L Edge
Master member
High alpha and STOL devices are a kick to fly. Some work, others not so. I chose a real tough one . The DR Chinook.
Looking at some of the devices that he offers:
1) a raised leading edge of the wing
2) leading edge slot
3) endcaps
4) elevator that is angled
5)flap caps
6) oversize elevator control that produces a ground wake
and so on.
What I am going to do is build super light with a wing without any bracing and adding other devices that I have explored.
Since no plans are available, going to use some research and experimenting that I have done. Being "old school", out comes the paper, slide rule and drafting tools. This is what I have come up with using the gut feeling, study the figure over and over and going crazy. Finally I put the paper work away and now for the build.
So that is the starter. Leaving the wheel setup off for now to see if it will fly by chucking it.
Looking at some of the devices that he offers:
1) a raised leading edge of the wing
2) leading edge slot
3) endcaps
4) elevator that is angled
5)flap caps
6) oversize elevator control that produces a ground wake
and so on.
What I am going to do is build super light with a wing without any bracing and adding other devices that I have explored.
Since no plans are available, going to use some research and experimenting that I have done. Being "old school", out comes the paper, slide rule and drafting tools. This is what I have come up with using the gut feeling, study the figure over and over and going crazy. Finally I put the paper work away and now for the build.
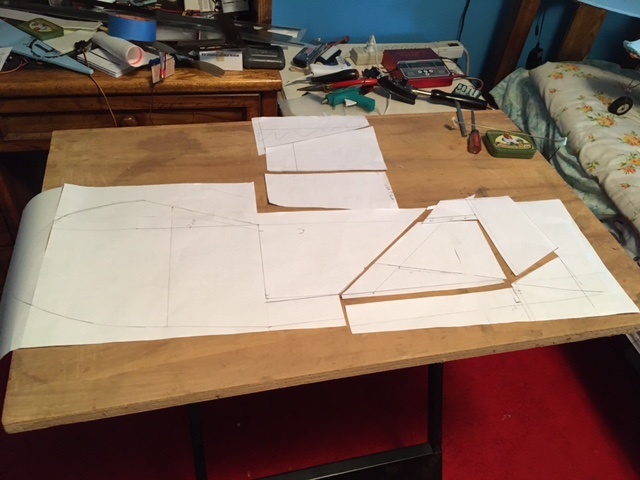
So that is the starter. Leaving the wheel setup off for now to see if it will fly by chucking it.