Pieliker96
Elite member
Main Gear
The main gear on version 1 worked well but was a bit tempermental - the solder joints in the main bogies cracked occasionally, which was a pain to repair. This time, I went with a simpler approach: brass rods through the side walls of a small aluminum u-channel section, with wheel collars holding everything together. It's more or less the same weight but quite a lot stronger. I also added some bits of wire to keep the bogies at the right angle instead of the previously used rubber bands.
Nose Gear
I've had the idea to make a braking system for a while now, it could have certainly been beneficial on the first flight of V1. The system I devised is constructed from control horns, brass tubing, and steel wire. The circular control horns have a radius filed into their splines that seats against the gear strut. When the horns are rotated, they cam outwards. They are synchronized by bits of steel wire sliding in the brass tube, free on one side and crimped on the other (the tubing is anchored in the holes of the control horn), which also butt up against the strut to provide a zero location . An appendage was anchored to the assembly to provide more leverage for the actuator servo. The outer face of the circular control horns and the inside of the wheels were coated with hot glue with a bias towards the outside to serve as a braking material. Springs were added between the horns and the wheels to keep the friction low when the brakes are not engaged; a free-running wheel could inadvertantly contact the braking face due to side loading of the gear.
Note that the brake is self-releasing: brake engagement tries to turn the control horns in a way that would disengage them. If the opposite were true, the mechanism could easily jam uncommanded. In addition, compressing the oleo strut decreases the braking action. Ideally, these serve as a sort of anti-skid and prevent the nose gear from being ripped out of the fuselage, depending on how effective the brakes turn out to be; the system is resistant to jamming and is positively actuated by the brake servo.
A bit of aluminum u-channel was crimped onto the upper part of the oleo. A flat was filed on the back of the channel to allow a seat and positive mount for the servo, after which it was glued and zip-tied into place. All of the hardware seems to clear the retracts. The servo is mechanically isolated from the steering system for simplicity.
Here's a gif of the brakes in action. If a picture is worth a thousand words, a video is worth a million.
The braking system is of minimal weight and adds a much-needed feature for such a large craft. Testing will tell how well it works.
Spars
Carbon fiber is awesome, super light and super strong. Version 1 used layered poplar square stock that was installed as an afterthought into the wings. The carbon fiber I'm using is a bit heavier but much, much stronger, and it gives me the peace of mind of not having to worry about the wings folding in flight. They'll also be used for removable vertical stabilizers, which had previously been bashed quite a lot during transport due to being in such an exposed position.
Servos
The main wing servos on the original craft were ES3054s, which were operating right around their specced torque figures. Combine that with the servos gradually working loose and having to be reglued, shoddy linkage geometry, and some sketchy wiring, and you've got a loss of primary flight controls waiting to happen. V2's wings will have much beefier servos with around three times the original torque, better anchoring within the wing, and more skookum control linkages. The remaining ES3054s will be used in their original positions at the vertical stabilizers and nose wheel steering as well as the brake servo and canard flap, which was previously a (rather inadequate) 9-gram.
ESCs
Heatshrink provides mechanical protection for the components on the PCB but also acts as a massive thermal insulator. The "heatsinks" on most ESCs are really just thermal masses, designed to soak up the energy and slowly radiate it away once the flight has ended. If you push the ESC too hard and overload that mass, you're in big trouble, because there's no good way to get rid of the heat - the only route is through the thermally restrictive heatshrink and into the air.
The thermal mass method works fine in most cases. If you do need more cooling performance, a simple mod is to cut off some of the heatshrink as seen below. This removes a good deal of that thermal resistance. If you'd like to go even further you can remove the heatsink and the thermal pad and just run the bare FETs (just make sure you've got a decent amount of airflow!) which can save a bit of weight and provide better cooling (provided the surface area reduction of "heatsink" to the FETs is more than offset by the decreased thermal resistance, although this may not be the case and therefore requires testing). Another mod is to add an actual real proper finned heatsink, which I have done in the past with great success. And of course, make sure there's a good deal of airflow, because it makes drawing away heat a whole heckuva lot easier than just using convection.
The ESCs on V1 were directly exposed to the airflow and stayed pretty cool (not "ouch" hot) over the short timeframe of the flight. In V2, they have been moved out of the intake duct airflow and will now source air from a yet undetermined source, most likely the nose gear hole or a NACA duct through the upper surface of the intake duct. The thermal mass alone is marginally enough to keep cool during a normal flight profile without airflow, as was determined through testing. A bit of extra airflow should remedy that.
The main gear on version 1 worked well but was a bit tempermental - the solder joints in the main bogies cracked occasionally, which was a pain to repair. This time, I went with a simpler approach: brass rods through the side walls of a small aluminum u-channel section, with wheel collars holding everything together. It's more or less the same weight but quite a lot stronger. I also added some bits of wire to keep the bogies at the right angle instead of the previously used rubber bands.
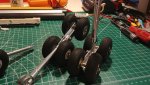
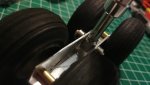
Nose Gear
I've had the idea to make a braking system for a while now, it could have certainly been beneficial on the first flight of V1. The system I devised is constructed from control horns, brass tubing, and steel wire. The circular control horns have a radius filed into their splines that seats against the gear strut. When the horns are rotated, they cam outwards. They are synchronized by bits of steel wire sliding in the brass tube, free on one side and crimped on the other (the tubing is anchored in the holes of the control horn), which also butt up against the strut to provide a zero location . An appendage was anchored to the assembly to provide more leverage for the actuator servo. The outer face of the circular control horns and the inside of the wheels were coated with hot glue with a bias towards the outside to serve as a braking material. Springs were added between the horns and the wheels to keep the friction low when the brakes are not engaged; a free-running wheel could inadvertantly contact the braking face due to side loading of the gear.
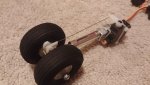
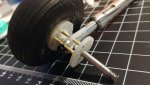
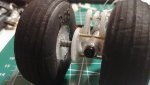
Note that the brake is self-releasing: brake engagement tries to turn the control horns in a way that would disengage them. If the opposite were true, the mechanism could easily jam uncommanded. In addition, compressing the oleo strut decreases the braking action. Ideally, these serve as a sort of anti-skid and prevent the nose gear from being ripped out of the fuselage, depending on how effective the brakes turn out to be; the system is resistant to jamming and is positively actuated by the brake servo.
A bit of aluminum u-channel was crimped onto the upper part of the oleo. A flat was filed on the back of the channel to allow a seat and positive mount for the servo, after which it was glued and zip-tied into place. All of the hardware seems to clear the retracts. The servo is mechanically isolated from the steering system for simplicity.
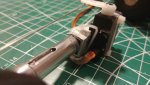
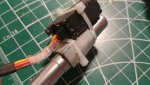
Here's a gif of the brakes in action. If a picture is worth a thousand words, a video is worth a million.
The braking system is of minimal weight and adds a much-needed feature for such a large craft. Testing will tell how well it works.
Spars
Carbon fiber is awesome, super light and super strong. Version 1 used layered poplar square stock that was installed as an afterthought into the wings. The carbon fiber I'm using is a bit heavier but much, much stronger, and it gives me the peace of mind of not having to worry about the wings folding in flight. They'll also be used for removable vertical stabilizers, which had previously been bashed quite a lot during transport due to being in such an exposed position.
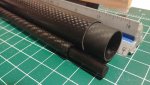
Servos
The main wing servos on the original craft were ES3054s, which were operating right around their specced torque figures. Combine that with the servos gradually working loose and having to be reglued, shoddy linkage geometry, and some sketchy wiring, and you've got a loss of primary flight controls waiting to happen. V2's wings will have much beefier servos with around three times the original torque, better anchoring within the wing, and more skookum control linkages. The remaining ES3054s will be used in their original positions at the vertical stabilizers and nose wheel steering as well as the brake servo and canard flap, which was previously a (rather inadequate) 9-gram.
ESCs
Heatshrink provides mechanical protection for the components on the PCB but also acts as a massive thermal insulator. The "heatsinks" on most ESCs are really just thermal masses, designed to soak up the energy and slowly radiate it away once the flight has ended. If you push the ESC too hard and overload that mass, you're in big trouble, because there's no good way to get rid of the heat - the only route is through the thermally restrictive heatshrink and into the air.
The thermal mass method works fine in most cases. If you do need more cooling performance, a simple mod is to cut off some of the heatshrink as seen below. This removes a good deal of that thermal resistance. If you'd like to go even further you can remove the heatsink and the thermal pad and just run the bare FETs (just make sure you've got a decent amount of airflow!) which can save a bit of weight and provide better cooling (provided the surface area reduction of "heatsink" to the FETs is more than offset by the decreased thermal resistance, although this may not be the case and therefore requires testing). Another mod is to add an actual real proper finned heatsink, which I have done in the past with great success. And of course, make sure there's a good deal of airflow, because it makes drawing away heat a whole heckuva lot easier than just using convection.
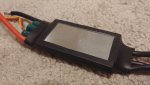
The ESCs on V1 were directly exposed to the airflow and stayed pretty cool (not "ouch" hot) over the short timeframe of the flight. In V2, they have been moved out of the intake duct airflow and will now source air from a yet undetermined source, most likely the nose gear hole or a NACA duct through the upper surface of the intake duct. The thermal mass alone is marginally enough to keep cool during a normal flight profile without airflow, as was determined through testing. A bit of extra airflow should remedy that.
-------------------- XB-70 V2: More Power, More Lift, More Engineering. --------------------