bracesport
Legendary member
The last pieces of the puzzle are in place!
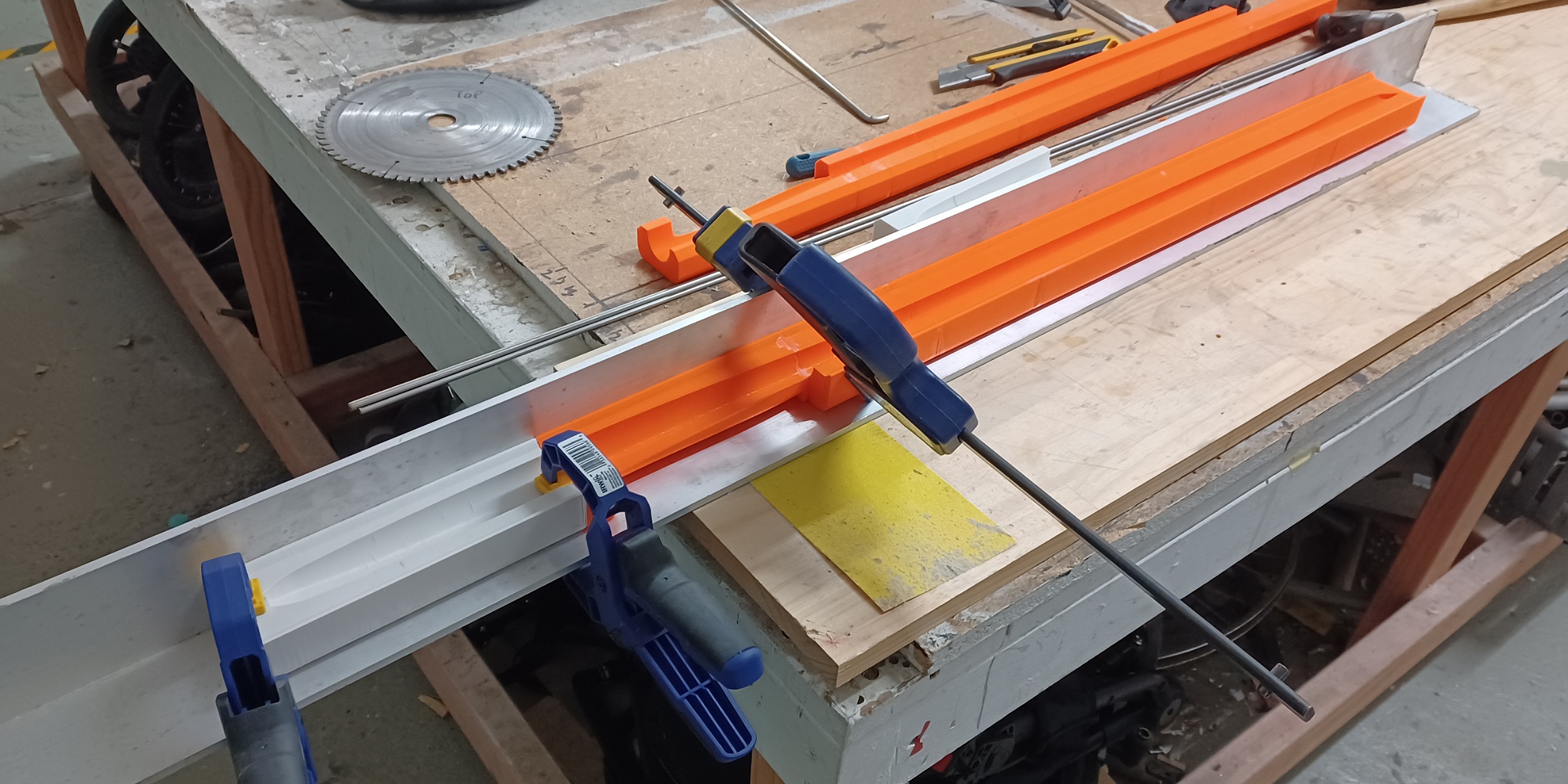
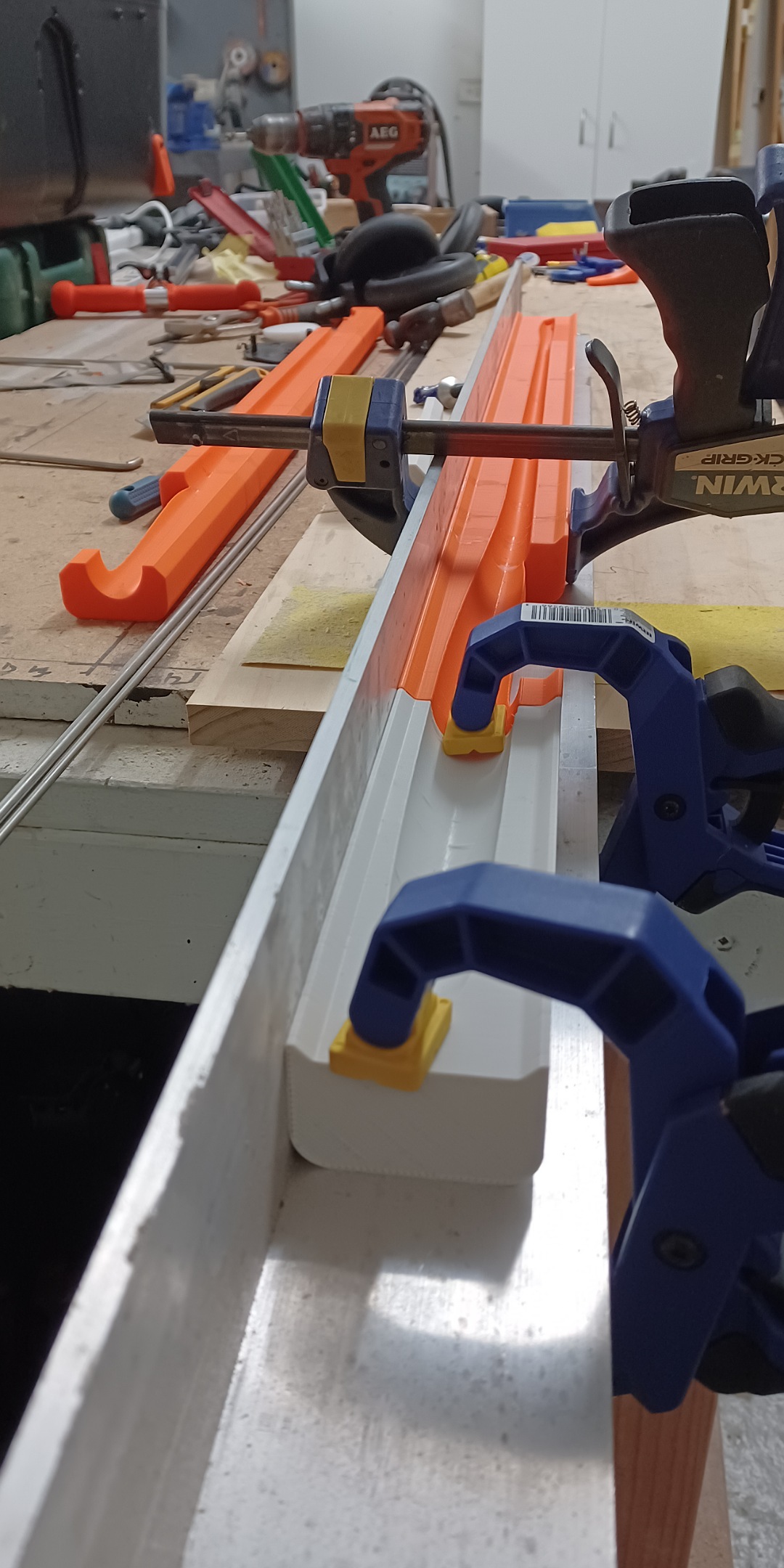
Some more tweaking - 80% slimmer fuse section in vertical direction - the purple nose section that houses the servos is a 3D printed part that is removable and will be better for different configurations and modifications (including a prop version) - the 3D printed section has a 7mm CF tube for stiffness - the flaperon pushrods are now in perfect alignment for a straight run - battery up front - Rx through slot at the base of the 3D printed part - looks pretty good I think.
View attachment 220909 View attachment 220910 View attachment 220911
With you having refinements at the ultimate end of the spectrum using carbon-fiber/epoxy cured in female molds and gorgeous streamlining, I find it odd that you would leave the horns outside in the slipstream. Is there some technical/logistics reason you don't use short torque tubes on the aileron hinge line and have the horns on the inside... just a few millimeters inward?
Some more CAD tweaks - this time I have made the wing joiner a 'V' for the dihedral and tapered it to match the shear web - I think it will better integrate with the shear web and be a little easier to make - I am planning laminated popsicle sticks covered with UD CF and a CF braided sock for the joiner - the sleeve will be CF braided sock and joined in with the shear web and wing skins - there will be an end cap for the wings to further integrate the joiner sockets - well that's the theory anyway.
I have been thinking more seriously to make the Phantom III an F5K ship - my tweak on it is to go V tail with pull strings
Just now finding your thread and being newer than when it started, I'm going back through it. Apologies if I ask a question that you answered later. If I don't ask it when I find it, I'll forget.
Really top notch aerospace industry techniques you're using!
I see you mentioning shear webs, caps and assuming you're optimizing lay-ups for those. Since you find 170 grams heavy and seeing this post, I wonder... are you doing structural analysis? Closed-form, Mechanics of Materials or numerical, FEA? If so, what kind of margins are shooting for? Do you have any specifications on your CF?
Cool stuff!![]()