quorneng
Master member
Plane Print have for sale the print files for a 1.5m span Seagull both as a glider and EDF powered. The majority of it is printed in LW_PLA.
It certainly seems to fly but I was a bit concerned at the all up weight of the EDF version at 560g given it is using just a 40 mm EDF. Some of the EDF versions made ended up at over 600g.
I have to admit it does look very realistic making full use of sweeping shapes possible with printing. It using elevons and a rudder tail so is in effect a flying wing.
In the past I have built a couple of small scale planes using 2mm Depron. Both came out below 250g.
A 600mm span DH Venom with a 40 mm EDF. 202g
A 800 mm EE Canberra with 30 mm EDFs. 248g.
Would it be possible to do the same to make a Seagull?
A 3 view drawing of a possible layout.
Likely to be a bit smaller than the Plane Print version at only 1.2m span but then it should only be half the weight.
A bit more of an 'aeroplane' than a flying wing with an elevator and differential ailerons but a fixed fin. A configuration I have used in many EDFs although in this case the tail 'volume' will be very limited. The only printed parts would be the EDF inlet and exhaust ducts.
I came across a very nice QX 30 mm EDF that is claimed to deliver over 200g on 3s.
It only weighs 21g so as long as the ducting does not absorb too much thrust and the 250g limit is achieved it should do.
The next task is some 'test' ducts to find out what actually happens.
There is no rush as the UK is moving into winter and this is quite likely to be a 'tricky to fly' lightweight.
It certainly seems to fly but I was a bit concerned at the all up weight of the EDF version at 560g given it is using just a 40 mm EDF. Some of the EDF versions made ended up at over 600g.
I have to admit it does look very realistic making full use of sweeping shapes possible with printing. It using elevons and a rudder tail so is in effect a flying wing.
In the past I have built a couple of small scale planes using 2mm Depron. Both came out below 250g.
A 600mm span DH Venom with a 40 mm EDF. 202g
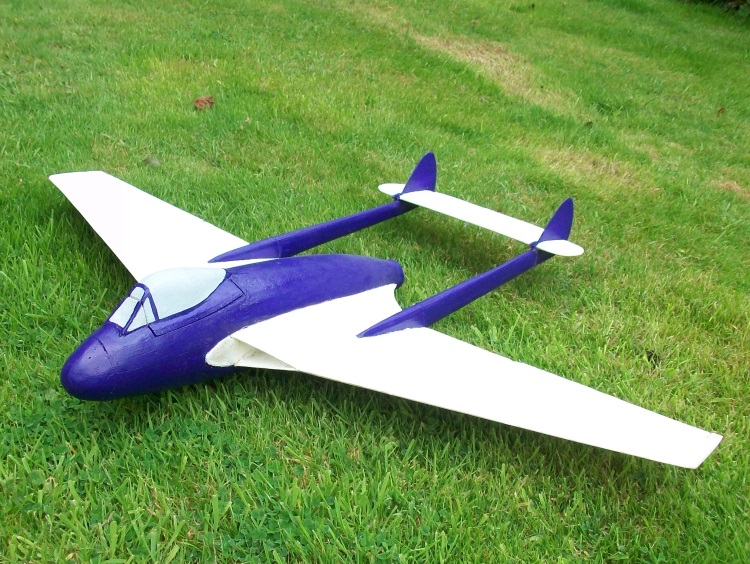
A 800 mm EE Canberra with 30 mm EDFs. 248g.
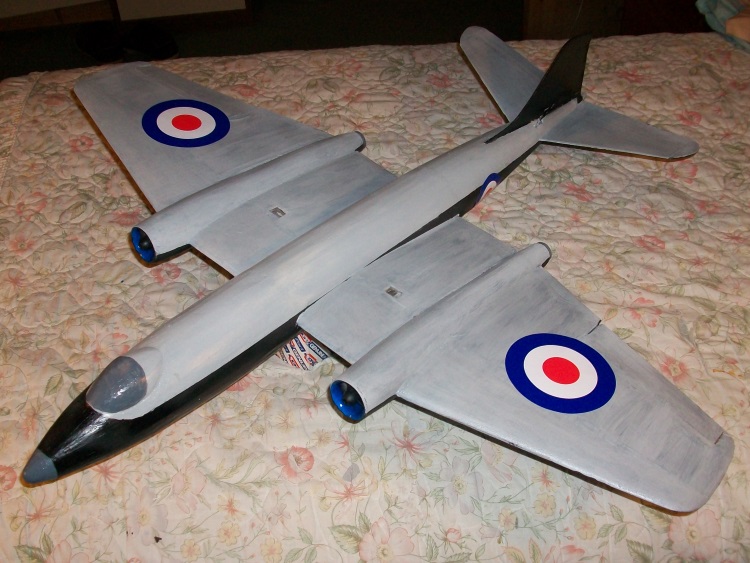
Would it be possible to do the same to make a Seagull?
A 3 view drawing of a possible layout.

Likely to be a bit smaller than the Plane Print version at only 1.2m span but then it should only be half the weight.
A bit more of an 'aeroplane' than a flying wing with an elevator and differential ailerons but a fixed fin. A configuration I have used in many EDFs although in this case the tail 'volume' will be very limited. The only printed parts would be the EDF inlet and exhaust ducts.
I came across a very nice QX 30 mm EDF that is claimed to deliver over 200g on 3s.
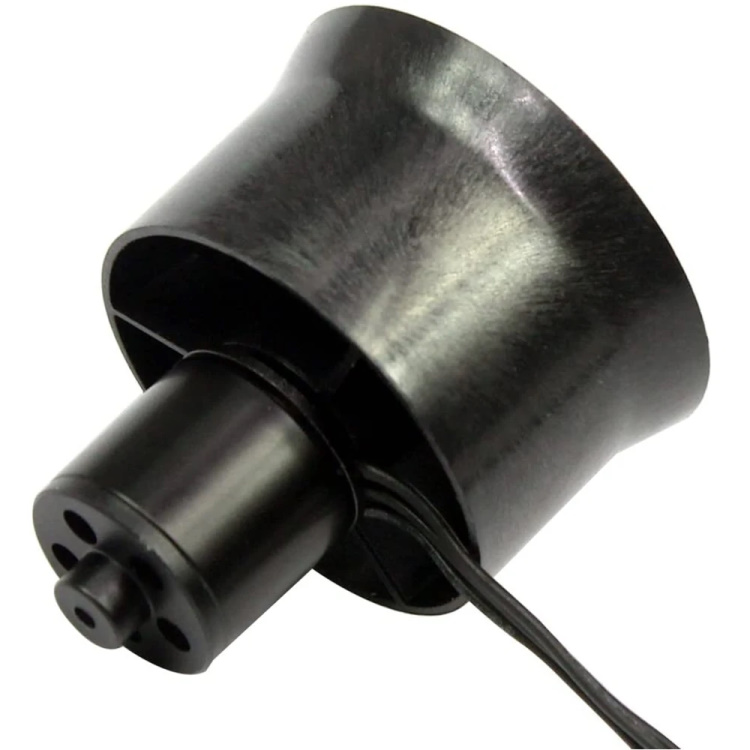
It only weighs 21g so as long as the ducting does not absorb too much thrust and the 250g limit is achieved it should do.
The next task is some 'test' ducts to find out what actually happens.
There is no rush as the UK is moving into winter and this is quite likely to be a 'tricky to fly' lightweight.
Last edited: