I had mixed results this weekend. The wheels are looking pretty good:
I did two tire profiles - both seem to work, the first one has squared shoulders and prints easier:
The second one I filleted the edge where the curved face meets the flat sides:
The second one looks more like a real skate wheel - but is trickier to print since there's less in contact with the build plate, and it doesn't come out as symmetrical since the one side tends to sag while printing without support (and supports and TPU don't play nice together.)
They both have the same OD and since the wheels only roll on the crown they're interchangeable. I wouldn't mix them on a pair of skates...but on the low rider they should be fine to mix and match. I have 3 of the rounder profile and 1 square profile on my mockup and it seems fine.
I also did a test of a modified hub that should be stronger despite having holes in it:
It should be stronger since those holes get multiple perimeters around them so it gives more material than if this was just infilled. But...it's really not necessary for the low-rider and the hubs take more than twice as long to print this way - it's also a bit of a pain to line the holes up on the two hub halves. So...I only did one like this as a demo.
The tires should be printed with 6 perimeters. My first test only used 3 and made for a squishy tire due to the low infill:
The 4 I'm actually using have 6 perimeters and the center section is solid TPU from the crown to the PLA hub. They have very little give and seem to be totally usable.
The tires are kind of tricky to assemble...and once together do not come apart without destroying the tire. In fact - I'd probably put them in real skates and skate on them if I still had a pair to try it on. They wouldn't last very long - but I'm fairly confident they're structurally sound enough they could be used to support a full sided adult.
The wheels consist of 3 pieces - 2 identical hubs and 1 tire:
The hubs are stacked - you could glue them but there's really no need:
The stacked hubs are then pressed into the tire - which takes some force despite the flexibility of the TPU:
The hubs are then rotated - the point shown in the photo is the trickiest part - getting the tire over the "lip" of the tall part of the hub takes considerable force:
I found it helps to put a long bolt or piece of all thread through the hub to get more leverage doing this:
Also - when I assembled my first Y plate I found why the bearing spacers are important. I accidentally tightened one of the bolts through a wheel too much and found out that it creates enough force to damage the bearings. The PLA hubs (I used MakerGeeks impact modified Raptor PLA) held up to the clamping force just fine...but the bearings themselves gave in and the inner races got squished inward without the spacer to keep them in place. Oops. Not sure if I should be impressed with how strong this Raptor PLA is...or shocked at how weak these super cheap Chinese bearings are. (There bearings were $2 for 10 from wish.com I bought them mostly to see just how bad they were....they're better than I expected but still terrible bearings.)
But...I made more progress than just playing with wheels...going to split that into a second post though....
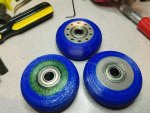
I did two tire profiles - both seem to work, the first one has squared shoulders and prints easier:
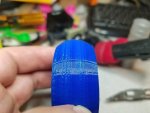
The second one I filleted the edge where the curved face meets the flat sides:
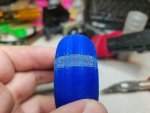
The second one looks more like a real skate wheel - but is trickier to print since there's less in contact with the build plate, and it doesn't come out as symmetrical since the one side tends to sag while printing without support (and supports and TPU don't play nice together.)
They both have the same OD and since the wheels only roll on the crown they're interchangeable. I wouldn't mix them on a pair of skates...but on the low rider they should be fine to mix and match. I have 3 of the rounder profile and 1 square profile on my mockup and it seems fine.
I also did a test of a modified hub that should be stronger despite having holes in it:
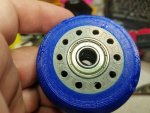
It should be stronger since those holes get multiple perimeters around them so it gives more material than if this was just infilled. But...it's really not necessary for the low-rider and the hubs take more than twice as long to print this way - it's also a bit of a pain to line the holes up on the two hub halves. So...I only did one like this as a demo.
The tires should be printed with 6 perimeters. My first test only used 3 and made for a squishy tire due to the low infill:
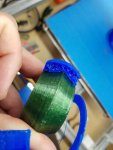
The 4 I'm actually using have 6 perimeters and the center section is solid TPU from the crown to the PLA hub. They have very little give and seem to be totally usable.
The tires are kind of tricky to assemble...and once together do not come apart without destroying the tire. In fact - I'd probably put them in real skates and skate on them if I still had a pair to try it on. They wouldn't last very long - but I'm fairly confident they're structurally sound enough they could be used to support a full sided adult.
The wheels consist of 3 pieces - 2 identical hubs and 1 tire:
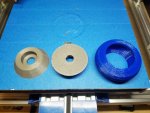
The hubs are stacked - you could glue them but there's really no need:
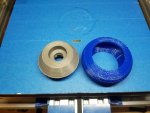
The stacked hubs are then pressed into the tire - which takes some force despite the flexibility of the TPU:
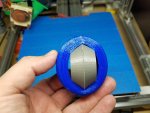
The hubs are then rotated - the point shown in the photo is the trickiest part - getting the tire over the "lip" of the tall part of the hub takes considerable force:
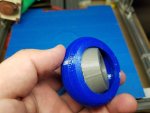
I found it helps to put a long bolt or piece of all thread through the hub to get more leverage doing this:
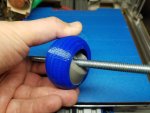
Also - when I assembled my first Y plate I found why the bearing spacers are important. I accidentally tightened one of the bolts through a wheel too much and found out that it creates enough force to damage the bearings. The PLA hubs (I used MakerGeeks impact modified Raptor PLA) held up to the clamping force just fine...but the bearings themselves gave in and the inner races got squished inward without the spacer to keep them in place. Oops. Not sure if I should be impressed with how strong this Raptor PLA is...or shocked at how weak these super cheap Chinese bearings are. (There bearings were $2 for 10 from wish.com I bought them mostly to see just how bad they were....they're better than I expected but still terrible bearings.)
But...I made more progress than just playing with wheels...going to split that into a second post though....