So... why is resin printing great for detailed parts but a huge pain for things where you need accurate dimensions?
Well, a couple of reasons.
First there's shrinkage. Resins shrink as they cure. Some don't shrink much, some can shrink as much as 7% or more. Thankfully the resins I've tried so far don't seem to shrink much - maybe 1-2%. And they seem to shrink evenly (unlike FDM where filaments that shrink tend to shrink more in X/Y than in Z) so this isn't a huge issue and usually able to be dealt with by scaling the part before slicing. On the parts I've been printing when I model them to the exact dimensions I want I find with grey resin I can just print them as is...but with the black I have I need to increase them 1-2% before printing.
Next there are a couple of issues due to the physics of MSLA printing. With FDM a part is built up from the ground up. With MSLA you're "pulling" the part out of a vat of resin. The way it actually works is when a layer is cured it sticks to the build plate and the FEP plastic that makes up the bottom of the vat. Then for the next layer to be printed the build plate is lifted which should "peel" the part off the FEP. The FEP is taught but flexible so as the part is pulled the FEP will release at the edges first as the center lifts up. This can actually put quite a bit of force on the part pulling it down (which to the part is up since the build process is kind of upside down) in some cases this can deform the part. It can also pull the part off it's supports or the build plate if there's more surface area on the FEP than there is on the build plate or there are insufficient supports. This is the main way failures seem to happen with MSLA printing.
And - some parts can be much worse than others for this. Hollow parts can be particularly tricky because they can create suction. It's generally advised to leave a vent hole in a part to prevent this. That might be possible on a decorative figurine....but on a functional part it can be much trickier. Take my lower knobs for example:
This is a failure I've seen a few times. The top of this image is where the part was adhered to the print bed. So you can see how after a few hundred layers the part stayed stuck to the print bed...but the new layers stuck to the FEP for part of it and didn't fully release. Eventually they did and this completed...but it left this deformity. At least that's my best guess for how this happened. Other parts on the build plate completed fine. It could have been an issue with the LCD...but it's a new printer so that seems unlikely. And I've had a lot of this part fail because of the suction issues printing a tube like this.
But...I can't just put a hole in the side of this part. I could add some extra material and make it taller and put a hole in there...but then I have to sand all that off in post and it wastes a bunch of resin. Lame.
So...how you do address this?
One popular solution is to print the part at an angle on supports. This prevents the closed tube that creates suction...it can also give you higher fidelity and hide some layer lines (not that they're very visible to begin with.) So let's try that!
Ick. The part facing up is what was towards the build plate. You can see how the parts sagged. You can also see a few zits left behind from the supports. With some post-processing sanding these could be made to work...but they'd be cosmetically scarred unless you were going to paint them. Fine for decorative stuff...but no good for functional
So back to putting them flat on the build platform...But how do we make sure they stick? We increase the exposure on the first few layers to make them harder. Except then they get overexposed and you get elephant foot:
It isn't terrible on this one...but most of my tests of this switch cap were really bad. And that bottom shape needs to be accurate because these snap onto tactile switches. I've actually done these in FDM before and they work...but I had to make the openings oversized and print them in ABS and vapor smooth them to get them even close...and they still look lumpy and inconsistent so I'm not happy with them:
The lumpy, glossy, inconsistent buttons bug the heck out of me on this. I really want to replace them with nice clean resin prints!
So if printing right on the bed gives elephant foot and deforms the bottom...why not just add some supports?
Well...let's try "light" supports that leave the smallest marks on the print:
Nope...the part warped in the peel process and pulled itself off. It stayed attached enough it didn't fail...but it's deformed
Ok...what about stronger "medium" supports:
Better...but it still came off and still deformed a bit. Ok....Heavy supports!
This time it stayed attached (this is after I pulled it off the supports...I'm just holding it in place to compare) but....
The bottom is all deformed between the supports. Again we're seeing the resin slumping as the first few layers were built up like we did with the angled knob.
I tried printing these switch caps angled as well and using supports from a different slicer...but they all came out with deformities in whatever was facing down. Adding more supports can minimize them...but then you have to remove the supports and the zits they leave...and it still doesn't result in a perfect result.
Arrgh! What can we do?
Well, a couple of reasons.
First there's shrinkage. Resins shrink as they cure. Some don't shrink much, some can shrink as much as 7% or more. Thankfully the resins I've tried so far don't seem to shrink much - maybe 1-2%. And they seem to shrink evenly (unlike FDM where filaments that shrink tend to shrink more in X/Y than in Z) so this isn't a huge issue and usually able to be dealt with by scaling the part before slicing. On the parts I've been printing when I model them to the exact dimensions I want I find with grey resin I can just print them as is...but with the black I have I need to increase them 1-2% before printing.
Next there are a couple of issues due to the physics of MSLA printing. With FDM a part is built up from the ground up. With MSLA you're "pulling" the part out of a vat of resin. The way it actually works is when a layer is cured it sticks to the build plate and the FEP plastic that makes up the bottom of the vat. Then for the next layer to be printed the build plate is lifted which should "peel" the part off the FEP. The FEP is taught but flexible so as the part is pulled the FEP will release at the edges first as the center lifts up. This can actually put quite a bit of force on the part pulling it down (which to the part is up since the build process is kind of upside down) in some cases this can deform the part. It can also pull the part off it's supports or the build plate if there's more surface area on the FEP than there is on the build plate or there are insufficient supports. This is the main way failures seem to happen with MSLA printing.
And - some parts can be much worse than others for this. Hollow parts can be particularly tricky because they can create suction. It's generally advised to leave a vent hole in a part to prevent this. That might be possible on a decorative figurine....but on a functional part it can be much trickier. Take my lower knobs for example:
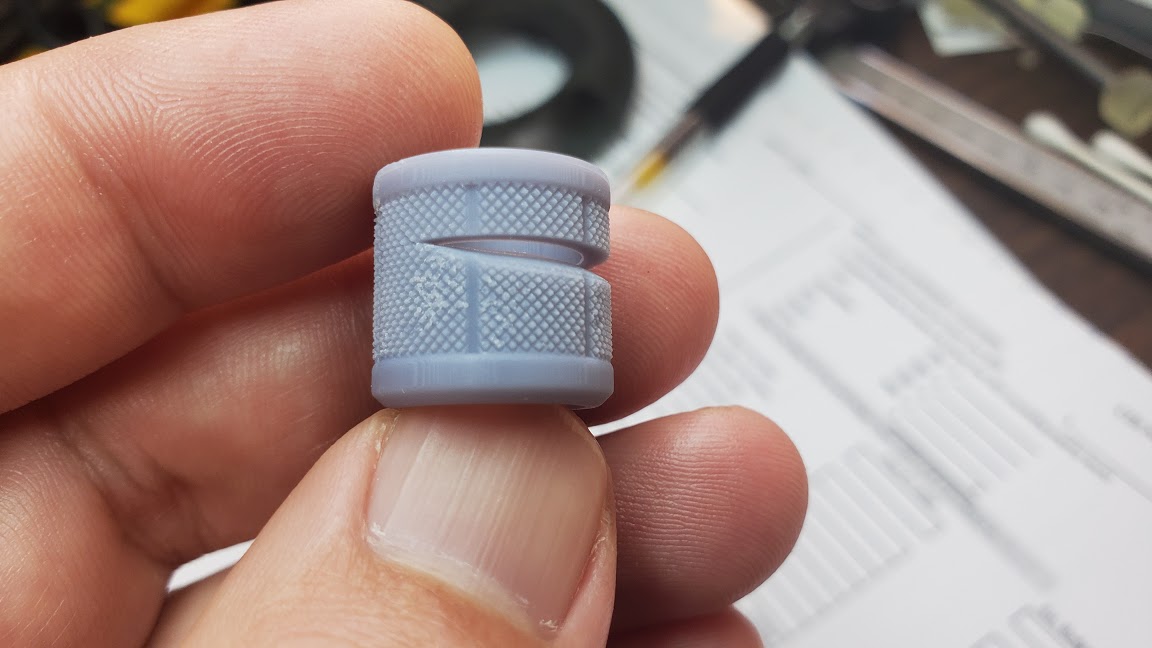
This is a failure I've seen a few times. The top of this image is where the part was adhered to the print bed. So you can see how after a few hundred layers the part stayed stuck to the print bed...but the new layers stuck to the FEP for part of it and didn't fully release. Eventually they did and this completed...but it left this deformity. At least that's my best guess for how this happened. Other parts on the build plate completed fine. It could have been an issue with the LCD...but it's a new printer so that seems unlikely. And I've had a lot of this part fail because of the suction issues printing a tube like this.
But...I can't just put a hole in the side of this part. I could add some extra material and make it taller and put a hole in there...but then I have to sand all that off in post and it wastes a bunch of resin. Lame.
So...how you do address this?
One popular solution is to print the part at an angle on supports. This prevents the closed tube that creates suction...it can also give you higher fidelity and hide some layer lines (not that they're very visible to begin with.) So let's try that!
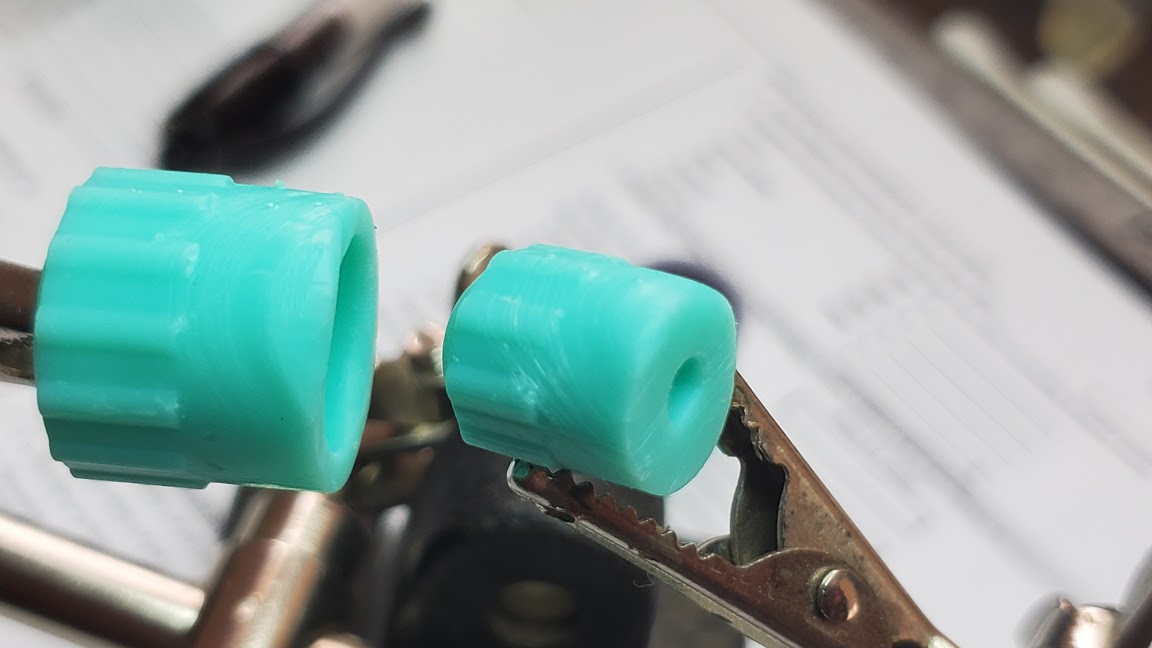
Ick. The part facing up is what was towards the build plate. You can see how the parts sagged. You can also see a few zits left behind from the supports. With some post-processing sanding these could be made to work...but they'd be cosmetically scarred unless you were going to paint them. Fine for decorative stuff...but no good for functional
So back to putting them flat on the build platform...But how do we make sure they stick? We increase the exposure on the first few layers to make them harder. Except then they get overexposed and you get elephant foot:
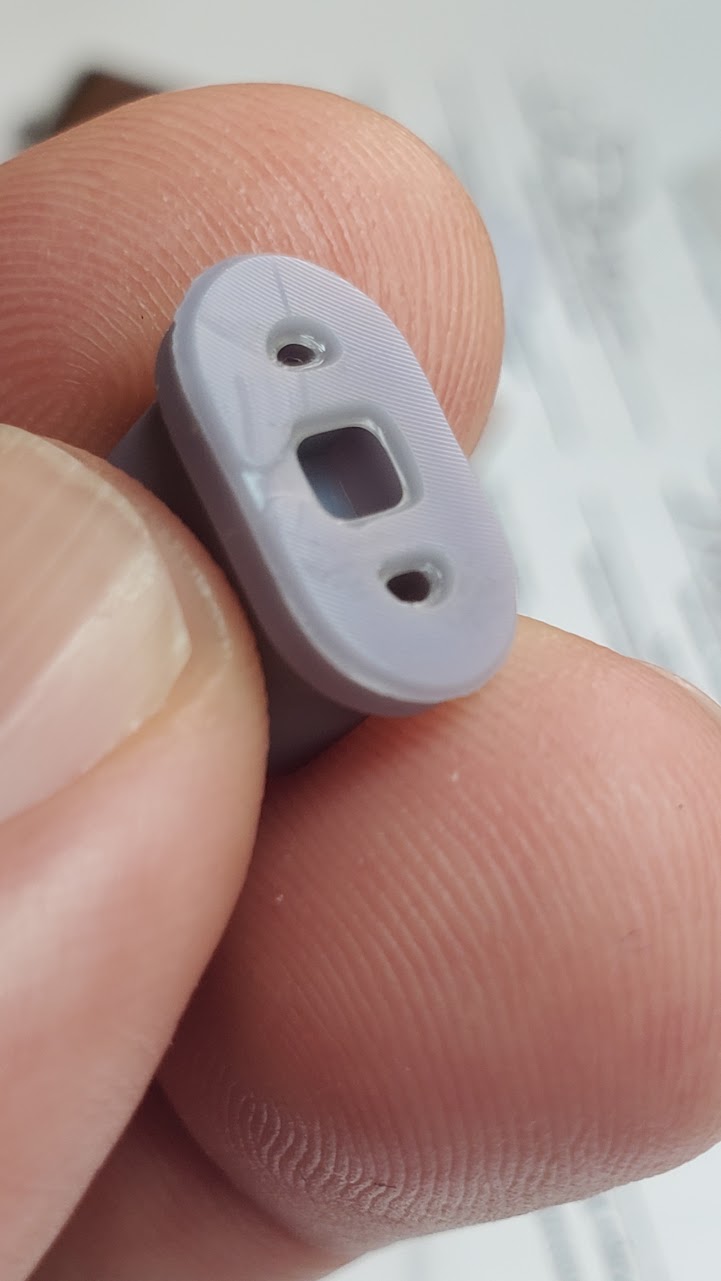
It isn't terrible on this one...but most of my tests of this switch cap were really bad. And that bottom shape needs to be accurate because these snap onto tactile switches. I've actually done these in FDM before and they work...but I had to make the openings oversized and print them in ABS and vapor smooth them to get them even close...and they still look lumpy and inconsistent so I'm not happy with them:
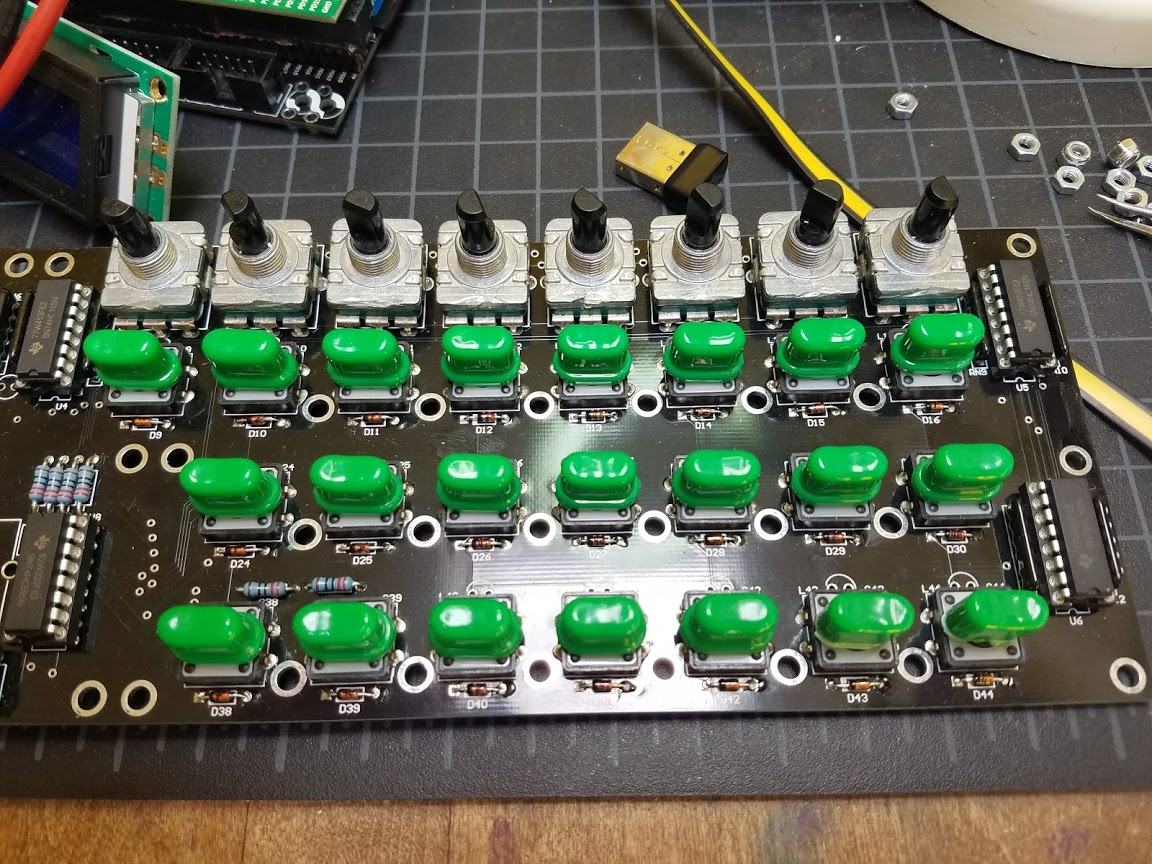
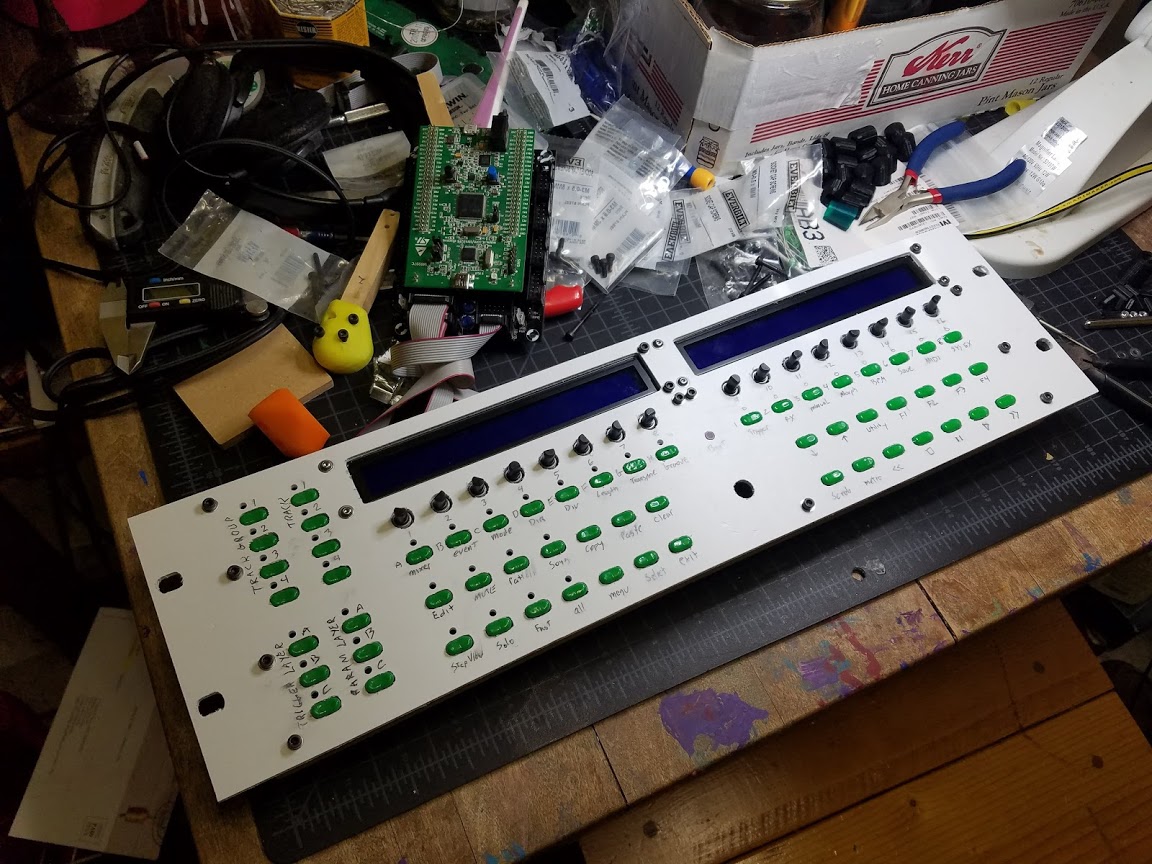
The lumpy, glossy, inconsistent buttons bug the heck out of me on this. I really want to replace them with nice clean resin prints!
So if printing right on the bed gives elephant foot and deforms the bottom...why not just add some supports?
Well...let's try "light" supports that leave the smallest marks on the print:
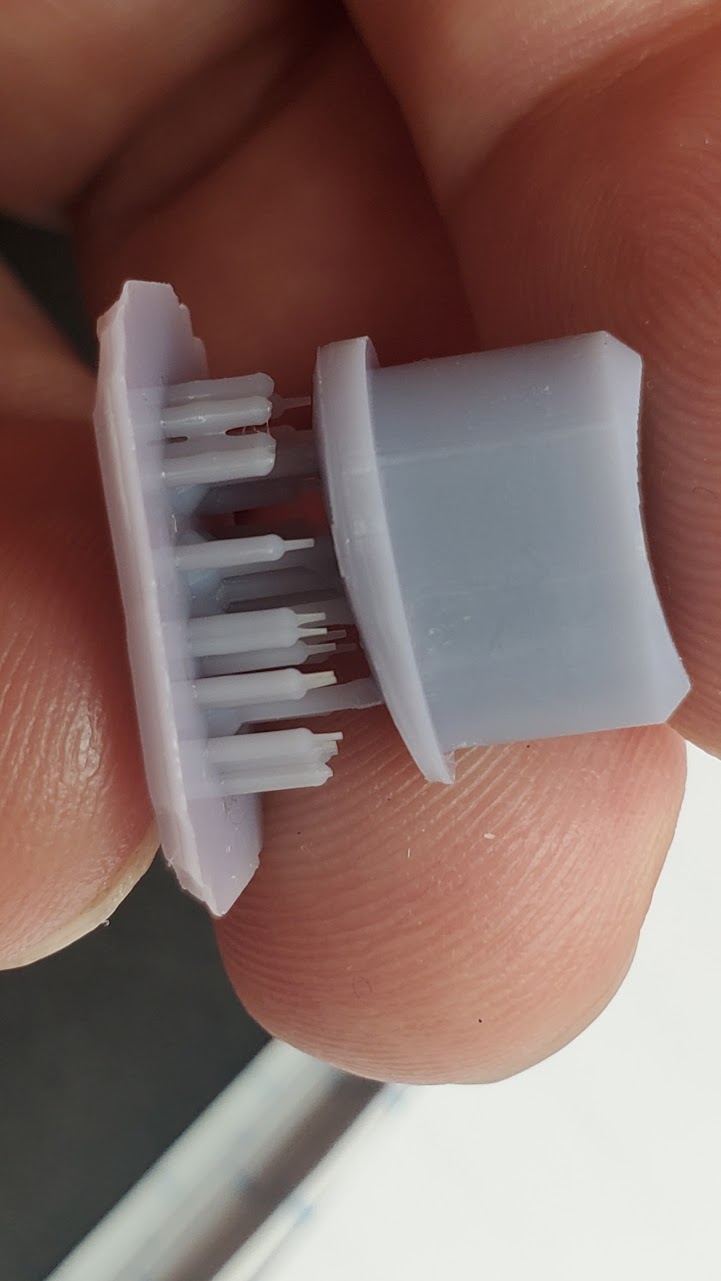
Nope...the part warped in the peel process and pulled itself off. It stayed attached enough it didn't fail...but it's deformed
Ok...what about stronger "medium" supports:
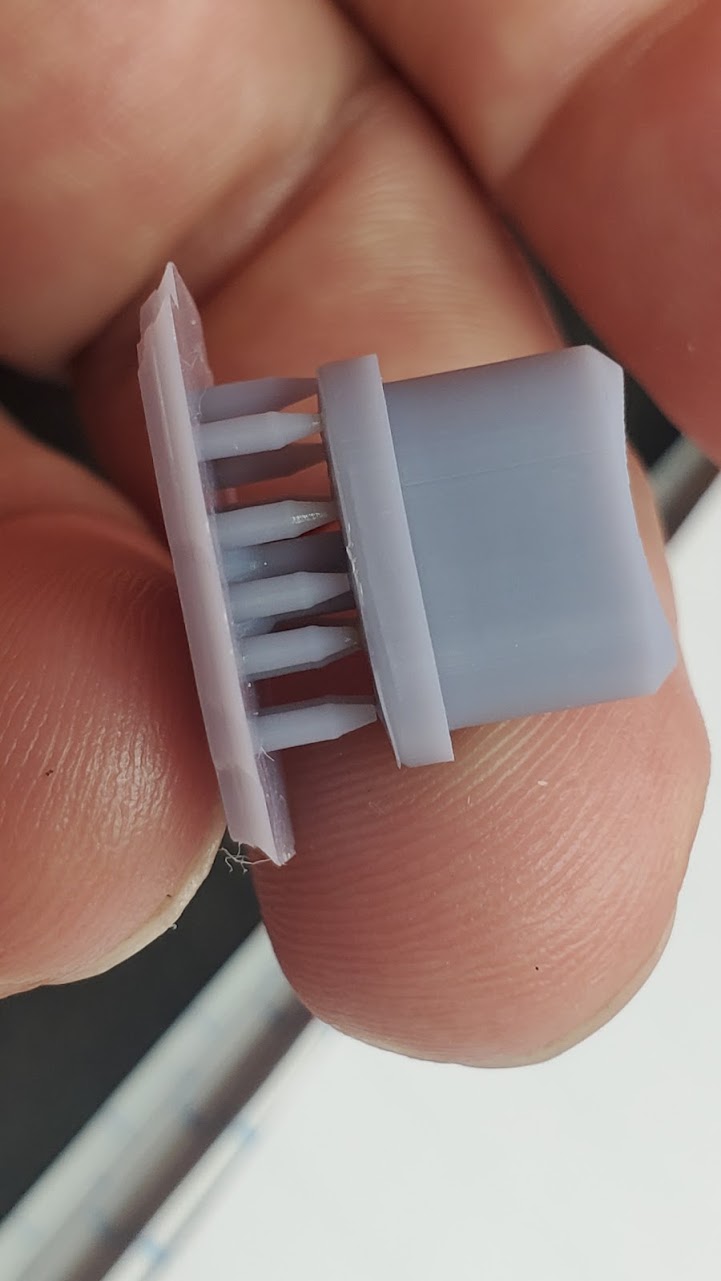
Better...but it still came off and still deformed a bit. Ok....Heavy supports!
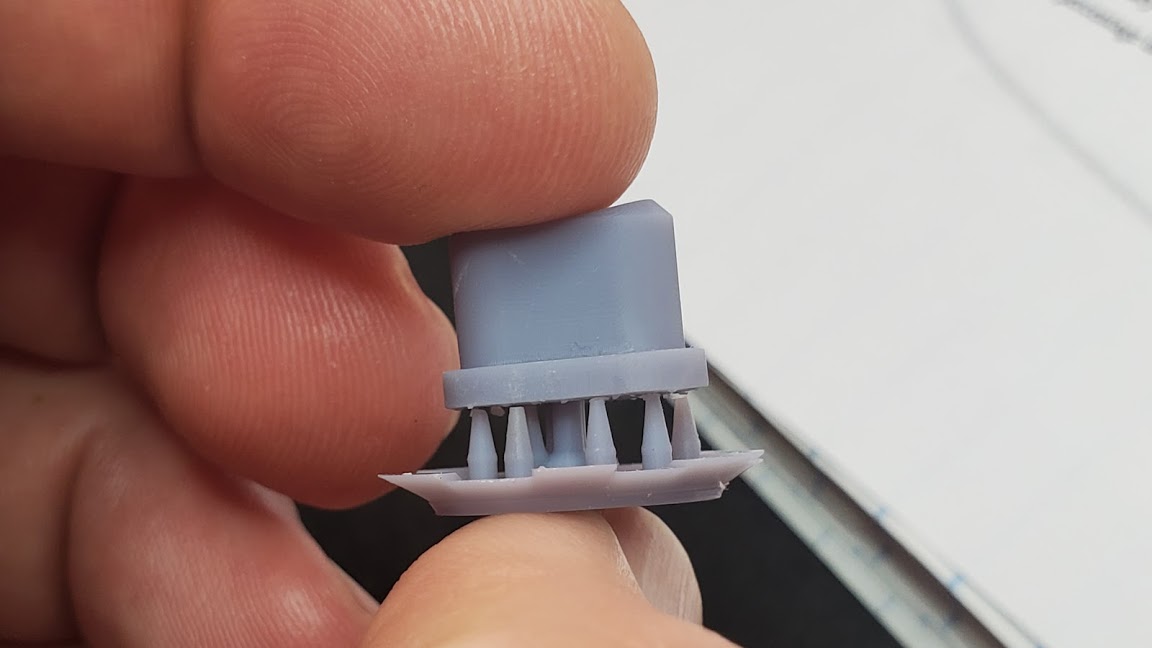
This time it stayed attached (this is after I pulled it off the supports...I'm just holding it in place to compare) but....
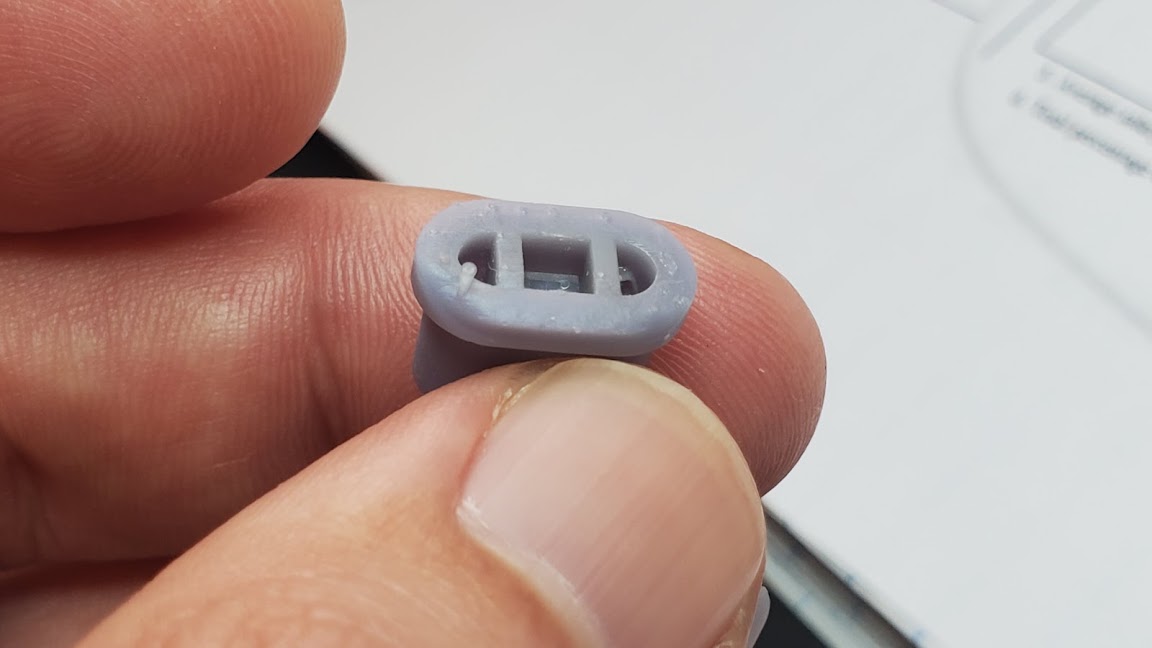
The bottom is all deformed between the supports. Again we're seeing the resin slumping as the first few layers were built up like we did with the angled knob.
I tried printing these switch caps angled as well and using supports from a different slicer...but they all came out with deformities in whatever was facing down. Adding more supports can minimize them...but then you have to remove the supports and the zits they leave...and it still doesn't result in a perfect result.
Arrgh! What can we do?