So close....this is really driving me crazy.
I took a few days off and focused on other projects, went camping and spent time enjoying my family. Then last night decided to give this another go. I think a big part of the problem I'm having is my layer fan is failing. So I'm not getting sufficient cooling and that's making the issues with printing this worse.
So I gave it another go with cura last night, I changed my layer height slightly (I had been printing at 0.25mm but 0.24 and 0.26 are a better match for the pitch of my leadscrews IIRC so I gave 0.26 a go.) I also rotated the part 45 degrees on the bed to try and make the steppers work in unison hoping it would make it less likely that one would skip. And finally...I enabled supports (ugh.)
It came out, no layer shifts! But I sliced the wrong model...this one is missing the last wire tie-down I added
Nuts, oh well. I can live without that.
At least it stayed adhered to the bed and it printed without shifting...now...let's tackle that support:
Ugh, I hate support. So much of it. It even put support in the belt paths and the little 3mm holes:
This is going to suck....but....
That actually cleaned up pretty well. The 3mm holes were a serious pain to get the support out of, but for the most part it wasn't that bad since cura does much easier to remove supports than slic3r. Unfortunately the easier looking supports in the mounting holes didn't go as well:
One of my IR sensor mounting holes broke removing it's support
And while it's less obvious so did both ears for tying wires off
Even so...I can probably live with this. At least enough to install it and use the new extruder and layer fan to print a better one.
Except....the support has come back to bite me
Can you see the problem?
The tunnels where the zip ties run to mount this to the linear bearings....it put support in them
I've tried a few things to get in there and knock out the support...but it's far enough in that I can't seem to get any kind of tool that strong enough to dislodge the support up through the curve.
Grrrr.
Going to give cura another try today...but this time with support only enabled when it touches the bed. It won't help support the top which may cause the jump at the top to come back...but hopefully the 45 degree rotation will help avoid that. It will mean the things that broke removing support won't have support and I'm fine with that since they print fine without support anyway.
Never expected it to turn into this big of a project to install this extruder
Can't get over what a pain this part is turning out to be.
If it still fails on this next try I may attempt something totally different. Go back to the original design of this mount, swap to the longer mounting screws that came with the titan, and just print a piece like this (The 2mm thick purple bit):
Which can sandwich between the extruder and mount to give me a place to mount the IR sensor. I'm not convinced that adding my IR sensor mount is what made this so hard to print...but...it was right after I added that when I started having major issues....one more go at the one piece tonight first though.
I took a few days off and focused on other projects, went camping and spent time enjoying my family. Then last night decided to give this another go. I think a big part of the problem I'm having is my layer fan is failing. So I'm not getting sufficient cooling and that's making the issues with printing this worse.
So I gave it another go with cura last night, I changed my layer height slightly (I had been printing at 0.25mm but 0.24 and 0.26 are a better match for the pitch of my leadscrews IIRC so I gave 0.26 a go.) I also rotated the part 45 degrees on the bed to try and make the steppers work in unison hoping it would make it less likely that one would skip. And finally...I enabled supports (ugh.)
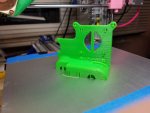
It came out, no layer shifts! But I sliced the wrong model...this one is missing the last wire tie-down I added
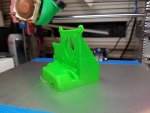
Nuts, oh well. I can live without that.
At least it stayed adhered to the bed and it printed without shifting...now...let's tackle that support:
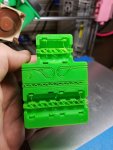
Ugh, I hate support. So much of it. It even put support in the belt paths and the little 3mm holes:
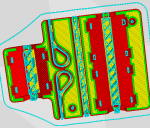
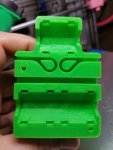
That actually cleaned up pretty well. The 3mm holes were a serious pain to get the support out of, but for the most part it wasn't that bad since cura does much easier to remove supports than slic3r. Unfortunately the easier looking supports in the mounting holes didn't go as well:
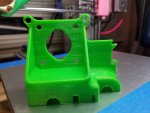
One of my IR sensor mounting holes broke removing it's support
Even so...I can probably live with this. At least enough to install it and use the new extruder and layer fan to print a better one.
Except....the support has come back to bite me
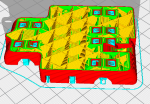
Can you see the problem?
The tunnels where the zip ties run to mount this to the linear bearings....it put support in them
I've tried a few things to get in there and knock out the support...but it's far enough in that I can't seem to get any kind of tool that strong enough to dislodge the support up through the curve.
Grrrr.
Going to give cura another try today...but this time with support only enabled when it touches the bed. It won't help support the top which may cause the jump at the top to come back...but hopefully the 45 degree rotation will help avoid that. It will mean the things that broke removing support won't have support and I'm fine with that since they print fine without support anyway.
Never expected it to turn into this big of a project to install this extruder
If it still fails on this next try I may attempt something totally different. Go back to the original design of this mount, swap to the longer mounting screws that came with the titan, and just print a piece like this (The 2mm thick purple bit):

Which can sandwich between the extruder and mount to give me a place to mount the IR sensor. I'm not convinced that adding my IR sensor mount is what made this so hard to print...but...it was right after I added that when I started having major issues....one more go at the one piece tonight first though.