 9gram servos on hand, I remade the servo holder it can be found Here( https://cad.onshape.com/documents/f...renderMode=0&uiState=64512f0aa81303542d3ff232 )
fixed!Is it possible to print this if it is view only?
Excellent very nice landing.I put mine up for her first three flights this morning. The first and third flights were flown using 3S 850 mAh batteries, with the Matecam 808 mounted at the back of the wing to offset the additional weight, while the second flight was flown using the specified 2S 800 mAh battery. With the 2S battery, she balances almost perfectly level at the specified CG point from the plans. With the 3S batteries and the Matecam, she balances just a bit nose down. I'm flying mine 4 channel, and she's among the easiest landing planes I've flown. The nylon zip-tie tail skid worked great, and while ground steering with the rudder isn't as precise or responsive as a steerable tail wheel, she was manageable. On 2S, she was not able to pull a smooth vertical loop from level flight, but rather flopped over backwards before hitting achieving full inverted flight at the top, making more of a teardrop shaped loop. On 3S, she pulled a smooth, circular loop from level flight. Roll rate with my ailerons is decent. She's not a 3D stunt plane, but she'll handle some simple aerobatics. I didn't attempt inverted flight.
On the maiden flight portion of the video, I cut out most of the eastbound portions of the flight, as the sun was low enough to pretty much wash out the view on the camera. The takeoff and landing portions show what I mean pretty clearly.
The only issue I had during the flight, was that the checkerboard tape on the tail starting peeling back. I've secured it with some clear tape folded over the leading edge.
Floaty and slow!I waited until it was pretty much dead calm (in between rain showers here) flew fine. I needed quite a bit of left rudder and the "maximum trim reached" was for my elevator. I put in some 'reflex' because I thought for sure it would need some up trim, but I was wrong.
Ricky
Floaty and slow!
What is the length of your arrow?