AeroEngineer20
New member
Hello all! My name is Andrew, and I am a university student majoring in Mechanical Engineering. I've been watching FliteTest for quite a while now and have been inspired by their designs and their attitude toward the hobby. I think it's safe to assume that I am not the only one here who has found my way into the hobby through them, and for that I'm very grateful.
I have a few projects I've been working on, but I'll introduce my biggest one first. In May of 2017 I decided I wanted to build a hobby-sized turbojet engine from scratch, with every part being made by me. I was confident in my modelling abilities through my experience with Blender and Autodesk products, but I had relatively little experience in CNC machining other than 2D plasma cutting. For a project like this I would have to learn, so I made friends with my university's shop manager. He got me up to speed on physically operating the machines, and gave me guidance on methods and rules of CNC machining, spring boarding from my manual machining experience in high school. I also joined the local EAA chapter, who lets me use their TIG welder as a member.
Since May, I've been working on it every chance I get. My ultimate goal is to have a test run before April 17th, my 20th birthday. While it is still a work-in-progress, I am now comfortable with sharing it outside my local friend group. Even if it doesn't work, the process of designing and machining is invaluable experience gained.
I have glossed over the majority of the process and details in the interest of maintaining some kind of brevity, so If you have any questions, feel free to reply!
Section View:
Progress so far:
Cast and partially machined intake:
Diffuser and stator vanes:
Compressor machining (roughing stage):
Turbine (right) and turbine nozzle (left):
Turbine nozzle machining:
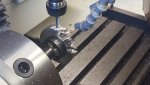
I have a few projects I've been working on, but I'll introduce my biggest one first. In May of 2017 I decided I wanted to build a hobby-sized turbojet engine from scratch, with every part being made by me. I was confident in my modelling abilities through my experience with Blender and Autodesk products, but I had relatively little experience in CNC machining other than 2D plasma cutting. For a project like this I would have to learn, so I made friends with my university's shop manager. He got me up to speed on physically operating the machines, and gave me guidance on methods and rules of CNC machining, spring boarding from my manual machining experience in high school. I also joined the local EAA chapter, who lets me use their TIG welder as a member.
Since May, I've been working on it every chance I get. My ultimate goal is to have a test run before April 17th, my 20th birthday. While it is still a work-in-progress, I am now comfortable with sharing it outside my local friend group. Even if it doesn't work, the process of designing and machining is invaluable experience gained.
I have glossed over the majority of the process and details in the interest of maintaining some kind of brevity, so If you have any questions, feel free to reply!
Section View:
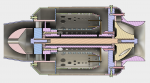
Progress so far:
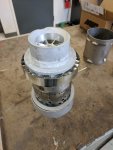
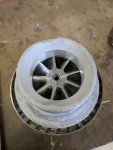

Cast and partially machined intake:
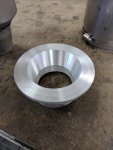
Diffuser and stator vanes:
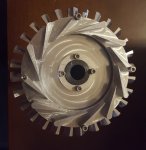
Compressor machining (roughing stage):
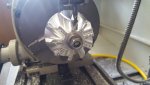
Turbine (right) and turbine nozzle (left):
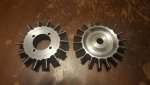
Turbine nozzle machining:
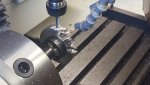