Yeah, I thought about wire. Then figured, it'll be fine for this one test until I can get the motor angle set. Dumb mistake.
Got several new motors coming, and some other odds and ends. Copied the baby blender landing gear, just way scaled down. Used a piece of push rod wire.
A bit of hot glue, and then a piece of extreme packing tape to hold it all down. Didn't want to go adding any more weight from zip ties. We'll see what happens.
Got several new motors coming, and some other odds and ends. Copied the baby blender landing gear, just way scaled down. Used a piece of push rod wire.
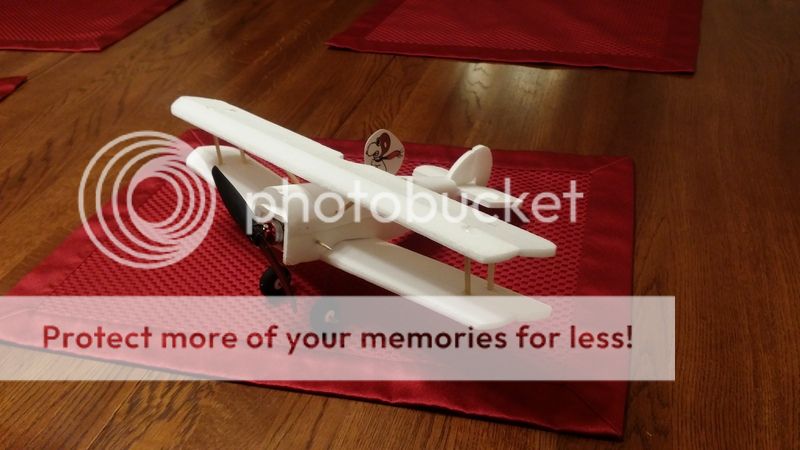
A bit of hot glue, and then a piece of extreme packing tape to hold it all down. Didn't want to go adding any more weight from zip ties. We'll see what happens.
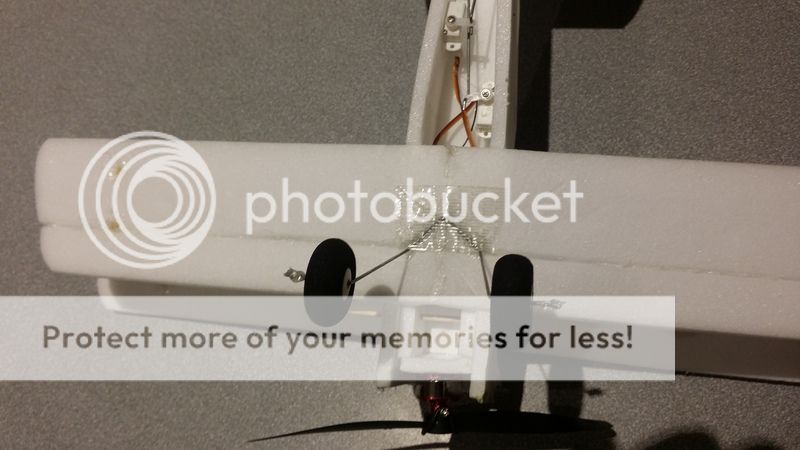