quorneng
Master member
In 1947 the Air Ministry requested proposals for designs to quickly make use the latest swept wing information.
Hawker responded by simply adding swept wings to the Sea Hawk then nearing production. The ministry accepted the proposal and ordered 3 be built, two to fly and one for static testing. With such a relatively simple change work progressed quickly the first flying in 1948. The second early the following year.
After nearly a year of development flying the static testing indicated the rear fuselage in particular needed reinforcing so Hawker took the opportunity to build a new rear fuselage for the second P1052 but with a single exhaust at the tail. It was renamed the p1081.
The redundant rear fuselage was reinforced and fitted to the first P1052. Test flying continued and in 1952 with an arrestor hook fitted under took carrier landing trials. It was later fitted with a swept tail plane for further high speed testing. It eventually demonstrated that the modest performance improvement from the swept wing did not justify the poorer handling characteristics, particularly for carrier operations so it was retired in 1953.
Amazingly it still exists in the Fleet Air Arm museum at Yeovilton.
As it uses a visually identical fuselage to the Sea Hawk and I already have the plans and built techniques so I though it would be interesting to build a P1052 for comparison to my XPS foam Sea Hawk. It just so happen I have a 'spare' 55 mm EDF too!
As the Sea Hawk's inlet proved to be rather inefficient I would take the opportunity to improve the inlet geometry even at a slight exhaust sacrifice.
The complete duct and EDF ready for a thrust test.
As I hoped the thrust was significantly better being close to 430 g. An big improvement on the Sea Hawk.
It meant there was no reason not to proceed!
As before the centre section half shell is first with the duct 'inserted' exactly half way in.
I did actually overlook the fact that the EDF was in a slightly different location compared to the Sea Hawk so the formers needed quite a bit of 'doctoring' to get the duct to fit but fortunately the XPS is easy to cut and to add to as required.
So far so good.
Hawker responded by simply adding swept wings to the Sea Hawk then nearing production. The ministry accepted the proposal and ordered 3 be built, two to fly and one for static testing. With such a relatively simple change work progressed quickly the first flying in 1948. The second early the following year.
After nearly a year of development flying the static testing indicated the rear fuselage in particular needed reinforcing so Hawker took the opportunity to build a new rear fuselage for the second P1052 but with a single exhaust at the tail. It was renamed the p1081.
The redundant rear fuselage was reinforced and fitted to the first P1052. Test flying continued and in 1952 with an arrestor hook fitted under took carrier landing trials. It was later fitted with a swept tail plane for further high speed testing. It eventually demonstrated that the modest performance improvement from the swept wing did not justify the poorer handling characteristics, particularly for carrier operations so it was retired in 1953.
Amazingly it still exists in the Fleet Air Arm museum at Yeovilton.
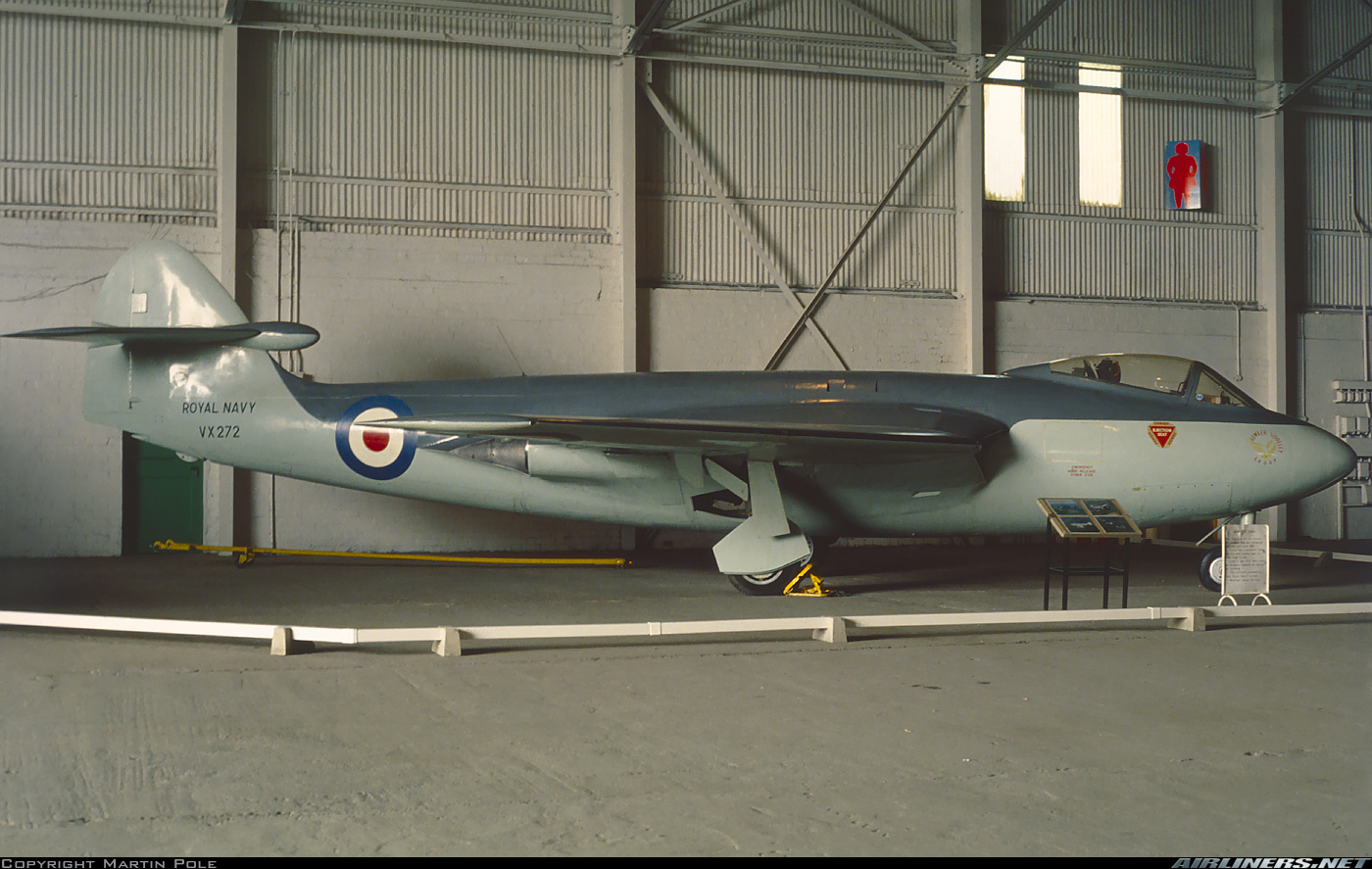
As it uses a visually identical fuselage to the Sea Hawk and I already have the plans and built techniques so I though it would be interesting to build a P1052 for comparison to my XPS foam Sea Hawk. It just so happen I have a 'spare' 55 mm EDF too!
As the Sea Hawk's inlet proved to be rather inefficient I would take the opportunity to improve the inlet geometry even at a slight exhaust sacrifice.
The complete duct and EDF ready for a thrust test.
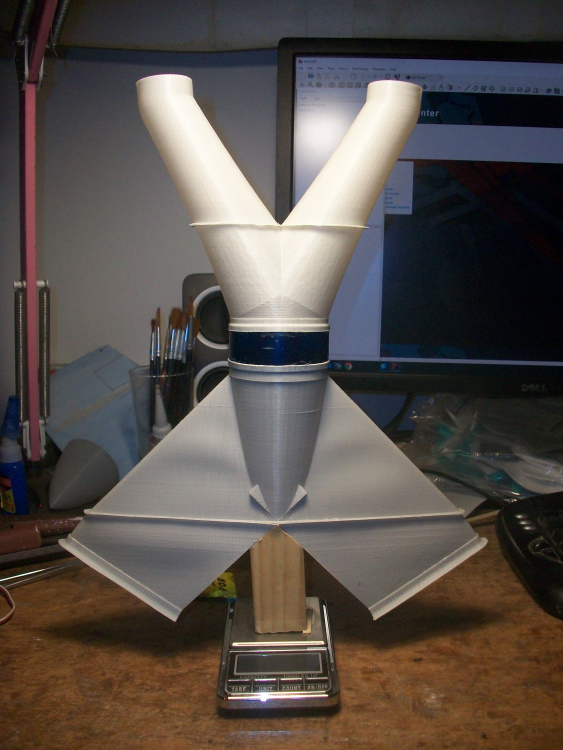
As I hoped the thrust was significantly better being close to 430 g. An big improvement on the Sea Hawk.
It meant there was no reason not to proceed!
As before the centre section half shell is first with the duct 'inserted' exactly half way in.
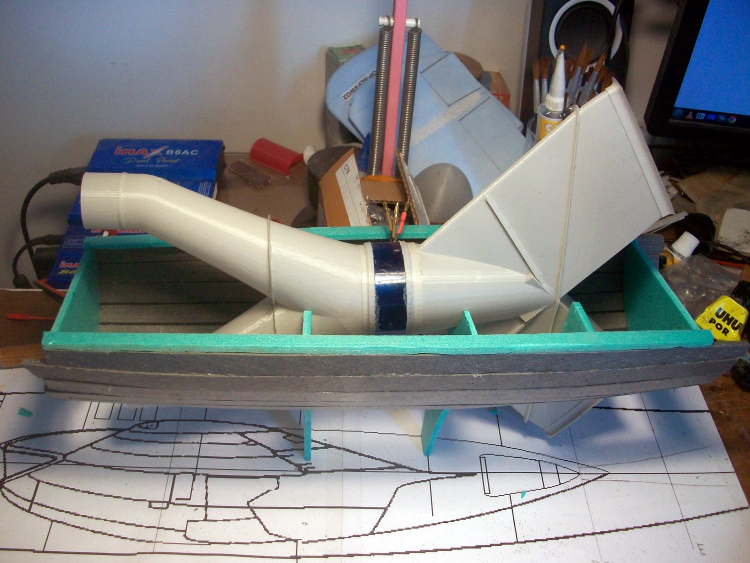
I did actually overlook the fact that the EDF was in a slightly different location compared to the Sea Hawk so the formers needed quite a bit of 'doctoring' to get the duct to fit but fortunately the XPS is easy to cut and to add to as required.
So far so good.