Hi all,
so my first fory in to quad building is to make a carbon fibre mico drone frame out of 1mm CF sheet, but I would be grateful for some advice in two areas.
First of all here is a link to some 3D modeling I have done on the frame.
https://gallery.autodesk.com/fusion360/projects/micro-drone-carbon-fiber-fpv-upgrade
So far one major thing i found out was direction of weave is crucial!! 3-5mm arms are fine as long as the weave is along the arm and not across it!
and there have been a few revisions all to do with learning 3D package, Carbon fibre and various other bits. But I would apriciate some help one a few points.
1. Cutting thin CF sheet, I have been using a dremel on a small drill stand. Locking down a 0.6 mm grinding/routing bit and pushing the sheet aginst it. IT does work but if there is any one in the UK that has a CNC mill and like to cut small bits of thin carbon fiber sheet I might be interested in some help for future projects
2. What is the best way to glue thing carbon fiber sheet together. I have tried Cyanoacrylate, epoxy glues and finishing resin, with the last by far the best. But its still not a brilliant bond when its one sheet edge on. I do need a fairly strong join on this project so if any one has some suggestions on some methods to try I would be most grateful.
Cheers
### EDIT ###
Tips I have picked up.
1. with thin CF sheet (1mm) the arms need to be cut inline with the weave. For a drone that only weights 50-70g 1mm sheet is plenty strong enough. However CF bends very easly across the weave, but is very stiff in line with it. for an arm 3-5mm in width and with only a single layer you need to know what direction you need the stiffness in!
2. To glue thin CF sheeting togather like this (edge to face) use a finishing resin ( I used Zap z-proxy finishing resin). Mix as directed but I also mixed in a good amount of carbon fiber dust from when I was cutting the sheet. Also make sure to rough up the surfaces. My methods was to mix the resin with out the Carbon fiber dust in it, then apply a thin coat of this to the both surfaces. then mix in the dust to the rest. then I would leave for about 20-30 minutes until it started to thicken and apply it at this stage to help hold the parts in place. This way the first coat will still runny would bind well to the surfaces, and the thicker resi later on would mean more stayed on the joints and over all there was a much stronger bond.
3. To cut thin Carbon fiber by hand is a pain, so I came across this on youtube, the bit he suggests is perfect to make nice easy clean cuts. If you have a dremel though dont but there stand as from all reports it is poorly made and not stable. there are many others around that will hold a dermal. just get one that is rock steady, moves up and down cleanly, and that you can lock in the down position.
If I think of any thing else I will put it here also.
so my first fory in to quad building is to make a carbon fibre mico drone frame out of 1mm CF sheet, but I would be grateful for some advice in two areas.
First of all here is a link to some 3D modeling I have done on the frame.
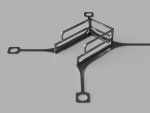
https://gallery.autodesk.com/fusion360/projects/micro-drone-carbon-fiber-fpv-upgrade
So far one major thing i found out was direction of weave is crucial!! 3-5mm arms are fine as long as the weave is along the arm and not across it!
and there have been a few revisions all to do with learning 3D package, Carbon fibre and various other bits. But I would apriciate some help one a few points.
1. Cutting thin CF sheet, I have been using a dremel on a small drill stand. Locking down a 0.6 mm grinding/routing bit and pushing the sheet aginst it. IT does work but if there is any one in the UK that has a CNC mill and like to cut small bits of thin carbon fiber sheet I might be interested in some help for future projects
2. What is the best way to glue thing carbon fiber sheet together. I have tried Cyanoacrylate, epoxy glues and finishing resin, with the last by far the best. But its still not a brilliant bond when its one sheet edge on. I do need a fairly strong join on this project so if any one has some suggestions on some methods to try I would be most grateful.
Cheers
### EDIT ###
Tips I have picked up.
1. with thin CF sheet (1mm) the arms need to be cut inline with the weave. For a drone that only weights 50-70g 1mm sheet is plenty strong enough. However CF bends very easly across the weave, but is very stiff in line with it. for an arm 3-5mm in width and with only a single layer you need to know what direction you need the stiffness in!
2. To glue thin CF sheeting togather like this (edge to face) use a finishing resin ( I used Zap z-proxy finishing resin). Mix as directed but I also mixed in a good amount of carbon fiber dust from when I was cutting the sheet. Also make sure to rough up the surfaces. My methods was to mix the resin with out the Carbon fiber dust in it, then apply a thin coat of this to the both surfaces. then mix in the dust to the rest. then I would leave for about 20-30 minutes until it started to thicken and apply it at this stage to help hold the parts in place. This way the first coat will still runny would bind well to the surfaces, and the thicker resi later on would mean more stayed on the joints and over all there was a much stronger bond.
3. To cut thin Carbon fiber by hand is a pain, so I came across this on youtube, the bit he suggests is perfect to make nice easy clean cuts. If you have a dremel though dont but there stand as from all reports it is poorly made and not stable. there are many others around that will hold a dermal. just get one that is rock steady, moves up and down cleanly, and that you can lock in the down position.
If I think of any thing else I will put it here also.
Last edited: