Burnhard
Well-known member
Found a solution to keep the doors open. Stumbled across a build report from @Pieliker96 on a Caribou yesterday night. Tried that in my test set-up today and it works. Will need to work on the optics.
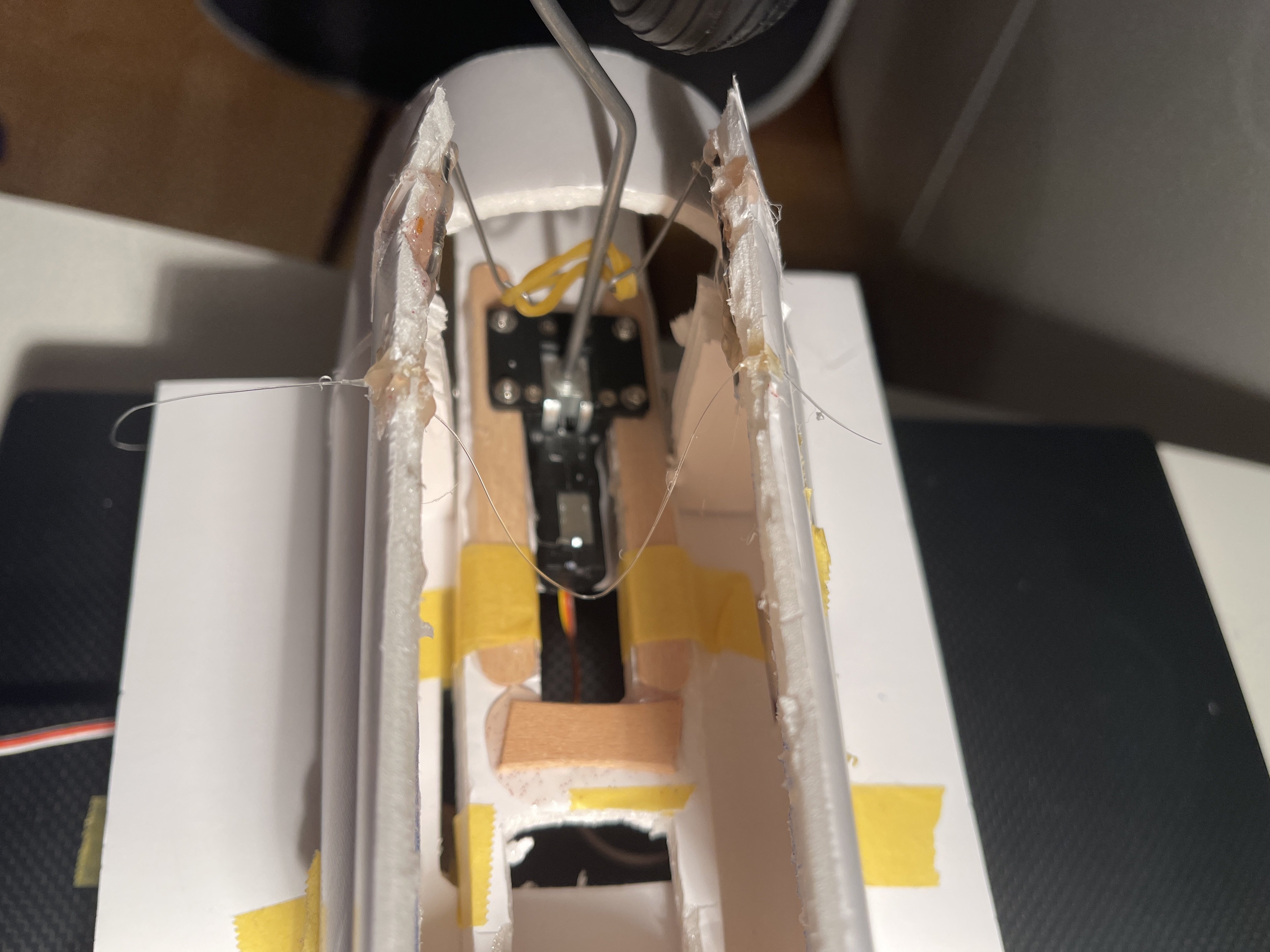
Probably need to change my design. Will do on the next one ;-)Burnt out flap servos just testing?
This does suggest that much effort is required to simply make them move regardless of any additional aerodynamic load that will arise when they are deployed in flight. Given each flap only weighs a few grams perhaps some improvement to the "mechanics" of their movement would improve their reliability.
I like to see any control surface when disconnected from its servo free enough moving so it drops under its own weight. Then I know the majority of the servo's force will be available to counter aerodynamic loads.![]()
I guess you have to be very careful with the tape. On another video I saw somebody using a small iron to round the edges but I do not have one of those. The other thing I did in the past was to sand the lower wing skin but this does not work with the speed build kits as the laser melts the foam for about 1 to 2 mm which is too much to get to a round shape. This only worked when I was hand cutting the foam board from plans. Hope the balsa solution results in less clever comments on aerodynamics at my local flying club ;-)A fella at the club added similar triangular shapes to his leading edge, claiming that it diminished his plane's nasty stall characteristics. Maybe you'll get a little added benefit beyond your smooth leading edge. I have the same issue with the MS planes.
I've been using the leading edge technique on some of the newer 13th Squadron plans (e.g. Helldiver, DH88, Betty): cutting 45* bevels on top and bottom wing sections, then using blue tape across the leading edge to hold the sections together before folding over for gluing. When it works, it makes a solid, rounded leading edge that looks sharp and is strong. On the other hand, when it doesn't (like when the tape slips a bit), it can lead to a nasty open gap on the LE that is hard to fix, so be careful if you ever try it. It is worth the effort!
Amen BrotherA dude at my flying club introduced the idea of maidening the aircraft prior to painting in case it does not fly great. I tend to ignore that advice.
I’ve got planes that were crashed several times before they finally got paint! 🤣Amen Brother
Your workmanship is first class. The flaps look great. I am anxious to hear how your first flight goes.The basic build is done! After the wing was done the next steps went reasonably quick. Almost ran out on servo ports on my 9 channel receiver. Decided to use a separate channel for each side of the flaps and also used a separate channel for the tail wheel so that I can trim it out against the rudder. Had no channel left for a working bomb bay. However I prepared one side of the lower fuselage to later include a maintenance hatch.
Next steps will be:
-filling any wrinkles and gaps with light weight filler
-making a pair of spinners from xps foam (I also got the FT spinners but the styrofoam is not to great to sand down
-thinking of a paint scheme (I like the one with the read and white tail)
-painting. The recent post from @Baron VonHelton makes me wonder whether I should get an airbrush
A dude at my flying club introduced the idea of maidening the aircraft prior to painting in case it does not fly great. I tend to ignore that advice. View attachment 224550
Quick question on the CG. Where do you measure that?Your workmanship is first class. The flaps look great. I am anxious to hear how your first flight goes.
I made my first flight today and I am pleased. I was surprised to discover that it was actually nose heavy with a 2250mah 3 cell. I checked the horizontal stabilizer and it is on the same plane as the wing so there was no pitch error there. I also switched to the servoless retracts like you have and they work well. Plane had plenty of power with the supplied motors/esc. Elevator and ailerons have lots of authority so plan on adding expo.
Now to add an FPV camera!) http://youtube.com/user/sourdough60/
Ive had many planes live their entire lives without paint! LolI’ve got planes that were crashed several times before they finally got paint! 🤣
The only plane that did not get a proper paint job is our first tiny trainer build. However the kids did a bit of pencil painting with it and after flying in snow a year ago, this now looks pretty psychedelic. Will need to find a picture of that one.Ive had many planes live their entire lives without paint! Lol
I also measured between fuselage and nacelle. With the 2250 3cell the balance point was 83 mm. THAT was the configuration on the first flight and it required all the nose-up trim I had to trim it level. So, the proper C/G should be something more like the 66.7mm.Quick question on the CG. Where do you measure that?
I measured between the fuselage and the nacelle. With a 4S 3400 it seems to balance just after the recommended 66,7mm. There is no way mine would balance even close the recommended CG with a 3S 2200.