Pieliker96
Elite member
2022's Wing
2023's Wing
Now it's time for 2024.
Proposed design revisions:
1. Bigger batteries and more efficient aero (higher AR, more streamlining) for more endurance. Target is 20 minutes.
2. Bigger overall size, more overall weight, more inertia to be less affected by collisions.
3. Make liberal use of composites for strength, ditch protruding nose for impact/crashworthiness.
4. Move to a contra-rotating setup, both props in the same slot, for more thrust and noise, possibly some engine-out capability.
5. Ditch dead weight of the lighting system.
6. Increase snag-and-drop parachute size to have a bigger effect on captured targets. Move to two tow lines for double the capture capability.
7. Get a RX with signal diversity to hopefully stop the dropout issues. Possibly change protocols.
8. Removable wings for transport.
9. Bring spare parts and stock to Flite Fest for on-site repairs.
The basic weight and balance is done, as is the planform. Projected weight is 3.4kg which with a wing area of 1088in^2 is a WCL of 5.77. The TWR should be the same if the thrust scales linearly with two motors. If contrarotation makes it more or less efficient, the TWR will be affected accordingly. I'm planning to keep the same prop from last year's setup on top, then vary the lower prop while testing for maximum static thrust.
Hoping for some good combat action this year.
2023's Wing
Now it's time for 2024.
Proposed design revisions:
1. Bigger batteries and more efficient aero (higher AR, more streamlining) for more endurance. Target is 20 minutes.
2. Bigger overall size, more overall weight, more inertia to be less affected by collisions.
3. Make liberal use of composites for strength, ditch protruding nose for impact/crashworthiness.
4. Move to a contra-rotating setup, both props in the same slot, for more thrust and noise, possibly some engine-out capability.
5. Ditch dead weight of the lighting system.
6. Increase snag-and-drop parachute size to have a bigger effect on captured targets. Move to two tow lines for double the capture capability.
7. Get a RX with signal diversity to hopefully stop the dropout issues. Possibly change protocols.
8. Removable wings for transport.
9. Bring spare parts and stock to Flite Fest for on-site repairs.
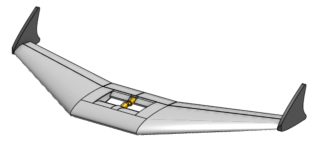
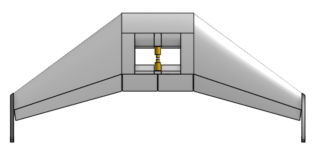
The basic weight and balance is done, as is the planform. Projected weight is 3.4kg which with a wing area of 1088in^2 is a WCL of 5.77. The TWR should be the same if the thrust scales linearly with two motors. If contrarotation makes it more or less efficient, the TWR will be affected accordingly. I'm planning to keep the same prop from last year's setup on top, then vary the lower prop while testing for maximum static thrust.
Hoping for some good combat action this year.
Last edited: