Inq
Elite member
I've wanted a build challenge and as part of FTFC23, I also want a plane challenge. Not that I know anything about sailplanes... but the idea of flying on thermals captivates me. Although the build challenge starts in February, I'm guessing it's OK to do design work ahead of time since building kits from FT that are designed AND pre-cut are acceptable in the challenge.
Boomerang is a flying wing, sailplane with the following design features (at this time):
I'm allowed to change my mind due to input from any of you willing to give me constructive criticism or from the inner voices that haunt me. 
By all means... please share some of your wisdom.
Back to challenge...
Boomerang is a flying wing, sailplane with the following design features (at this time):
- Minimize weight - As I'm spec'ing two sheets of DTFB, the skin weight will be around 200 mg. I haven't analyzed for spars yet.
- Maximize span - I doubt bigger is necessarily better, but I want it big... with the two sheets of DTFB, my initial span is 3m (~120in).
- Minimize power - Although the jury is still out, I'd like to see if I can do this with a 1S power system using the all-in-one micro boards with receiver, servos and brushed ESC.
- Propeller - It will be a pusher design with folding propeller. Size TBD
By all means... please share some of your wisdom.
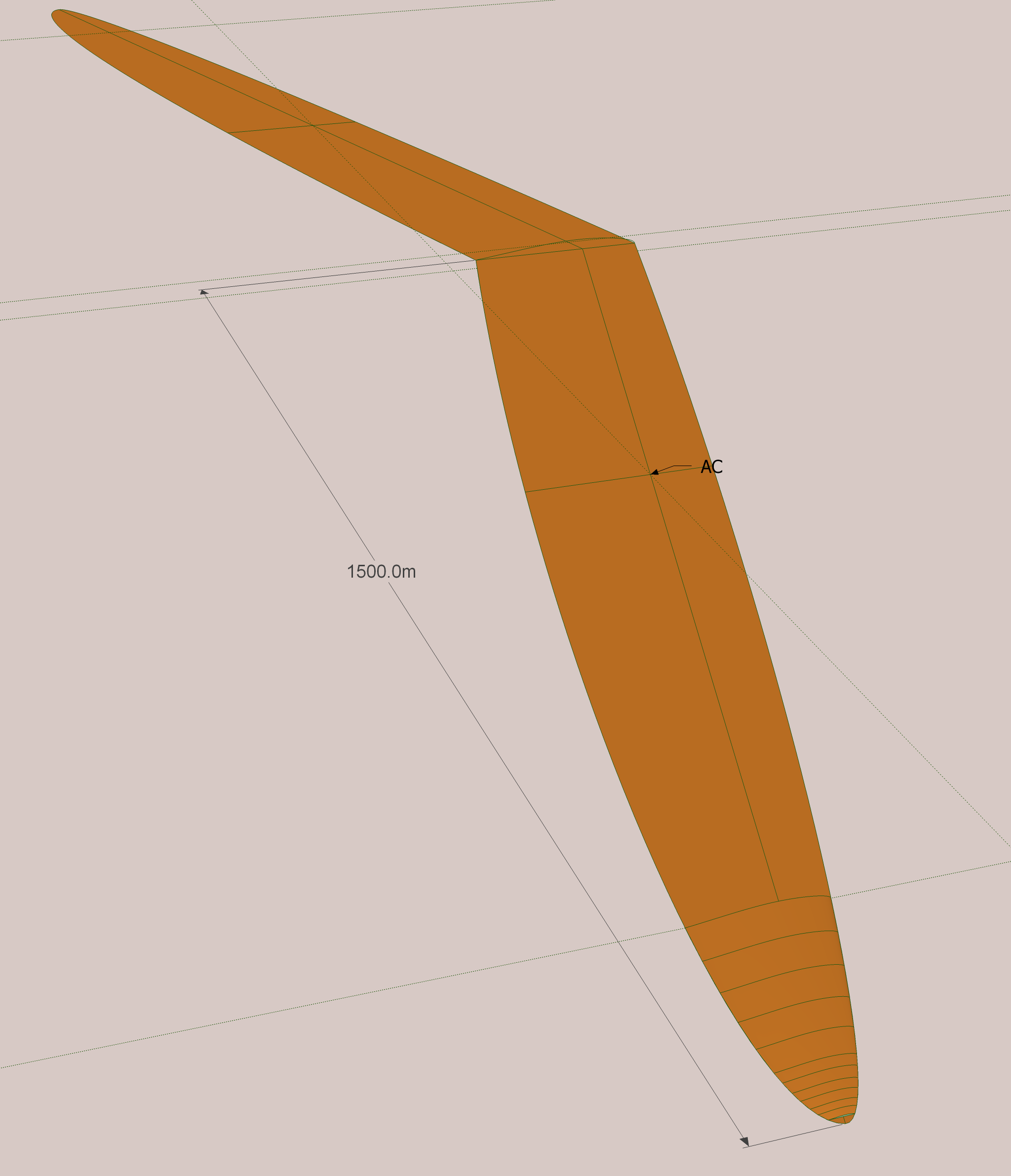
Back to challenge...
Last edited: