telnar1236
Elite member
I recently picked up a few Dumas kits at a yard sale. All but one were static display models, but since they are all balsa, I think they should be good for RC conversion. The F-105 looked like the simplest model to work with (I ended up with an F-105, and F-4, a Harrier, and a MiG 17 for a grand total of $43) so I am starting with that one and if it goes well I will probably convert the others over time. I haven't had much time to build recently so a small kit is about my speed right now. My current plan is to run a lightweight 40mm EDF unit with 250g of thrust running on a 1000 mAh 2s battery while aiming for an AUW under 300g. Covering will be a combination of very thin fiberglass sheeting and balsa. The control scheme I am currently aiming for is tailerons and a rudder. I need to resist the urge to add servo-driven retracts. I am adding carbon fiber reinforcements to the wings and horizontal stabilizer, but everything else looks good.
I got started this evening and assembled the wings and started a bit on the fuselage. The next step is to make the fiberglass internal ducting. and finish the assembly of the fuselage. This should be a pretty quick build because of how nice the Dumas kits are.
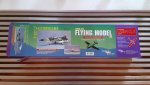
I got started this evening and assembled the wings and started a bit on the fuselage. The next step is to make the fiberglass internal ducting. and finish the assembly of the fuselage. This should be a pretty quick build because of how nice the Dumas kits are.
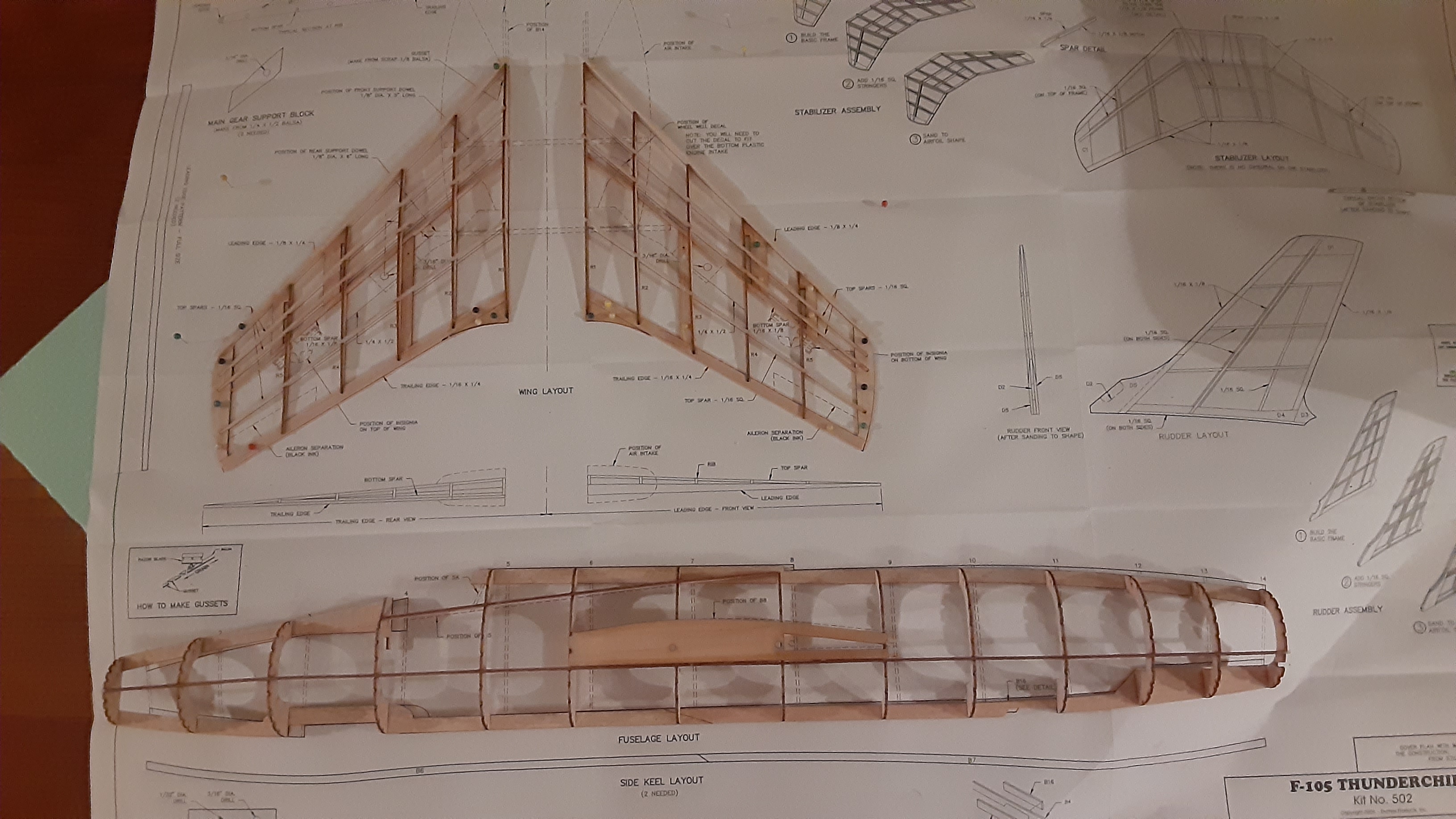
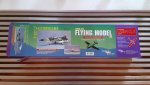