Started drawing one of these up last night:
I need electronics and some odds and ends to finish the Bf 109, so it was either get extra work done in the evening or have some fun. So far, I've done two Axis powers War Birds to balance out the Mighty Mini P-51 and Corsair. I think that the Mighty Mini lineup was about due for a biplane fighter. There's just something about biplanes, and the Gloster Gladiator is a beautiful plane.
It's also got a rather interesting history. It was the last biplane fielded by the RAF, and the first fighter to have an enclosed cockpit. It was put into the field just as monoplanes were starting to dominate, and as such, it went to export very quickly. The number of countries that fielded the Gladiator was kinda crazy. The first recorded kill in WWII from a Gladiator, was a US pilot in China who shot down a Mitsubishi A5M.
If I remember correctly, there were a couple squadrons involved in the Battle of Britain, where they were way overmatched. In many of the other theatres, they held their own, or dominated the skies. So many different countries ended up with them, that several ended up on the Axis side, and I believe even the Russians ended up with one.
Here's one outfitted for snow:
So, on to the plans:
Drawn up with a 24.25" Wingspan, and should be compatible with the F power pack. It will use the standard mighty mini power pod. This isn't really out of line for size. For instance, the real life Bf 109 has a wingspan of 33 feet, and the Gladiator has a wingspan of 32'.
I didn't realize it at the time, but this is the same wingspan as the baby blender. However, with the more refined build techniques, this plane will be far, far, lighter. I'm also going for a thin semi-symmetrical airfoil. This in combination with the rounded wing tips should induce far less drag. The under camber on the tips may add some of that drag back, but I believe it will do a lot to enhance stability.
The fuselage design is something new I'm testing out. Lots of paper has been removed from many parts, including the fuse. For the tail section, I plan to only include as much foam board as necessary for strength. The rest of the skin of the plane will be poster board. Should be just as easy to assemble as any other FT style plane, it will just have the added benefit of lightness and a more accurate rounded fuse. I'm hoping for a bare airframe weight increase of only 25% (it may be less) from the current monoplane mighty mini warbirds. All while doubling the wing area.
Of course, it will have a hatch to hide the batteries in, and will be getting the full clear canopy treatment. I'm also testing out a better method of creating a round cowl with a smooth rounded transition in the front. Got some goodies from the minwax isle to play with. I'm hoping that a very smooth cowl can be created with very little work.
If all goes well, this one should be slow enough, and agile enough to actually fly indoors.
********************************************************************************
Latest beta plans:
Mighty Mini Gloster Gladiator Beta v.4 Tiled
Mighty Mini Gloster Gladiator Beta v.4 Full
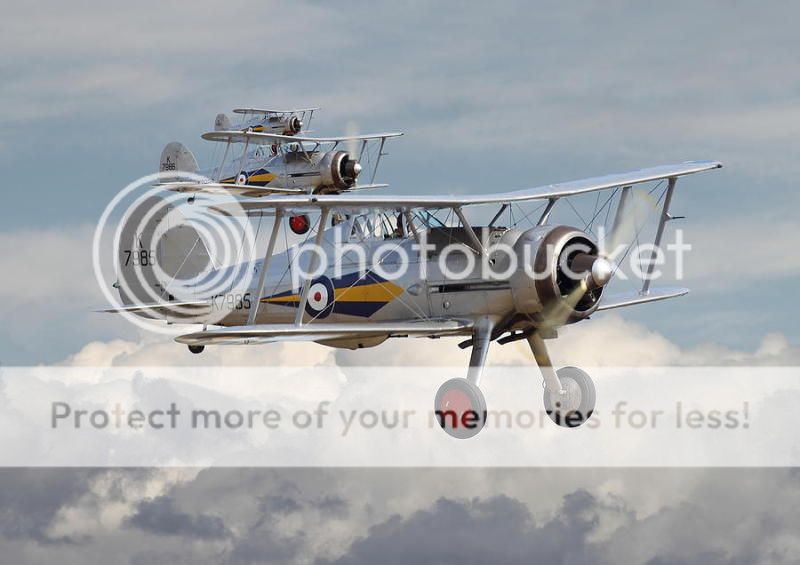
I need electronics and some odds and ends to finish the Bf 109, so it was either get extra work done in the evening or have some fun. So far, I've done two Axis powers War Birds to balance out the Mighty Mini P-51 and Corsair. I think that the Mighty Mini lineup was about due for a biplane fighter. There's just something about biplanes, and the Gloster Gladiator is a beautiful plane.
It's also got a rather interesting history. It was the last biplane fielded by the RAF, and the first fighter to have an enclosed cockpit. It was put into the field just as monoplanes were starting to dominate, and as such, it went to export very quickly. The number of countries that fielded the Gladiator was kinda crazy. The first recorded kill in WWII from a Gladiator, was a US pilot in China who shot down a Mitsubishi A5M.
If I remember correctly, there were a couple squadrons involved in the Battle of Britain, where they were way overmatched. In many of the other theatres, they held their own, or dominated the skies. So many different countries ended up with them, that several ended up on the Axis side, and I believe even the Russians ended up with one.
Here's one outfitted for snow:
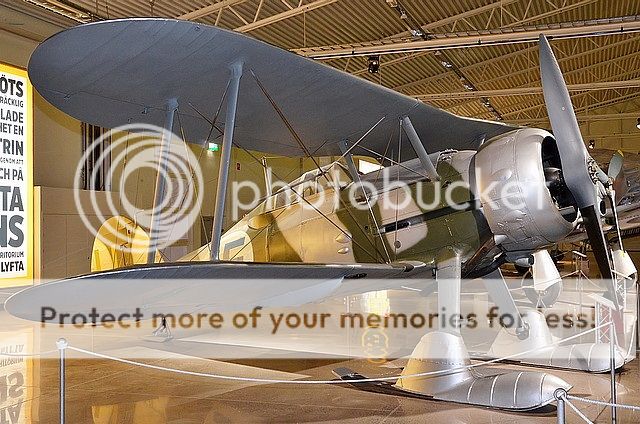
So, on to the plans:
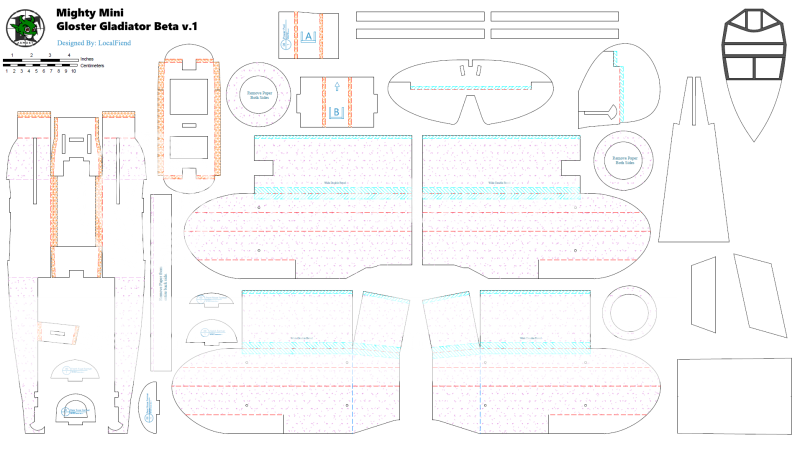
Drawn up with a 24.25" Wingspan, and should be compatible with the F power pack. It will use the standard mighty mini power pod. This isn't really out of line for size. For instance, the real life Bf 109 has a wingspan of 33 feet, and the Gladiator has a wingspan of 32'.
I didn't realize it at the time, but this is the same wingspan as the baby blender. However, with the more refined build techniques, this plane will be far, far, lighter. I'm also going for a thin semi-symmetrical airfoil. This in combination with the rounded wing tips should induce far less drag. The under camber on the tips may add some of that drag back, but I believe it will do a lot to enhance stability.
The fuselage design is something new I'm testing out. Lots of paper has been removed from many parts, including the fuse. For the tail section, I plan to only include as much foam board as necessary for strength. The rest of the skin of the plane will be poster board. Should be just as easy to assemble as any other FT style plane, it will just have the added benefit of lightness and a more accurate rounded fuse. I'm hoping for a bare airframe weight increase of only 25% (it may be less) from the current monoplane mighty mini warbirds. All while doubling the wing area.
Of course, it will have a hatch to hide the batteries in, and will be getting the full clear canopy treatment. I'm also testing out a better method of creating a round cowl with a smooth rounded transition in the front. Got some goodies from the minwax isle to play with. I'm hoping that a very smooth cowl can be created with very little work.
If all goes well, this one should be slow enough, and agile enough to actually fly indoors.
********************************************************************************
Latest beta plans:
Mighty Mini Gloster Gladiator Beta v.4 Tiled
Mighty Mini Gloster Gladiator Beta v.4 Full
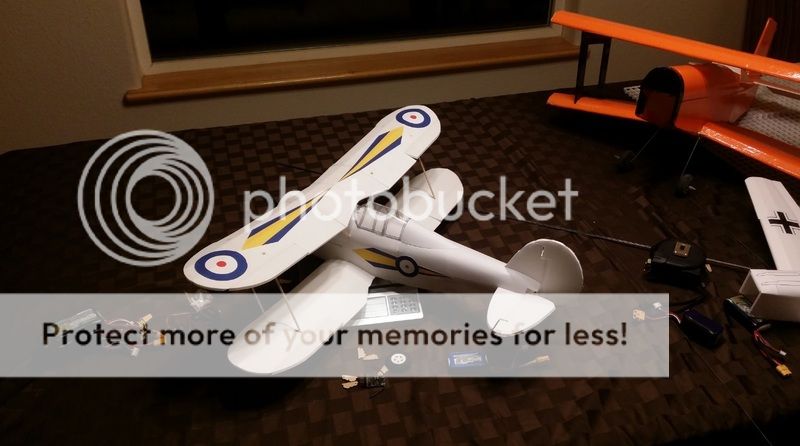
Last edited: