I have 2 2805.6 1800 KV motors 9 inch prop.,
plus 2 x 1408,3600 KV 4 inch prop,
plus 1 x 1306 4000 Kv, 3 8inch prop
I want to control them from a Matek f765 flight controller, loaded with Ardupilot software/firmware.
I suppose that means 5 channels, and an extra switch somewhere.
Any ideas on haw to set this up? How do you normally do Flaps and undercarrage?
I want the 3 smaller motors to be roll and pitch controlled at low speed, and cut off over 40 mph.
1) does the Matek have enough motor channels, or do I need a different controller?
2) what current do the smaller motors draw, and can the battery handle it.?
The battery is 4000 mAh 30C 4S.
I am adding the 3 extra small motors and props to convert my tailsitter design to STOL.
The reasoning is the ability to ground launch and land on farm paddocks. The grass is often not a stable platform,
and a rolling launch/land requires 3 inch plus wheels.
My old free-flighter used to land Ok, at about 36 inches and 1.5 lbs.
It landed fairly quickly, at about 20 mph, and rolled along nicely.
It even survived several fence hits with only minor damage.
Possibly the extra lift is not needed, but takeoff stability is an issue.
The aircraft will be off the ground before flight speed is reached. Pitch and roll need to be managed.
Also, more specs on the 3 smaller motors would be good.
I can only get the motors from Banggood, and they don't have lengthy descriptions-
just the S-number. They are all 4S capable.
Brands are: Aurora rc d1306 and Iflight xing c1408
Never mind weights. Current drain with specific props would be useful.
It would be handy to know their projected thrust as well. Should they have an overriding throttle, or just on/off?
I don't expect the 3 small motors to lift 1.4 to 1.6 kgs by themselves.
This is more in the range of 4 x 5 inch prop motors.
Ultra-light "stick" bell motors are 8.5 g, ones with threads and nuts on the prop shaft are around 16 g.
Which are the best props? 5 or 6 inch pitch? 3 or 4 blades?
For both motor/ prop diameter cases.
Specific blade shapes? I know the smaller one look like large props hacked off half way!
I want them to run in tubes/rings/ducts, optimised for static thrust.
Also, where can I find good duct profile layouts for different ducts?
The 4 inch ones go through the wings, at about 30mm deep,
(1.2 ins) and the 3 inch one goes through the fuselage, at 200mm deep (8 inches)
Here is a picture of the specs, which I do not fully understand.
<edit>
dshot is the esc protocol, pwm is for actuators.
There are 9 devices to be controlled.
The Matek spec shows 12, of which 10 are dshot- capable.
does this mean it can run 4 actuators and 8 motors at once??
Uart is universal asynchronous receiver transmitter. There are 7.
Is this used for just the receiver, or for other devices?
Is this also for telemetry output? The receiver needs at least 5 channels- I suppose they come in 1, 2,3,4,6 ,8,....
Receiver should be 2.4 Ghz digital, video is 5.8 GHz analog.
Can this controller mix the telemetry into the analog output of the video?
How would that be wired up? camera > flight controller > 5.8 GHz transmitter??
I see it mentions 5V, 9V, 12V, 3.3 V LDO??
LDO = low dropout regulator, 200mA.
What runs off this? is this for low power voltage regulation for the receiver?
plus 2 x 1408,3600 KV 4 inch prop,
plus 1 x 1306 4000 Kv, 3 8inch prop
I want to control them from a Matek f765 flight controller, loaded with Ardupilot software/firmware.
I suppose that means 5 channels, and an extra switch somewhere.
Any ideas on haw to set this up? How do you normally do Flaps and undercarrage?
I want the 3 smaller motors to be roll and pitch controlled at low speed, and cut off over 40 mph.
1) does the Matek have enough motor channels, or do I need a different controller?
2) what current do the smaller motors draw, and can the battery handle it.?
The battery is 4000 mAh 30C 4S.
I am adding the 3 extra small motors and props to convert my tailsitter design to STOL.
The reasoning is the ability to ground launch and land on farm paddocks. The grass is often not a stable platform,
and a rolling launch/land requires 3 inch plus wheels.
My old free-flighter used to land Ok, at about 36 inches and 1.5 lbs.
It landed fairly quickly, at about 20 mph, and rolled along nicely.
It even survived several fence hits with only minor damage.
Possibly the extra lift is not needed, but takeoff stability is an issue.
The aircraft will be off the ground before flight speed is reached. Pitch and roll need to be managed.
Also, more specs on the 3 smaller motors would be good.
I can only get the motors from Banggood, and they don't have lengthy descriptions-
just the S-number. They are all 4S capable.
Brands are: Aurora rc d1306 and Iflight xing c1408
Never mind weights. Current drain with specific props would be useful.
It would be handy to know their projected thrust as well. Should they have an overriding throttle, or just on/off?
I don't expect the 3 small motors to lift 1.4 to 1.6 kgs by themselves.
This is more in the range of 4 x 5 inch prop motors.
Ultra-light "stick" bell motors are 8.5 g, ones with threads and nuts on the prop shaft are around 16 g.
Which are the best props? 5 or 6 inch pitch? 3 or 4 blades?
For both motor/ prop diameter cases.
Specific blade shapes? I know the smaller one look like large props hacked off half way!
I want them to run in tubes/rings/ducts, optimised for static thrust.
Also, where can I find good duct profile layouts for different ducts?
The 4 inch ones go through the wings, at about 30mm deep,
(1.2 ins) and the 3 inch one goes through the fuselage, at 200mm deep (8 inches)
Here is a picture of the specs, which I do not fully understand.
<edit>
dshot is the esc protocol, pwm is for actuators.
There are 9 devices to be controlled.
The Matek spec shows 12, of which 10 are dshot- capable.
does this mean it can run 4 actuators and 8 motors at once??
Uart is universal asynchronous receiver transmitter. There are 7.
Is this used for just the receiver, or for other devices?
Is this also for telemetry output? The receiver needs at least 5 channels- I suppose they come in 1, 2,3,4,6 ,8,....
Receiver should be 2.4 Ghz digital, video is 5.8 GHz analog.
Can this controller mix the telemetry into the analog output of the video?
How would that be wired up? camera > flight controller > 5.8 GHz transmitter??
I see it mentions 5V, 9V, 12V, 3.3 V LDO??
LDO = low dropout regulator, 200mA.
What runs off this? is this for low power voltage regulation for the receiver?
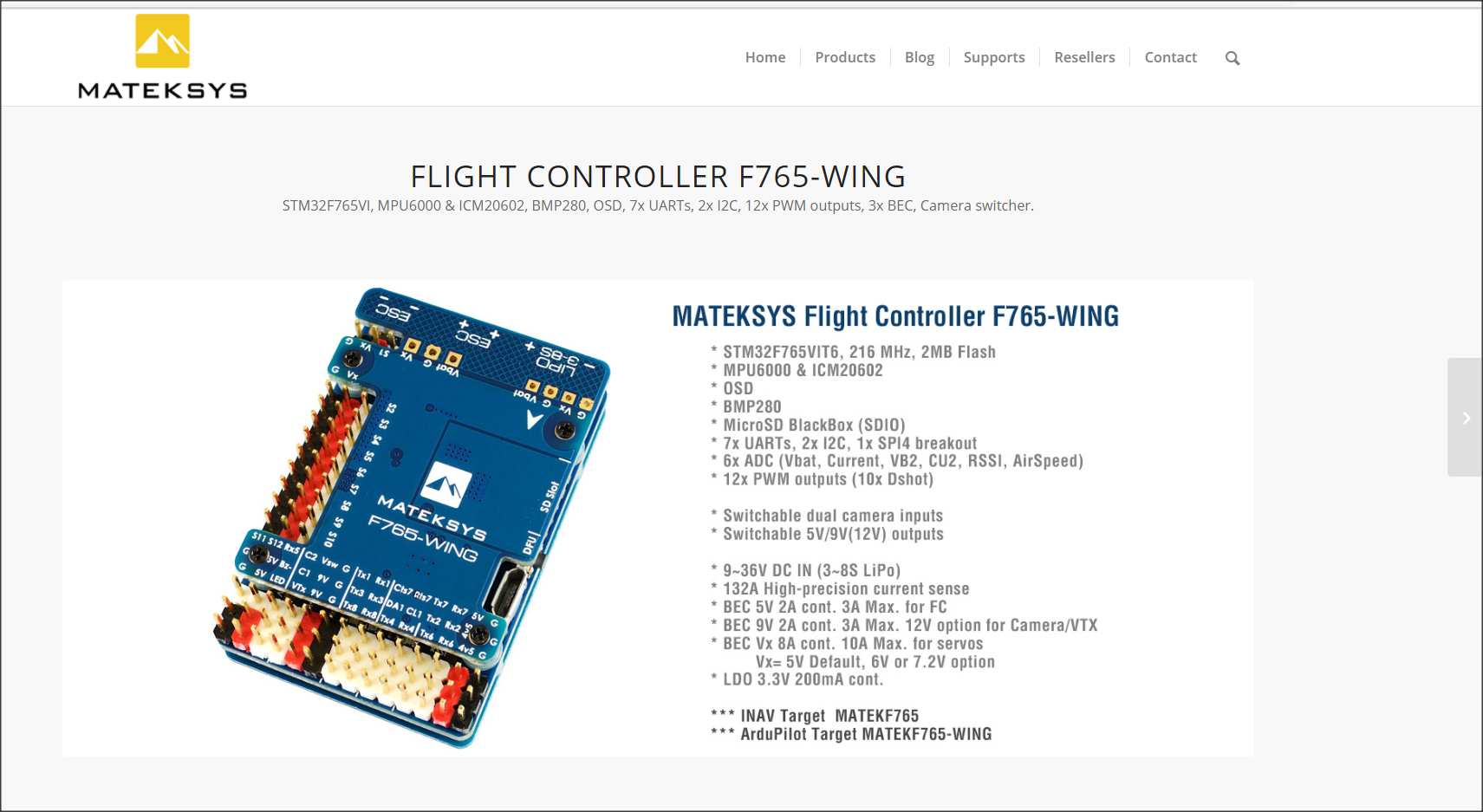
Last edited: