Pigfarm1403
Builder
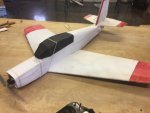
-Inspiration
So after finally sorting through all of my stuff from flitefest ohio I was inspired by the clean workspace and organized parts to design my first plane. I have a couple of year of building and I have done a variety of giant builds but I would hardly call those "designs". Some of you might have heard or even seen the hobbyzone v900. The v900 is an extremely fast (120mph) propdriven rc plane that I first encountered at a combat at FFO, when it split my plane in half, since then my interest in faster planes has grown. A month back I bought the flyzone l39 which can hit speeds upwards of 90mph but I would still like to break the 100mph barrier, and so it begins.....
-Overview
After about 8hrs of work I created a durable speed platform I call the "low-wing python". I does not hit near 100mph at this point because it is only the first version of the series I plan on making. I would say confidently that at its current state it can beat any ft plane in speed contest with a power pack c. Key features give it this speed which include the heavily swept back and short wing, no under-chamfered wingtips, and less boxier pieces made out of lowes foamboard, particularly the wingtips and engine cowling. The plane uses a C-pack motor but I am more than likely going to need to upgrade the motor in order to reach 100mph on later versions.
-Electronics/power system
Motor: powerpack c
ESC: 30amp esc
Prop: 10x4.5
Batttery: 3s 1600mah/ 4s which is bad but its fun :^)
Servo: stardard 9g servos
Tx/RX: Flysky fsai6x
-Build
Wing: Unfortunately I forgot to take pictures of the interior of the wing but it is pretty basic. i have two layers of foamboard as formers for the wing and three wooden spars, two for the wingtips and one for the wing joint. For the ailerons I did something a little different and cut out a small area for the ailerons instead of extending the trailing edge. The servos for the ailerons are covered by a layer of water resistant paper from excess foam and the servo wires lead to the fuselage on the exterior of the wing, something I will change in another version.
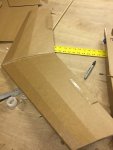
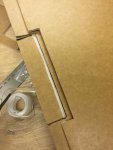
Body: I wanted to have a very sturdy body because I knew I was going to crash this plane and I wanted it to be a durable platform for speed tests. So for the tail of the plane I put in a couple of square formers to help the tail keep its shape after a crash and it worked very well. Another thing I did to make the frame sturdy is I doubled up the nose section so it wouldn't bend side to side if it got worn out. Unfortunately this plane isn't swappable but I am okay with that. One thing I also wanted to do is have a very easy to access area for my electronics so I made the canopy removable and I can store my receiver and battery in the same spot without having to take much of anything apart. The tail controls are very basic and in the second version I plane on moving the elevator servo inside the fuselage and repositioning the rudder servo so I don't have to run the control rod through the elevator.
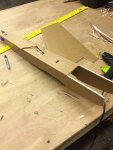
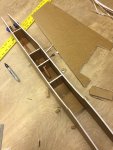
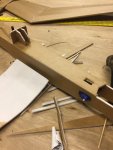
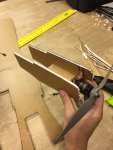

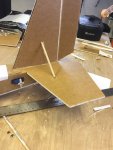
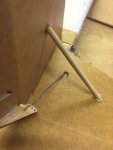
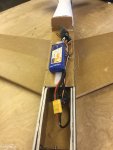
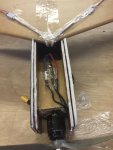
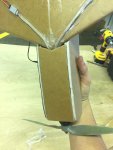
Aesthetics: I went with a simple paint scheme, red, white, and black, and I made more detailed pieces with Lowes 1inch foam-board that i trimmed down and sanded
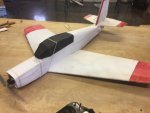
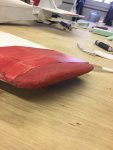
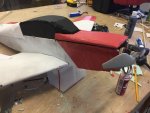
-Changes in v2
Body: I am pretty happy with the body and the only change I plan on making is rearranging the servo locations
Wing: In this build i knew my wing wouldn't be the fastest I just wanted to get it in the air, so this is where the next plane will get some more speed. Currently the wing is 12mm which which doesn't sound like much but for a fast place that really thick. This next wing will have a thickness of 9mm to make it sleeker. i also plan on bringing the wingtips out to a point like in the NN Mig 3.
I am VERY happy with the way that this build went and I will definetly build newer faster version and hopefully I will eventually break 100mph with this platform. If enough people ask me to I will work on a set of digital plans but I would need some assistance with reverse engineering the plane. Keep an eye out on this thread because there is more to come and any input would be grealty apreciated. Thanks!
Attachments
Last edited: