Mad_Mechanic
Well-known member
So I was thinking about the box spar that @BATTLEAXE made and I had an idea, let me know what you all think about this for a revised spar.
Instead of the C-fold spar, what if the wing used a "beam spar," hopefully I can explain this and why this might have some advantages.
I played around in SolidWorks and came up with this concept.
The idea here is that it would utilize the on-edge strength of foam board and at the same time it would be two pieces cut identical that include the dihedral angle in the piece. This (in theory) would simplify forming the wing. You can also run wires between the beams like a box spar.
Thoughts?
Post Edit: In terms of potential weight savings in foam board here is what it could look like. (without accounting for glue)
Version 1 C-fold spar: ~3.7 grams
Version 2 proposed Beam Spars: 2 spars at ~.9 grams each, ~1.8g total
Instead of the C-fold spar, what if the wing used a "beam spar," hopefully I can explain this and why this might have some advantages.
I played around in SolidWorks and came up with this concept.
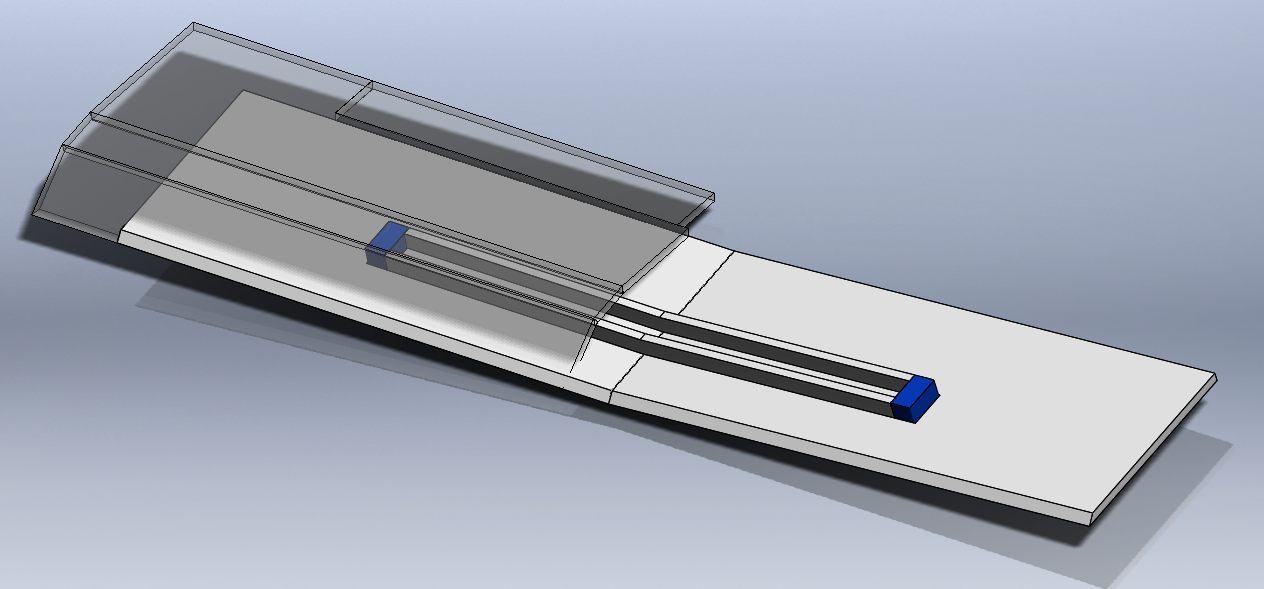
The idea here is that it would utilize the on-edge strength of foam board and at the same time it would be two pieces cut identical that include the dihedral angle in the piece. This (in theory) would simplify forming the wing. You can also run wires between the beams like a box spar.
Thoughts?
Post Edit: In terms of potential weight savings in foam board here is what it could look like. (without accounting for glue)
Version 1 C-fold spar: ~3.7 grams
Version 2 proposed Beam Spars: 2 spars at ~.9 grams each, ~1.8g total